Najczęściej w magazynach do kolizji dochodzi pomiędzy wózkiem widłowym a regałem. Do najbardziej popularnych produktów, które podnoszą stan bezpieczeństwa w magazynie, należą elementy biernej ochrony konstrukcji regałów. Nie bez znaczenia dla bezpieczeństwa jest także używanie nowoczesnych wózków systemowych przeznaczonych do pracy w wąskich magazynowych korytarzach.
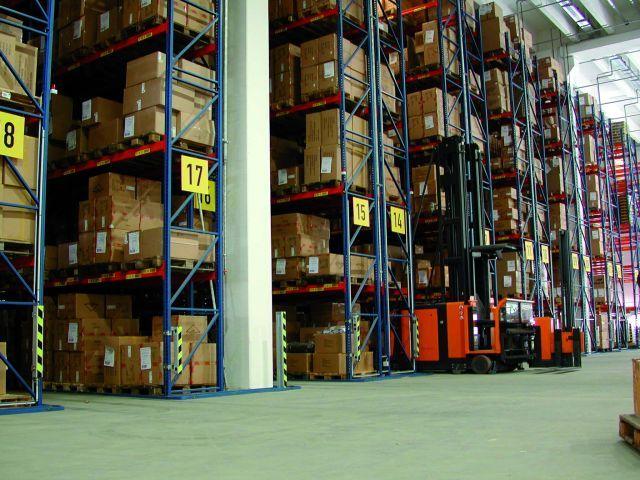
W celu zapewnienia bezpiecznych warunków pracy w magazynie, użytkownik powinien współpracować z projektantem już we wczesnym etapie inwestycji. Szczególną uwagę należy zwrócić na zabezpieczenie miejsc o zwiększonym nasileniu ruchu wózków widłowych, takich jak okolice bram, przejazdów pomiędzy korytarzami międzyregałowymi i oraz na zabezpieczenie miejsc, gdzie poruszają się piesi oraz gdzie wózki widłowe przejeżdżają pod regałami. – Niestety, nagminnie spotykamy się wśród osób projektujących magazyny wysokiego składowania z pomijaniem lub bagatelizowaniem kwestii zapewnienia bezpieczeństwa pracy w wąskich korytarzach. Wynika to często z braku świadomości istniejących zagrożeń związanych z eksploatacją wózków typu VNA, wiedzy na temat sposobów na zapewnienie właściwych warunków bezpieczeństwa pracy czy wręcz braku znajomości odpowiednich norm. Systemowe wózki widłowe poruszające się pomiędzy regałami w wąskich korytarzach magazynów wysokiego składowania stwarzają duże zagrożenie dla osób pieszych potencjalnie mogących się pojawić w tych obszarach pracy wózków. I to z kilku powodów – twierdzi Jarosław Kociszewski, Prezes i Dyrektor Zarządzający ELOKON Logistics.
Nie wystarczą tylko bierne urządzenia ochronne, co w zasadzie sprowadza się do zastosowania głównie kilku rodzajów elementów: ochraniacza słupa, ochraniacza ramy, wypełnienia gniazda w przejeździe regałowym, ogranicznika palet i ewentualnie innych „drobnych” akcesoriów. Na przykład sposób rozłożenia towarów w magazynie i organizacja wykonywanych tam operacji i procesów logistycznych. – Często na dolnych poziomach regałów magazynowych składowane są towary, które pracownik może ręcznie wyjąć i przenieść lub przełożyć na mały wózek, a wykorzystanie w tym przypadku wózka VNA byłoby czasochłonne i nieuzasadnione ekonomicznie. Pracownik taki jest w tym przypadku narażony na kolizję z wózkiem, co stanowi dla niego bardzo duże niebezpieczeństwo – podkreśla Jarosław Kociszewski.
Wózki VNA w ofensywie
Od kilku lat obserwujemy wyraźny wzrost zainteresowania wózkami VNA, jest to pośrednio związane z rosnącym apetytem inwestorów na przestrzeń przeznaczoną na składowanie oraz z rosnącymi wymaganiami w zakresie wydajności pracy (rotowania składowanych ładunków). – Gdy przestrzeń magazynowa jest na wagę złota, np. w strategicznie ulokowanych magazynach na relatywnie drogiej powierzchni czy w przypadku chłodni, przedsiębiorstwa wymagają rozwiązań umożliwiających maksymalne wykorzystanie kubatury. Równocześnie rozwiązania z użyciem regałów i wózków do pracy w wąskich korytarzach nie są tak drogie w zakupie, jak magazyny automatyczne oparte o układnice oraz, co istotne, są możliwe do zastosowania w formie działań modernizujących istniejący magazyn – mówi Łukasz Kobus, Doradca techniczny w firmie Wandalex S.A.
