Systemy podwieszane w logistyce magazynowej to rozwiązanie dość często kojarzone z branżą odzieżową. Faktem jest, że przemysł tekstylny chętnie korzysta z takiego rodzaju transportu wewnętrznego, niemniej jednak w również innych branżach systemy podwieszane znajdują z powodzeniem zastosowanie. Nie ulega wątpliwości, że takie instalacje są wymagające projektowo oraz że cechuje je duża elastyczność, bardzo pożądana przez niektóre grupy użytkowników.
Zakres towarów, które można transportować za pomocą instalacji systemów podwieszanych, jest do prawdy szeroki. Wynika to z faktu, iż taki system transportu można wyposażyć w różnego rodzaju zawieszki. Mogą one bowiem występować jako haki, półki czy nawet przenośniki rolkowe.
Choć na pierwszy rzut oka z transportem podwieszanym kojarzy nam się przede wszystkim odzież, w rzeczywistości branże wykorzystujące systemy transportu podwieszanego są dosyć różnorodne: od motoryzacyjnej poczynając, poprzez operatorów logistycznych, branżę odzieżową i tekstylną, a także pralnie przemysłowe, aż po firmy zajmujące się dzierżawą odzieży roboczej. „Ciekawym przykładem jest firma Moss Bross z Wielkiej Brytanii, która prowadzi zarówno sprzedaż, jak i wypożyczanie ubrań na różnego rodzaju przyjęcia czy gale (np. smokingi). W magazynie Moss Bross możliwe jest magazynowanie i obróbka ubrań na wieszakach, które należą do systemu wypożyczalni tej firmy, a także magazynowanie i dystrybucja odzieży pakowanej płasko. Pod jednym dachem połączone zostały dwa różne procesy logistyczne” – mówi Magdalena Choquet, Managing Director w Dematic Poland.
Rozpatrując celowość zastosowania tego rodzaju transportu wewnętrznego, warto pamiętać, iż wielkość firmy nie ma w tym przypadku większego znaczenia. Rozwiązania oparte na systemach transportu podwieszanego stosują firmy nieduże, średnie oraz wielkie korporacje. „W zależności od konkretnych potrzeb, zastosowanie systemu może obejmować całość procesów logistycznych, takich jak przyjęcie towaru, magazynowanie, kompletację zamówień czy sortowanie na poszczególnych odbiorców, albo tylko wybrane, kluczowe dla firmy obszary, np. magazynowanie oraz kompletację zamówień czy też pakowanie towaru w torby foliowe” – dodaje Magdalena Choquet.
Dominujące branże
Niektóre gałęzie przemysłu szczególnie upodobały sobie transport podwieszany jako najkorzystniejsze logistycznie rozwiązanie w procesach magazynowania i dystrybucji. „Najczęściej system transportu podwieszanego jest wykorzystywany przez branże tekstylne. Firmy, takie jak H&M, Spedimex czy Lancerto, posiadają w swoich centrach dystrybucyjnych bardzo duże powierzchnie systemów podwieszanych. Kolejnymi są dystrybutorzy produktów spożywczych takich, jak owoce, warzywa i mięso. Ze względu na oszczędność miejsca i możliwość transportu bez blokowania dróg komunikacyjnych transport podwieszany jest wykorzystywany również przez branżę automotive oraz elektroniki czy telemechaniki” – mówi Andrzej Malec, Menedżer Logistyk w firmie WDX S.A. Nasz rozmówca twierdzi, że tak naprawdę możliwość wykorzystania transportu podwieszanego może mieć miejsce niemalże w każdym magazynie – jest to kwestia wprowadzenia innowacji czy niestandardowego podejścia do tematu transportu wewnętrznego.
