Nowa seria pojemników QX SSI SCHAEFER spełnia wysokie wymogi koncernu Volkswagen. Nowe pojemniki mogą być stosowane w systemach automatycznych oraz chronią artykuły przed zanieczyszczeniami i czynnikami mechanicznymi, jak np. w przypadku delikatnych części silników.
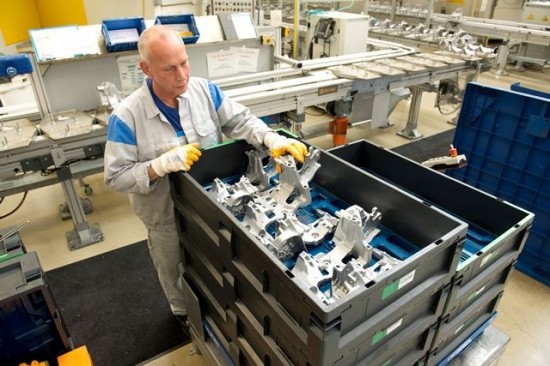
Nowoczesna produkcja przemysłowa charakteryzuje się ciągle rosnącymi wymogami jakościowymi produktów (szczególnie w branży motoryzacyjnej). Głównymi aspektami są czystość, staranne wykonanie oraz prosty proces produkcji. Koncern Volkswagen jako największy producent samochodów w Europie oraz jeden z czołowych na całym świecie ma wysokie wymagania przede wszystkim odnośnie części składowych silników dla wszystkich marek Volkswagen AG, ponieważ to one odpowiadają za jakość pojazdów. Jeśli istnieją jakieś słabe punkty procesów produkcyjnych lub logistyki, odbija się to na jakości produktu.
Koncern Volkswagen ma swoje siedziby w 18 krajach Europy oraz 94 zakłady produkcyjne w 8 krajach w Ameryce, Azji i Afryce. Koncern zatrudnia ok pół miliona pracowników i produkuje dziennie ok 34 500 pojazdów na całym świecie, które później sprzedaje w 153 krajach. Siedziba Volkswagena, będąca jednym z największych na świecie zakładów produkujących silniki, znajduje się w Salzgitter/Niemcy. Zakład zatrudnia około 6 000 pracowników i produkuje silniki na powierzchni ponad 2 800 000 m2 dla całego koncernu Volkswagen. Dziennie produkuje się tu ok. 7 000 silników o zapłonie iskrowym oraz samoczynnym w 370 wariantach. Poza tym zakład produkuje także silniki do łodzi, silniki przemysłowe i elementy dla własnej produkcji oraz klientów zewnętrznych, a także agregaty.
Dla zakładu bardzo istotna jest czystość części, ponieważ ma ona wpływ na jakość silników, a wymagania odnośnie jakości w ostatnich latach znacznie wzrosły. Dodatkowymi ważnymi aspektami są: możliwość automatyzacji oraz szybkie i efektywne procesy. Z tych względów VW podjął decyzję o wprowadzeniu do swojego zakładu pojemników nowej generacji SSI SCHAEFER: najnowszą serię pojemników QX. Obecnie w Salzgitter transportowane i przechowywane są delikatne elementy silników w 30 000 rewolucyjnych pojemnikach, które chronią jednocześnie znajdujące się w nich elementy przed zanieczyszczeniami oraz czynnikami mechanicznymi. Wprowadzenie nowych pojemników odbyło się jednak w sposób niezwykły.
Dotychczas mało dostawców oferowało pojemniki o specjalnych wymiarach 600 x 500mm i 1000 x 600mm. Dostępne na rynku pojemniki wykazywały w obliczu ciągle rosnących wymogów odnośnie czystości oraz automatyzacji coraz więcej wad. Stabilność formy, ochrona elementów, łatwe czyszczenie oraz dopasowanie do magazynowanych lub transportowanych artykułów okazały się w obecnych czasach niewystarczające - gdy palety przemysłowe wykorzystywane są także w procesach automatycznych, potrzebne są dodatkowe adaptery palet, jak w przypadku VW. Dotychczasowe pojemniki nie spełniały wszystkich wymogów produkcji motoryzacyjnej – przede wszystkim, gdy chodziło o nowe projekty, jak np. wały korbowe, które do tej pory były pakowane do otwartych stalowych półek i przykrywane dodatkowo plandeką w celach ochronnych. Do wysyłki musiały być zatem po raz drugi manualnie przepakowane do pojemników (drobiazg, który musiał zostać, także pod kątem czystości, zoptymalizowany). Kiedy Volkswagen opisał ten problem SSI SCHAEFER, nastąpiła natychmiastowa specjalistyczna reakcja.