Rynek wózków systemowych do pracy w wąskich korytarzach charakteryzuje się stabilnym wzrostem. Pojazdy VNA znajdują zastosowanie tam, gdzie ceny grunty są szczególnie wysokie i tam, gdzie konieczne jest zapewnienie szczególnych warunków przechowywania produktów – na przykład w chłodniach. – Choć nie można mówić o skokowym wzroście liczby zapytań o tego typu pojazdy, klienci działający w wymienionych wyżej segmentach, dość często wykazują zainteresowanie urządzeniami kategorii VNA – dodaje Tobiasz Jakubczak, Specjalista ds. produktu w STILL Polska. Tę tendencję rynkową potwierdza również Sebastian Borkowski, Area Sales Manager w firmie Manitou Polska sp. z o.o. Jego zdaniem potrzeby rynkowe zmuszają klientów do zwiększania powierzchni magazynowych. Jednym z rozwiązań bez kosztownego, a czasem niemożliwego, rozbudowania hal jest wykorzystanie wózków do pracy w wąskich korytarzach. – Dzięki takiemu rozwiązaniu możemy nawet dwukrotnie zwiększyć ilość miejsc paletowych. Naturalną rzeczą jest więc, że klienci poszukują najkorzystniejszych rozwiązań, jakim zapewne jest wózek do wąskich korytarzy. Tak więc wraz ze zwiększającym się popytem na wózki magazynowe i potrzebą maksymalnego wykorzystania powierzchni magazynowej zainteresowanie sprzętem do wąskich korytarzy będzie wzrastać z każdym rokiem – mówi Sebastian Borkowski.
Przede wszystkim bezpieczeństwo
Podstawowym warunkiem bezpiecznej pracy w wąskich korytarzach magazynów wysokiego składowania jest przestrzeganie zasady, że w obszarach, w których pracują wózki, w tym samym czasie nie powinni znajdować się piesi. W magazynach wysokiego składowania z wąskimi korytarzami pracodawca ma do wyboru systemy ochronne, które można podzielić na trzy grupy:
- zabezpieczenia budowlane (osłony stałe),
- zabezpieczenia techniczne przy wejściach do korytarzy,
- zabezpieczenia techniczne na wózkach.
Oddzielenie obszarów pracy wózków i ludzi może być zrealizowane poprzez zastosowanie różnego rodzaju środków budowlanych, do których możemy zaliczyć: mury, przegrody, ogrodzenia, miejsca przekazywania ładunku. Systemy takie są sztywne i każda zmiana organizacji pracy w magazynie wymaga zmiany systemu. – Zabezpieczenia techniczne przy wejściach do korytarzy, czyli tzw. stacjonarne systemy bezpieczeństwa (bariery świetlne, układy fotokomórek), np. ELObar firmy ELOKON Logistics, są urządzeniami montowanymi przy/na regałach. Muszą one odróżniać pieszych od wózków i uniemożliwiać dostęp pieszym do korytarza, w którym pracuje wózek lub wjazd wózka, jeżeli w tym czasie znajdują się tam piesi. Zabezpieczenia takie, gdy w jednym z korytarzy znajdą się jednocześnie piesi i wózek, muszą wywoływać alarm, dając jednocześnie sygnał optyczny i akustyczny – mówi Jarosław Kociszewski.
Zabezpieczenia techniczne na wózkach, czyli tzw. mobilne systemy bezpieczeństwa, są rozwiązaniami najbardziej zaawansowanymi, niezwykle skutecznymi i elastycznymi w zastosowaniu, np. ELOprotect firmy ELOKON Logistics – system, który montuje się na wózkach, czyli na tym, co bezpośrednio zagraża pieszym. – Działają one w pełni samodzielnie, kontrolując obszar poruszania się wózka w wystarczającej odległości (pola ochronne i ostrzegawcze przed i za wózkiem), a w momencie wykrycia człowieka lub przeszkody nie tylko dają operatorowi wózka sygnał alarmowy (optyczny i akustyczny), ale automatycznie spowalniają i zatrzymują wózek w bezpiecznej odległości przed pieszym lub przeszkodą. Metoda ta jako jedyny środek zabezpieczający oddziałuje na układ sterowania i hamowania wózka, umożliwiając jednocześnie efektywne zapobieganie kolizjom i wypadkom w wąskich korytarzach – wyjaśnia Jarosław Kociszewski.
