Podstawowym narzędziem pracy każdego agenta zmiany jest warsztat (ang. Workshop), oczywiście o jego sukcesie decydować będzie szereg innych czynników, jak zaplanowanie i prowadzenie administracji i promocji Lean Management, komunikacja z pozostałymi pracownikami czy znajomość narzędzi. Ostatecznie to jednak poprzez prowadzenie prac z grupą, mających na celu poprawę procesów, realnie dokonuje się zmiana.
Dzięki umiejętności organizowania, prowadzenia, a także implementacji rozwiązań wypracowanych przez zespół podczas warsztatu, buduje się kulturę ciągłego doskonalenia i pozyskuje kolejnych zwolenników filozofii Kaizen. Pracownicy wszystkich szczebli, widząc skuteczność wprowadzonych zmian, a także korzyści, jakie sami dzięki temu uzyskują, coraz bardziej angażują się w Lean Management i chcą być częścią tej kultury. Jak zatem przeprowadzić efektywny warsztat? W pierwszej fazie należy całe wydarzenie zaplanować z odpowiednim wyprzedzeniem i upewnić się, że zakres warsztatu jest spójny z wizją rozwoju zakładu. Jeżeli organizacja ma harmonogram tego typu wydarzeń, to sprawa jest prostsza, ale nawet wtedy warto sprawdzić, czy bieżąca sytuacja jest sprzyjająca. Zakład może mieć przejściowe problemy, wówczas warto zastanowić się, czy nie należy terminu przesunąć. Takie podejście zapewni prowadzącemu większe poparcie zespołu, a w dalszej kolejności niezbędne zasoby (przede wszystkim ludzkie). Kompletowanie interdyscyplinarnego zespołu ma kluczowe znaczenie dla rezultatu wydarzenia. Zespół powinni tworzyć, w miarę możliwości, przedstawiciele wszystkich działów operacyjnych (minimum jedna osoba z działu) przy wsparciu jednego lub dwóch uczestników z pozostałych działów (kadry, finanse, BHP), tzw. świeże oko. Takie podejście pozwala maksymalizować zjawisko synergii i uwzględniać potrzeby wszystkich zainteresowanych. Nie należy zapominać również o takich szczegółach, jak rezerwacja sali, artykuły biurowe i pozostały sprzęt, który będzie wykorzystywany podczas warsztatu (stopery, metrówki itp.) – szukanie sali wraz z uczestnikami albo organizowanie ołówków w dniu warsztatu nie jest profesjonalne, traci się przez to czas i motywację uczestników. Jeżeli faza planowania i przygotowania przebiegła pomyślnie, to czas na poprowadzenie warsztatu. Agenda może być różna w zależności od tematyki warsztatu, jest nieorganiczna ilość możliwości, na potrzebę artkułu zostanie przedstawione uniwersalne narzędzie, które często określa się po prostu warsztatami Kaizen. Wydarzenie to można by zdefiniować następująco: poszukiwanie przez wszystkich zaangażowanych łatwych i szybkich (najlepiej do wdrożenia w trakcie warsztatu) rozwiązań w miejscu pracy, poprzez eliminację marnotrawstw (7 strat) i optymalizację przepływu. Jest to ponowne definiowanie organizacji pracy w miejscu, gdzie dodawana jest wartość. Odwołując się do powyższej definicji, proponowana agenda może wyglądać następująco:
- Wyznaczenie czasu taktu,
- Wyszukiwanie i eliminacja strat (ang. Waste walk),
- Balansowanie linii,
- Ustalenie optymalnej liczby operatorów,
- Zdefiniowanie celi godzinowych,
- Budowanie/rozwój pracy standardowej,
- Implementacja przepływu jednej sztuki,
- Ustawienie linii (ang. Layout),
- Frontowe zasilania (praca z złotej strefie),
- Ergonomia stanowiska pracy.
