Firma ES3 LLC we współpracy z SSI SCHAEFER oraz C&S Wholesale Grocers przeprowadziła kolejną automatyzację swojego centrum dystrybucyjnego w York, Pennsylvania/USA. ES3 wybrało Case Picking System (SCP) SSI SCHAEFER – wyróżnione nagrodą rozwiązanie, które gwarantuje wysoką wydajność zautomatyzowanych procesów od wpływu aż po wysyłkę towaru.
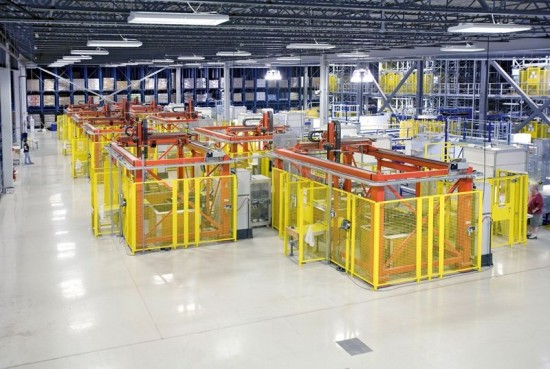
Obniżenie kosztów, wzrost wydajności, serwis na najwyższym poziomie – to cele na których skupia się ES3 LLC podczas optymalnej paletyzacji. Istotą projektu była dalsza automatyzacja magazynu. Rozbudowę centrum dystrybucyjnego firma ES3 LLC podjęła we współpracy z firmą SSI SCHAEFER, która otrzymała zlecenie na stworzenie koncepcji logistycznej, planu realizacji oraz samą realizację projektu.
W 2002 roku firma ES3 zajęła magazyn, który w ostatnich latach stał się jednym z największych magazynów artykułów spożywczych w Stanach Zjednoczonych. Ponad 20 000 różnych artykułów, produktów spożywczych oraz artykułów gospodarstwa domowego magazynowanych jest w kompleksie o powierzchni ponad 14 000 m kw.
Produkty dostarczane są od producentów, komplementowane wg. poszczególnych filii i przekazywane odpowiednim dystrybutorom. Dennis Senovich, Prezes Zarządu ES3, wyjaśnia istotę największego wyzwania: - Trendy branżowe idą w kierunku coraz większej liczby identyfikatorów SKU przy niewielkiej rotacji magazynu. SCS jest technicznie najbardziej dopracowanym systemem automatycznym, który kompleksowo rozwiązuje problemy pojawiające się podczas komplementacji oraz paletyzacji.
ES3 szukało kompaktowego, globalnego rozwiązania, które umożliwi nie tylko automatyzację procesów magazynowych, ale zautomatyzuje także procesy komplementacji zamówień oraz przygotowania do wysyłki. Optymalnym rozwiązanie dla zaplanowanej rozbudowy stało się połączenie dwóch systemów: Schaefer Case Picking (SCP) i Schaefer Tray System (STS). Rozwiązanie to oferuje prawie 90 000 lokalizacji (tacek) o różnej klasie wysokości w magazynie wysokiego składowania SCP. Przepływ materiału i stacje komplementacji zamówień znajdują się na różnych poziomach, co umożliwia przerób 100 000 kartonów dziennie. ES3 dysponuje dzięki temu jednym z największych, najnowocześniejszych i najbardziej wydajnych automatycznych systemów Case Pick w USA.
- System Schaefer Case Picking jest globalnym, modułowym rozwiązaniem, które może być dowolnie rozbudowane - wyjaśnia Christoph Schenk, przedstawiciel SSI SCHAEFER odpowiedzialny za realizację projektu. - Dzięki temu mogliśmy stworzyć zautomatyzowane rozwiązanie, które obejmuje procesy od wpływu towaru przez magazynowanie, aż po paletyzację. Fizyczne prace magazynowe, które do tej pory obciążały pracowników, nie wchodzą już w grę. W ogromnej strefie SCP wystarczy jedynie 12 pracowników podczas jednej zmiany, którzy zajmują się przede wszystkim sterowaniem lub konserwacją systemu.
W ES3 zainstalowano 3-modułowo skonstruowane systemy Schäfer Case Picking, system zarządzania magazynem „ant” oraz generator palet „Schäfer Pack Pattern Generator (SPPG)”. We współpracy z danymi z WMS, Schäfer Pack Pattern Generator oblicza w krótkim czasie optymalny układ palet. Dzięki tym informacjom WMS automatycznie steruje procesy paletyzacji.
Koncepcja strefy SCP zakładała, że procesy związane z przepływem materiału w strefie dostaw, magazynowania i wysyłki zostaną konsekwentnie rozszczepione i podzielone na 3 poziomy. Na środkowym poziomie znajduje się strefa dostaw (wpływu towaru), gdzie artykuły dostarczane są na paletach – nawet do 1 300 palet dziennie.