Pomimo, że praca wózka będzie zabezpieczona przez jeden z wyżej podanych systemów, należy pamiętać, że zgodnie z obowiązującymi przepisami każdy korytarz musi posiadać odpowiednie oznakowanie, wyraźnie wskazujące, że przebywanie w jednym czasie wózków i pieszych w jednym korytarzu jest niedozwolone.
Wybór jest spory
Najpopularniejszym rozwiązaniem firmy STILL w segmencie VNA jest wózek MX-X. Jego wyróżnikiem jest modułowa konstrukcja, dająca niezwykłą elastyczność i pozwalająca dostosować pojazd do specyficznych warunków magazynu. Dzięki kompaktowym wymiarom, MX-X można stosować w znacznie węższych niż standardowe korytarzach roboczych. Maksymalna wysokość podnoszenia na poziomie nawet 15 300 mm z udźwigiem 1 500 kg, pozwala na skuteczną pracę w magazynach wysokiego składowania. STILL MX-X cechuje się również niskimi kosztami eksploatacji i serwisowania. Jego napęd zużywa do 40 proc. mniej energii niż silniki szczotkowe, a instalowany w standardzie system Blue-Q pozwala na dodatkowe, kilkunastoprocentowe oszczędności.
W Polsce zgodnie z Kodeksem Pracy oraz z rozporządzeniami MGPiPS odnośnie bezpieczeństwa i higieny pracy przy użytkowaniu maszyn, pracodawca zobowiązany jest do zapewnienia bezpiecznych warunków pracy, wykorzystując do tego celu wszystkie możliwe środki, a w szczególności osiągniecia nauki i techniki.
– Wózek MX-X wykorzystuje system STILL OPTISPEED, gwarantujący optymalne dopasowanie szybkości jazdy wózka do wagi transportowanego ładunku. Umożliwia również optymalizację trasy dojazdu do celu oraz zatrzymanie pojazdu w idealnej odległości od regału dzięki systemowi lokalizacji pojazdu w oparciu o dane WMS oraz kody kreskowe umieszczane na regałach, obok których przejeżdża MX-X. Z kolei rozwiązanie STILL OPTISAFE, pozwala zaprogramować wykonanie konkretnych zadań, takich jak na przykład: redukcja prędkości, zatrzymanie pojazdu czy opuszczenie masztu w miejscach magazynu wymagających szczególnej ostrożności – mówi Tobiasz Jakubczak.
Z kolei spółka Manitou oferuje wózek EMA II. Jest to przegubowy czołowy wózek widłowy. Minimalny korytarz dla takiej maszyny to 1700 mm. Posiada napęd elektryczny. W zależności od potrzeb, udźwig urządzenia zaczyna się od 1,3 t, a kończy na 2 t. Maksymalna wysokość podnoszenia to ponad 12 m. – Duża ilość miejsca dla operatora i szeroka gama wyposażenia gwarantują bezpieczeństwo pracy. Ergonomicznie rozmieszczone elementy wpływają znacząco na produktywność, a możliwość bocznej wymiany baterii umożliwia pracę zmianową. Dzięki dużemu prześwitowi i wysokiej jakości zastosowanych kół wózek bez obaw może pełnić funkcję wózka czołowego wykorzystywanego do pracy na zewnątrz – podkreśla Sebastian Borkowski.