Czas taktu jest bazą, na której powinny być skupione wszystkie pozostałe działania, niestety nadal często mylony jest z czasem cyklu, który jest jego pochodną. Najprościej określić go jako czas, w którym klient kupuje od dostawcy jedną sztukę. Aby wyznaczyć czas taktu, potrzebujemy dwie dane: zamówienie klienta (najczęściej przeliczone na jeden roboczodzień) i dostępny czas netto producenta.
Czas Taktu= (Dostępny Czas Netto)/(Zamówienie Klienta)
Czas taktu jest często porównywany do uderzeń bębnów (ang. drum beats) na galerach, które narzucały tempo pracy wioślarzy z tym, że w tym wypadku odnosi się to do linii produkcyjnych (Rys. 1). Czas Taktu należy obliczać dla jednej rodziny produktów. Często w ramach danego gniazda produkcyjnego czy projektu produkowanych jest więcej niż jedna rodzina produktów, wówczas należy się zastanowić, ile czasu jest przeznaczone na produkowanie referencji, którą grupa zajmować się będzie w trakcie pracy.
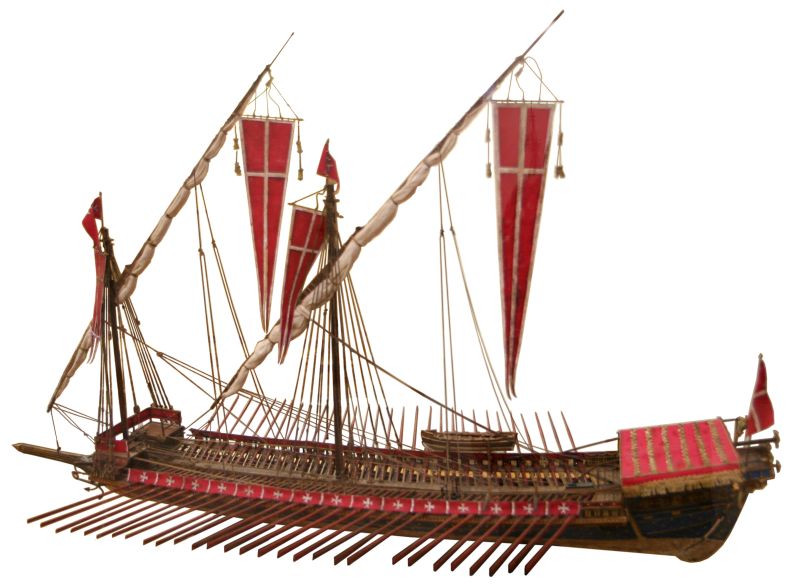
Rys. 1.
Eliminacja strat to podstawowe założenie każdego systemu produkcyjnego opartego na filozofii Kaizen. Najczęściej definiuje się siedem podstawowych: nadprodukcja, zapasy, niepotrzebne ruchy, transport, słaba jakość, oczekiwanie i niepotrzebne operacje (Rys. 2). Czasami dodaje się jeszcze ósmą, zdefiniowaną jako niewykorzystanie potencjału ludzkiego (głównie wiedzy pracowników bezpośrednio produkcyjnych). Najgorszą ze strat jest nadprodukcja, w odróżnieniu od pozostałych strat pochodzi ona z decyzji i ma na celu budowanie pozornego zapasu bezpieczeństwa na wypadek awarii, braku personelu czy problemów jakościowych (powodów jest znacznie więcej). Kolejnym efektem nadprodukcji jest zapotrzebowanie na dodatkową powierzchnię, a także sprzęt do transportu (wózki widłowe, opakowania, regały itp.). W rezultacie problemy są ukrywane, a nie eliminowane, uniemożliwiając w ten sposób redukcję kosztów, a często nawet je dodatkowo podnoszą. Typowym narzędziem służącym eliminacji strat jest tzw. Waste Walk, podczas którego przeszkolony (z zakresu 7 strat) personel przygląda się organizacji linii definiując i eliminując straty. Należy pamiętać, że część strat nie jest możliwa do usunięcia natychmiast (przykładem może być kontrola jakościowa), jednak przy odpowiednim zaplanowaniu działań większość daje się wyeliminować lub znacząco ograniczyć.