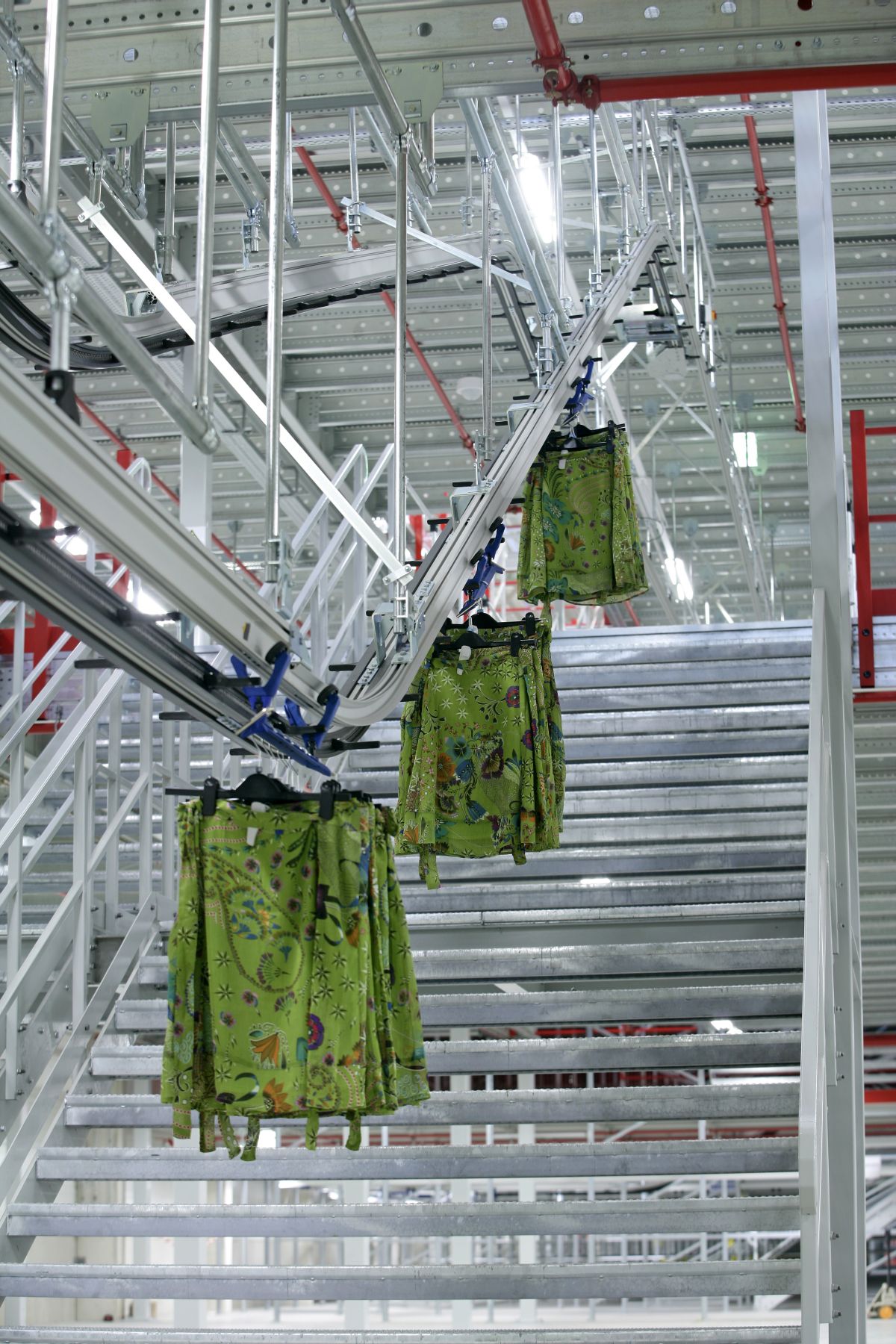
fot. Dematic
O konkurencyjności transportu podwieszanego w logistyce branży motoryzacyjnej przekonuje z kolei Magdalena Choquet z Dematic Poland. „Systemy transportu podwieszanego sprawdzają się także w branży motoryzacyjnej – tam, gdzie ważne jest szybkie dostarczenie podzespołów do montażu na linii. Dotyczy to elementów lekkich, takich jak na przykład tłumiki, okrycia foteli, paneli itp. Systemy sortowania stosowane w systemach podwieszanych umożliwiają dostarczenie podzespołów w 100 proc. sekwencji wymaganej na linii produkcyjnej lub montażowej, dotrzymując bardzo rygorystycznych i krótkich taktów linii obowiązujących na produkcji” – mówi Magdalena Choquet i dodaje, że technologia ta pozwala na szybką realizację krótkich serii w krótkim czasie od wywołania zapotrzebowania. Dodatkowo zapewnia wysoki poziom wykorzystania dostępnej powierzchni na hali produkcyjnej, gdyż nie wymaga stosowania tradycyjnych przenośników.
Kluczowy projekt
Transport podwieszany to z pewnością rozwiązanie na swój sposób unikatowe, w każdym przypadku indywidualnie rozpatrywane przez inwestora i firmę odpowiedzialną za zaprojektowanie systemu tak, aby na etapie eksploatacji działał bez zarzutu i spełniał pokładane w nim założenia. Andrzej Malec z WDX SA radzi przed podjęciem takiej inwestycji wziąć pod uwagę następujące aspekty techniczne:
• Zaplanowanie rozstawienia stanowisk załadunku i odbioru;
• Projekt przestrzenny urządzenia i wykluczenie kolizji;
• Sprawdzenie elementów konstrukcji wsporczej i podwieszanej co do możliwości przeniesienia obciążeń przez konstrukcję dachu słupów i posadzki;
• Rozwiązanie kwestii dróg transportowych;
• Dobór rozwiązania do kwestii wydajnościowych i buforowych;
• Zaprojektowanie zawieszek dedykowanych do produktu oraz sposobu załadunku i wyładunku;
• Określenie, czy ma to być system transportu automatycznego, czy manualnego.