Bramki świetlne, wagi oraz kamery oparte na technologii Machine Vision pomagają w ustaleniu wagi oraz wyglądu produktów oraz tworzą wzór paczki do bazy danych. Optyczny system kontroli, który stosowany jest również podczas kompletacji zleceń w SCP sprawia, że dalsze, wewnętrzne znakowanie, jak np. etykiety z kodami kreskowymi, nie jest już konieczne. Po pobraniu artykułów palety przekazywane są na krótki odcinek przenośnika, który kieruje je do dwóch robotów depaletyzujących. Roboty pobierają kartony z palety i ustawiają je na tackach, znajdujących się na przenośniku – na tacce mieści się przeciętnie 16 kartonów.
Tacki przenoszone są na przenośniku do sześciu miejsc zdawczych, na których następuje załadowanie do magazynu wysokiego składowania. System informatyczny kieruje tacki zgodnie z ich zawartością.
SSI SCHAEFER nie wykorzystuje do załadowania magazynu wysokiego składowania, składającego się z 36 korytarzy, tradycyjnych układnic. W większości przypadków stosowane są systemy windowe lub wózki regałowe, umożliwiające kompaktowe wykorzystanie przestrzeni oraz redukcję pustej przestrzeni w regale. Zintegrowane windy przenoszą tacki na odpowiedni poziom do miejsc zdawczych, po czym transport tacek przejmują wózki regałowe. Rozszczep transportu poziomego i transportu pionowego sprawia, że instalacja jest bardzo dynamiczna i wydajna. System wznosi się 24 metry w górę i oferuje prawie 90 000 lokalizacji w kilku korytarzach. Dzięki temu osiąga najwyższą z możliwych dynamikę komisjonowania.
Potrzeby klientów i wysokie standardy obsługi to podstawy przemysłu spożywczego. Ważna jest także odpowiednia dystrybucja palet do poszczególnych filii. - System SCP firmy SSI SCHAEFER daje dokładnie takie możliwości, dzięki którym realizacja procesów od wpływu, aż po wysyłkę towaru jest w pełni zautomatyzowana, a co za tym idzie efektywna - mówi Schenk. - W York system został skonstruowany stosownie do bogatego asortymentu i różnorodności artykułów, które ES dystrybuuje do C&S i innych klientów - tacki o wymiarach 120x100 cm i obciążeniu nawet do 230 kg na lokalizację.
Rozładowanie następuje za pomocą 48 wind regałowych Case-Wheeler, które są zintegrowane z systemem SCP i sterowane poprzez system zarządzania magazynem. Windy opracowują tacki pod względem ich zawartości pod konkretne zamówienia. - Niezwykła cecha koncepcji SCP - mówi Schenk. - Podczas gdy konwencjonalne regały mogą być obsługiwane wyłącznie od czoła, system SCP zwiększa wydajność poprzez maksymalne obciążenie dowolnej ilości wózków regałowych, obsługujących regały na całej ich długości.
Tacki są rozładowywane przez wózki z regałów STS (Schaefer Tray System) i przejmowane przez windy Case-Weeler – nawet do 4 500 tacek na godzinę. Windy przenoszą następnie tacki do oddzielnego poziomu komplementacji. Tam ilość artykułów rejestrowana jest dzięki technologii Maschine Vision (widzenie maszynowe) i dobierana jest odpowiednia ilość kartonów (na podstawie obliczonego przez komputer wzoru), które transportowane są do jednego z trzech umiejscowionych jeden nad drugim tzw. poziomów Shoot-out. Jedną z trzech linii transportowych obsługują trzy roboty paletyzujące w poszczególnych częściach SCP. W ten sposób kartony obsługiwane są przez dziewięć robotów paletyzujących poszczególne zamówienia.
Po prawej i lewej stronie robotów znajdują się puste palety, które pakowane są jedna po drugiej. System ma przy tym wydajność nawet do 74 palet na godzinę i 5 350 jednostek. We wzorach wyznaczonych przez system informatyczny wzięto pod uwagę rodzaje produktów. Odpowiednia selekcja sprawia, że produkty chemiczne nie zostaną zapakowane np. razem z artykułami spożywczymi. Następnym kryterium jest wytrzymałość produktów oraz możliwe ich obciążenie. Ten czynnik ma duży wpływ na zabezpieczenie jakości i stabilność palet – cięższe kartony ładowane są przed lżejszymi. Palety znajdują się na podnośnikach, dzięki którym następuje opuszczenie palety po każdym załadowaniu aż do momentu całościowej realizacji określonego wzoru. Zapakowane palety transportowane są na spiralach do poziomu wysyłki. W celu zachowania większej stabilności przechodzą automatycznie przez zintegrowane owijarki, skąd transportowane są na przenośnikach paletowych do 2 sekcji buforowych w strefie wysyłkowej. Następnie wózki ładują palety na ciężarówki.
- Inteligentna koncepcja zautomatyzowanych procesów w branży spożywczej - podsumowuje Schenk. - Począwszy od wpływu towaru, przez magazynowanie i komisjonowanie, aż po optymalną paletyzację pod względem objętości do poszczególnych filii, SCP jest wydajnym kompleksowym systemem dla dynamicznej intralogistyki.