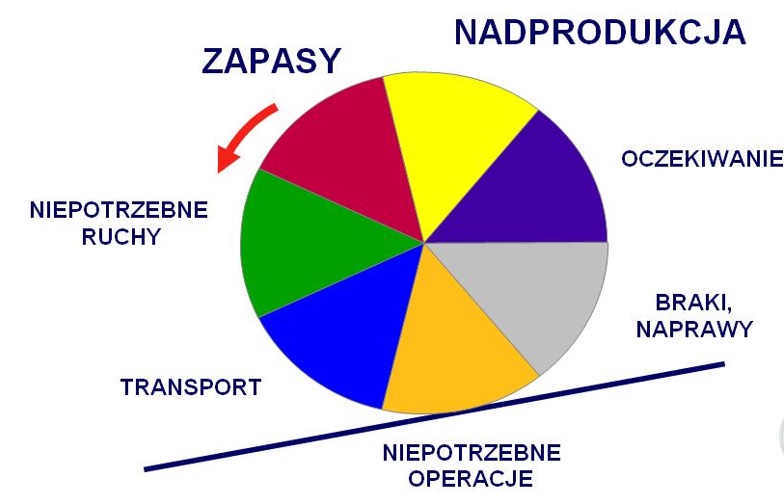
Rys. 2.
Balansowanie linii polega na równomiernym rozłożeniu pracy pomiędzy operatorów tak, aby optymalizować przepływ i eliminować wąskie gardła. Podstawowym wyznacznikiem jest omawiany wcześniej czas taktu. Dobry balans to taki, w którym stosunek czasu cyklu do czasu taktu wacha się w graniach od 90 do 95 proc. (w zależności od rodzaju procesu i poziomu strat). Najczęściej w trakcie warsztatu wykorzystuje się graficzną reprezentację balansu linii, którą jest diagram czasu cyklu (Rys. 3). Czas cyklu to czas potrzebny do wykonania wszystkich czynności przez operatora (zarówno dodających wartość, jak i strat), zanim je powtórzy. Diagram czasu cyklu pokazuje wahania pomiędzy każdym z cykli (zmienność wynikającą ze strat) oraz brak wypoziomowania między operatorami.
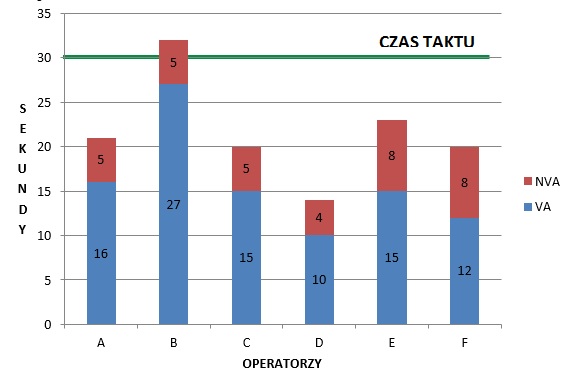
Rys. 3.
Kolejny etap warsztatu jest wynikiem wniosków i obliczeń wyciągniętych z poprzedniego kroku (balansowania linii). Ustalenie liczby operatorów dokonuje się poprzez podzielenie całkowitej zawartości pracy na linii (ang. Work Content) przez czas taktu. Uzyskany wynik daje wyznacznik, jaka powinna być teoretyczna liczba operatorów na linii, a porównując ją z obecną sytuacją, czy praca jest wykonywana w sposób efektywny. Czasami wystarczy tylko lepiej rozłożyć poszczególne elementy pracy pomiędzy operatorów tak, by cykl pracy każdego z nich był zbliżony. Innym razem uwaga musi być skupiona na eliminacji strat lub optymalizacji procesu (np. skrócenie czasu maszynowego). Jeżeli po optymalizacji liczba operatorów na linii nie jest liczbą całkowitą (lub bliską jej), to można też zastanowić się nad pracą w dwóch lub nawet trzech różnych ustawieniach (tzw. balans N, N+1, N-1) w trakcie trwania zmiany i przesuwaniu operatorów pomiędzy gniazdami produkcyjnymi.