Zanim jeszcze wpłynęło zlecenie lub nawet zgoda na projekt firma SSI SCHAEFER rozpoczęła razem z przedstawicielami Volkswagen projektowanie nowej serii pojemników dla branży motoryzacyjnej, która powinna sprostać wysokim wymogom producentów samochodowych.
- Największym wyzwaniem było uwzględnienie wszystkich wymagań Volkswagena w jednym pojemniku. Nasze kompetencje w obszarze pojemników oparte są jednak na wieloletnim doświadczeniu. Od razu wiedzieliśmy, że jest to możliwe, dlatego zaczęliśmy projektować nową serię QX bez konkretnego zlecenia. Przede wszystkim wiedzieliśmy, że istnieje na nie zapotrzebowanie - wyjaśnia Axel Breitkreutz, Produktmanager SSI SCHAEFER. Gotowość na inwestycję specjalistów intralogistycznych SSI SCHAEFER doprowadziła do prawdziwej rewolucji w gospodarce pojemnikowej.
- Czystość, możliwość wykorzystania w systemach automatycznych, stabilność, optymalne wykorzystanie pojemności, możliwość łatwego czyszczenia oraz dopasowanie do artykułów – pojemnik QX zdał wszystkie testy i przekonał nas do siebie - wyjaśnia Torsten Fellenberg, Logistyk w Volkswagen. Jak tylko pierwsze seryjne pojemniki zostały wyprodukowane, natychmiast wpłynęło zlecenie na ponad 30 000 pojemników.
Taki pojemnik nie powstaje jednak przez jedną noc - cały rok pracy w pocie czoła nad nowym pojemnikiem transportowym. Aby osiągnąć zamierzone cechy, firma SSI SCHAEFER opracowała nowe sposoby i to z sukcesem, ponieważ QX łączy ze sobą wszystkie zalety projektowanych w ostatnich latach pojemników. Nowy pojemnik plastikowy o wymiarach 1 000 x 600mm oraz 600 x 500mm jest w pełni kompatybilny z wymiarami palet przemysłowych 1 200 x 1 000mm. Dzięki temu VW może prawie we wszystkich przypadkach zrezygnować z adapterów palet. QX przeznaczony jest w szczególności do transportu nowych elementów silników: m.in. wałów korbowych czy modułów zapłonowych.
Aby sprostać wyzwaniom nowoczesnej produkcji przemysłowej, inżynierowie SSI SCHAEFER pożegnali się z tradycyjnym stylem pojemników z bogatym użebrowaniem. Zamiast tego pojemnik transportowy QX, który przeznaczony jest do stosowania blistrów głęboko tłoczonych, ma gładkie ścianki wewnętrzne, co znacznie ułatwia proces czyszczenia. Dodatkowo można wyposażyć ścianki boczne pojemnika w system zatrzaskowy, który służy do mocowania folii tłoczonych lub innych wkładek.
Dzięki specjalnej krawędzi odprowadzającej, do pojemnika nie dostaje się ani woda rozbryzgiwana ani ciała obce (o > 1 mm). Przestrzeń pośrednia jest całkowicie zabudowana. Zostało to sprawdzone przez niezależny Instytut, który przyznał pojemnikowi klasę szczelności IP44.