Markę Yale na polskim rynku reprezentuje firma EMTOR. W wózku systemowym Yale MTC standardowym fabrycznym wyposażeniem jest wewnętrzny system kontroli i zarządzania funkcjami, który nieustannie czuwa nad bezpieczeństwem pracy. W zależności od wysokości podnoszenia kabiny operatora, system ten automatycznie dobiera takie parametry wózka (np. maksymalną prędkość jazy wózka), aby zapewnić bezpieczeństwo operatora i ładunku, pozwalając jednocześnie na możliwie największą wydajność pracy. – Sporym zainteresowaniem cieszą się również systemy bezpieczeństwa pracy wózkiem systemowym oparte na laserowym skanowaniu przestrzeni przed i za wózkiem. System ten pozwala na wychwycenie przeszkody w korytarzu roboczym wózka (człowiek, przedmiot) i automatyczne wyhamowanie czy zatrzymanie wózka. Dostępne w naszej gamie wyposażenia wózka VNA są również systemy identyfikacji korytarza roboczego oparte na technologii RFID, dzięki której w danym korytarzu możemy zdefiniować zagrożenia dla wózka (np. niski przejazd pod konstrukcją magazynu) i wyeliminować możliwość niebezpiecznego zdarzenia – mówi Tomasz Łukaszek, Manager produktu w firmie EMTOR sp. z o.o.
Podstawowym warunkiem bezpiecznej pracy w wąskich korytarzach magazynów wysokiego składowania jest przestrzeganie zasady, że w obszarach, w których pracują wózki, w tym samym czasie nie powinni znajdować się piesi. Należy pamiętać, że zgodnie z obowiązującymi przepisami każdy korytarz musi posiadać odpowiednie oznakowanie, wyraźnie wskazujące, że przebywanie w jednym czasie wózków i pieszych w jednym korytarzu jest niedozwolone.
Opatentowany system hydrauliczny MTC firmy Yale umożliwia dostęp do wszystkich funkcji hydraulicznych jednocześnie, w połączeniu z lepszym zarządzaniem energią. Wózek posiada 2 niezależne silniki z pompami hydraulicznymi, które w zależności od obciążenia wspomagają się wzajemnie. Pompy są 2-kierunkowe i pozwalają na odzysk energii w trakcie opuszczania kabiny.
Stabilność kabiny wózka Yale MTC gwarantuje specjalna konstrukcja masztu z oktagonalnymi stężeniami sekcji. Dzięki takiemu rozwiązaniu maszt jest bardzo stabilny i nie potrzebuje wzmocnień dodatkowych w postaci skośnych usztywnień przymocowanych do tylnej części ramy wózka. Opatentowany przez Yale maszt typu QUADFORM zapewnia bezpieczeństwo pracy wózkiem i stabilność ładunku przy wysokościach podnoszenia przekraczających nawet 16 m.
Aktualności, wydarzenia, komentarze, branżowe czasopisma - bądź na bieżąco. Zapisz się do newslettera portalu logistyczy.com - KLIKNIJSpółka Wandalex w zakresie wózków do pracy w wąskich korytarzach Crown oferuje wózki TSP 6000, TSP 6500 i TSP 7000 o udźwigu 1000–1500 kg i maksymalnej wysokości podnoszenia od 11,7 do 17,2 m. – Wózki wyposażone są w pojedynczy maszt MonoLift, który pozwala na wyjątkową stabilność na wysokościach. Taki typ konstrukcji stosuje się w żurawiach wysięgnikowych o kilkakrotnie wyższej wysokości podnoszenia. Druga praktyczna funkcjonalność to obrotowy w zakresie 110° fotel operatora MoveControl, który pozwala na indywidualne ustawienia zapewniające optymalne pole widzenia i wygodę. Daje to operatorowi poczucie pewności przy pracy na wysokościach. Wszystkie elementy sterowania są wbudowane w podłokietniki fotela i umożliwiają kompletację na każdym poziomie składowania – twierdzi Łukasz Kobus.
Jego zdaniem, sterowane komputerowo hamulce automatycznie dostosowują się do wysokości podnoszenia i innych istotnych zmiennych, aby zapewnić lepszą kontrolę i zwiększyć bezpieczeństwo pracy. Poza tym stosowany jest system wykrywania obecności w korytarzu roboczym, co zabezpiecza przed przypadkowym potrąceniem „nieproszonego gościa” w korytarzu, w którym znajduje się pracujący wózek VNA. – Standardowe wyposażenie wózka stanowią czujniki położenia stóp i dłoni operatora, które dbają o to, aby jazda wózkiem odbywała się tylko i wyłącznie w sytuacji prawidłowej pozycji ciała operatora, a najpopularniejsze aktualnie indukcyjne prowadzenie wózka w korytarzu minimalizuje ewentualne błędy w prowadzeniu wózka i eliminuje potrzebę kontroli jazdy w kierunku przód-tył – dodaje Łukasz Kobus.
Sławomir Erkiert