Zdefiniowanie celi godzinowych najlepiej wprowadzić, używając tablicy produkcji części (tablica pracy godzinowej). Bardzo efektywne narzędzie z obszaru zarządzania wizualnego ułatwiające pracę, w szczególności osobą bezpośrednio odpowiedzialnym za produkcję na danym obszarze (Rys. 4).
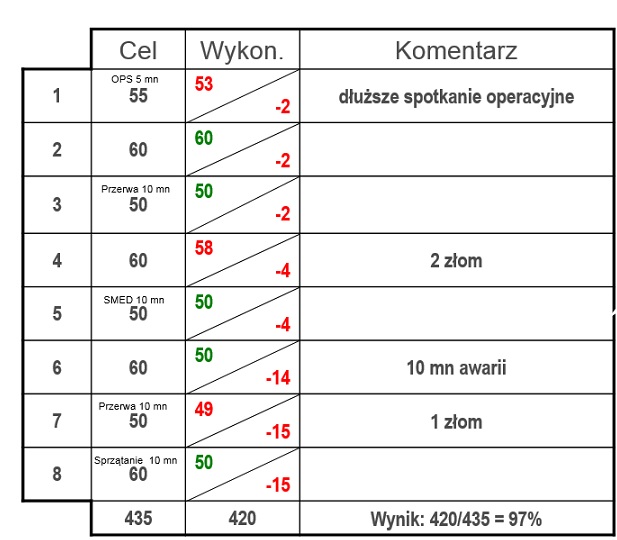
Rys. 4.
Praca Standardowa, która zgodnie z definicją jest najlepszym i najkrótszym sposobem wykonywania pracy na danym stanowisku, wypracowanym przez wszystkie zmiany, powinna być aktualizowana po każdym warsztacie. Często jednak po wprowadzeniu tymczasowego standardu i wstępnym szkoleniu pracowników czynność ta jest pomijana. Jest to szczególnie widoczne w zakładach, które nie mają dobrze opracowanego systemu audytowania pracy standardowej (jednego z czterech podstawowych elementów obok budowania, szkolenia i ciągłej poprawy). Nie mając jasno określonego standardu, nie ma możliwości jego sprawnego egzekwowania, a idąc dalej tym tropem – nie ma też szansy na jego trwały i skuteczny rozwój. Dlatego bardzo ważne jest, aby jak najszybciej wprowadzać wszelkie aktualizacje, które są wynikiem rozwiązań i pomysłów zaproponowanych podczas sesji Kaizen.
Optymalizacja przepływu (ang. flow) i dążenie do przepływu jednej sztuki lub jednej partii zawsze powinno być w centrum uwagi podczas warsztatu Kaizen. W zasadzie jest to kolejna czynność, na której należy się skupić po wyznaczeniu czasu taktu. Im mniejsze serie produkcyjne, tym większa elastyczność i mniejsza zajmowana powierzchnia, jest to następstwem obniżenia zapasów zarówno półproduktów, surowców, jak i wyrobu gotowego. Zapasy, będące efektem nadprodukcji, zawsze ukrywają problemy. Mając dużą ilość półproduktów na linii/celi produkcyjnej, nie jesteśmy w stanie ocenić wizualnie, czy balans jest optymalny. Staje się to natychmiast widoczne po wprowadzeniu przepływu jednej sztuki (łatwo zaobserwować, który operator jest tzw. „wąskim gardłem”, a który musi na niego czekać). Przepływ jednej sztuki pozwala też reagować natychmiastowo na pojawiające się problemy jakościowe. Powoduje to znaczne obniżenie napraw czy złomu. Można by wymieniać kolejne zalety ciągłego przepływu, największą z nich jest jednak to, że straty stają się natychmiast widoczne, dzięki czemu można odpowiednio szybko reagować i redukować koszty.