Kolejnym ważnym aspektem dla Volkswagena było to, że pojemnik posiada liczne prowadnice, a proste wykonanie elementów nośnych zwiększa powierzchnię chwytakową. Szczególne znaczenie ma to przy procesach związanych z produkcją i transportem wałów korbowych. Robot ładuje bezpośrednio do pojemników wcześniej wyczyszczone części. Załadowanie odbywa się do trzech znajdujących się obok siebie pojemników wg. skomplikowanego systemu. Na jeden pojemnik przypadają 3 wały karbowe. Po załadowaniu 8 pojemników w stos pojawia się sygnał świetlny po czym pracownik pobiera tak przygotowaną paczkę z wózka, przytwierdza etykietę i zamyka górny pojemnik pokrywą, aby ochronić artykuły przed kurzem i wodą rozbryzgiwaną. Wyprodukowane i zapakowane wg. zasady Kanban wały karbowe magazynowane są tymczasowo w strefie buforowej, a następnie transportowane do linii montażowej.
Kolejnym ważnym aspektem dla Volkswagena było to, że pojemnik posiada liczne prowadnice, a proste wykonanie elementów nośnych zwiększa powierzchnię chwytakową. Szczególne znaczenie ma to przy procesach związanych z produkcją i transportem wałów korbowych. Robot ładuje bezpośrednio do pojemników wcześniej wyczyszczone części. Załadowanie odbywa się do trzech znajdujących się obok siebie pojemników wg. skomplikowanego systemu. Na jeden pojemnik przypadają 3 wały karbowe. Po załadowaniu 8 pojemników w stos pojawia się sygnał świetlny po czym pracownik pobiera tak przygotowaną paczkę z wózka, przytwierdza etykietę i zamyka górny pojemnik pokrywą, aby ochronić artykuły przed kurzem i wodą rozbryzgiwaną. Wyprodukowane i zapakowane wg. zasady Kanban wały karbowe magazynowane są tymczasowo w strefie buforowej, a następnie transportowane do linii montażowej.
- Proces jest teraz czysty, szybszy i bardziej wydajny, a części odpowiednio chronione bez wykorzystania dodatkowych środków do pakowania - przedstawia Fellenberg. Dzięki większej powierzchni użytkowej przy takich samych rozmiarach, nowe pojemniki oferują większą pojemność, co może obniżyć koszty logistyczne nawet do 30%.
Aby ułatwić manualną obsługę, pojemnik jest zaopatrzony w ergonomiczne uchwyty na krawędzi do sztaplowania. - Dwie kieszenie na etykiety VDA są w tym przypadku konieczne. Poza tym mamy jeszcze wiele miejsca na inne znakowanie, np. wytłaczanie, dodatkowe etykiety lub kody RFID - wyjaśnia Breitkreutz. Firma SSI SCHAEFER wyposażyła dodatkowo pojemniki w kolorowe znaczniki na krawędziach. Dzięki temu pracownicy Volkswagena rozpoznają pojemniki z określonymi częściami, nawet gdy są one ustawione w stos i magazynują je w odpowiednim miejscu. To sprawia, że procesy w Volkswagenie są pewne i bezpieczne.
Specjalna technologia ścianki szczelinowej sprawia, że pojemnik jest odpowiednio stabilny a dwuścienne narożniki i wzmocnienia ścianek bocznych gwarantują ich niezapadanie się. Także nośność pojemnika spełnia wymogi Volkswagena. Dzięki temu, że dno jest wzmocnione i zgrzewane techniką wibracyjną, do pojemnika można załadować ładunek nawet do 70 kg. To sprawia, że także ciężkie elementy mogą być bezpiecznie transportowane. W standardzie pojemnik oferowany jest z gładkimi ściankami wewnętrznymi oraz o obciążeniu ok. 50 kg.
Torsten Fellenberg jest bardzo zadowolony z wyniku: - Seria QX spełniła nasze obecne wymagania. Firma SSI SCHAEFER zawsze reagowała szybko, niezawodnie i przede wszystkim innowacyjnie. Dzięki takiemu rozwiązaniu wiele zyskaliśmy i już cieszymy się na dalszą współpracę.
Więcej o pojemnikach QX na stronie http://www.ssi-schaefer.pl/magazynowanie/skrzynie-i-pojemniki/pojemnik-qx.html