W filozofii Kaizen preferowane są dwa sposoby budowania gniazd produkcyjnych: tzw. U – celka (gniazdo w kształcie litery U) (Rys. 5) lub linia prosta (Rys. 6). Oba rozwiązania mają swoje wady i zalety. Podczas warsztatu dobrze jest zastanowić się, czy badane gniazdo pracuje w jednym z tych dwóch układów. U – celka sprawdza się przede wszystkim w sytuacjach, gdy operatorzy muszą wielokrotnie przenosić detal pomiędzy maszynami (ang. multi handling). Zalety tego rozwiązania to między innymi: wejście (surowiec/komponent) i wyjście (wyrób gotowy) po tej samej stronie, duża elastyczność w balansowaniu linii. Wadą tego sposobu pracy jest konieczność zasilania linii z obu stron jak i ręczne przenoszenie części. Drugi sposób ustawienia maszyn w linię prostą jest preferowany, gdy mamy do czynienia z pracą głównie manualną. Jego zaletą jest: łatwość w synchronizacji z innymi obszarami produkcyjnymi (ang. Layout), zasilanie w materiał z jednej strony. Słabością tego rozwiązania jest mniejsza elastyczność w przypadku balansowania linii. Należy zastanowić się, które rozwiązanie będzie pasować lepiej dla danego projektu/gniazda, a także czy pasuje ono do całościowej wizji zakładu (czasem może się okazać, że zapoczątkuje to dyskusję o reorganizacji całego obszaru produkcji czy nawet całej fabryki).
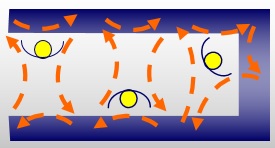
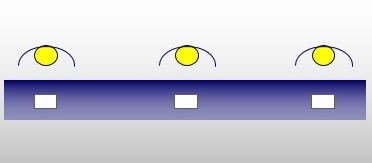
Rys. 5. Rys. 6.
Dwa ostatnie punkty, czyli zasilanie stanowiska i jego ergonomia, są ze sobą mocno powiązane i skupiają się na eliminacji zbędnych i często niebezpiecznych ruchów (schylanie, obracania, dźwiganie itp.). Warto zaangażować tutaj pracowników odpowiedzialnych za BHP, którzy mogą wspomóc – często mają gotowe narzędzia do sprawdzenia ergonomii stanowiska. Często spotyka się pojęcie pracy w tzw. „Złotej Strefie”, oznaczające mniej więcej tyle, że większość (w zasadzie wszystkie) komponentów znajduje się w zasięgu rąk operatora i są łatwo dostępne (Rys. 7).
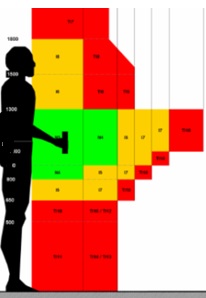
Rys. 7.
Poza samym zakresem/agendą warsztatu Kaizen niezbędne będzie też wcześniejsze przygotowanie paru narzędzi czy informacji (numeracja pokrywa się z zagadnieniami omawianymi powyżej):
- Zamówienie klienta (przeliczone na jeden dzień),
- Formularz do obserwacji/zapisywania strat,
- Formularz pomiarów czasu i stoper,
- Kalkulator,
- Informacja o standardowych przerwach,
- Aktualna dokumentacja Pracy Standardowej,
- Ustalenie, jaki jest dzisiejszy poziom zapasów na linii i jak został określony,
- Wydrukowany Layout i nożyczki,
- Jakich rozwiązań używamy (systemy rurowe, podajniki itp.),
- Formularz oceny ergonomii na stanowisku pracy.
**
Michał Prasał
Senior Continuous Improvement Manager
Cooper Standard Europe