Wybór właściwej technologii z szerokiej gamy systemów podwieszanych wymaga – jak w każdym projekcie automatyzacji – pogłębionej analizy procesów magazynowania i dystrybucji oraz specyfiki towaru. Również Magdalena Choquet z Dematic Poland zwraca szczególną uwagę na kilka krytycznych aspektów.
Pierwsza rzecz to charakterystyka towaru, czyli wymiary, waga, kształt, opakowanie, sposób pakowania (np. pojedyncze sztuki czy opakowania zbiorcze).
Drugi istotny czynnik to wymagana przepustowość systemu – czyli nie tylko i wyłącznie wydajność samego urządzenia sortującego, a wydajność całego systemu (procesu) przygotowania zamówień, przyjęcia towaru i wysyłki. „To na tym etapie tak ważne są analizy danych, obejmujące prześledzenie wolumenów dziennych, tygodniowych, rocznych; istotna jest sezonowość; szczególna uwaga powinna zostać poświęcona tzw. „peaks”, czyli nagłym skokom w zapotrzebowaniu i ten parametr warto prześledzić na przestrzeni przynajmniej dwóch pełnych sezonów. Oczywiście nie zapominamy o planowanych czasach pracy operacyjnej magazynu oraz planowanym wzroście wolumenu przynajmniej w perspektywie 2–3 lat” – mówi Magdalena Choquet.
Kolejny, trzeci, czynnik wskazany przez eksperta – to charakterystyka punktów dostaw towaru. Badana jest liczba destynacji, ich zmienność (to w przypadku odbiorców indywidualnych) oraz spodziewany wzrost ich liczby. „Oczywiście, niezbędne jest określenie zakresu zastosowania systemu podwieszanego: czy ma obejmować wszystkie procesy w centrum dystrybucji od przyjęcia towaru po wysyłkę, czy tylko wybrane aktywności. Jeśli system ma obsługiwać tylko wybrane aktywności, trzeba zaprojektować integrację systemu podwieszanego z procesami, które mają miejsce wcześniej oraz które następują po wydaniu towaru z systemu podwieszanego” – tłumaczy Magdalena Choquet.
Elastyczność konstrukcji
Nasza rozmówczyni wyjaśnia, iż w branży tekstylnej na system transportu podwieszanego składa się lekka, podwieszana do sufitu, konstrukcja aluminiowa, przypominająca złożony układ „torów”, na których przenoszone są pojedyncze wieszaki z ubraniami lub lekkie „wózeczki” (trolleys), na których umieszczona jest odzież na wieszakach. Konstrukcja posiada zwrotnice pozwalające na swobodne kierowanie towaru w wymagany obszar magazynu. Możliwe jest łączenie niezmechanizowanych elementów systemu z elementami zautomatyzowanymi, a także różnych opcji rozwiązań w obrębie jednego zintegrowanego systemu. Przepływ towaru kontrolowany jest poprzez system kontrolny, czyli oprogramowanie współpracujące z systemami WMS oraz układy skanerów. „Systemy transportu podwieszanego mają zastosowanie na każdym etapie przepływu strumienia towarów w centrum dystrybucyjnym. Znaczna różnorodność dostępnych systemów powoduje, że można wybierać spośród technologii, które oferują różne poziomy mechanizacji: począwszy od całkowicie ręcznych sposobów pracy, do wysoce zautomatyzowanych” – mówi Magdalena Choquet z Dematic Poland. „Inna kwestia to wybór nośników. Transport podwieszany odzieży wiszącej może odbywać się na specjalnych „wózeczkach” o długości ok. 500 mm i nośności do 35 kg. Albo decydujemy się na transportowanie pojedynczych wieszaków, mając jednocześnie pewność, że system poradzi sobie z wieloma rodzajami uchwytów przy wieszakach stosowanych przez producentów. Oba sposoby pracy pozwalają na śledzenie zarówno pojedynczych sztuk odzieży, jak i całych partii towaru” – dodaje.
Towar może być dostarczany do magazynu w formie wiszącej lub zapakowany na płasko w kartony. W tym pierwszym przypadku operatorzy umieszczają towar bezpośrednio na specjalnych wysięgnikach teleskopowych, które transportują wyładowany towar do odpowiedniego miejsca w magazynie. Jeśli natomiast towar przyjeżdża w kartonach, rozładunek odbywa się w tradycyjny sposób, kierowany jest on do strefy przyjęć, gdzie operatorzy pracujący przy odpowiednich stołach roboczych przekładają każdą sztukę odzieży na wieszak. W tym przypadku możliwe jest jednoczesne dokonywanie wizualnej kontroli jakościowej produktu.
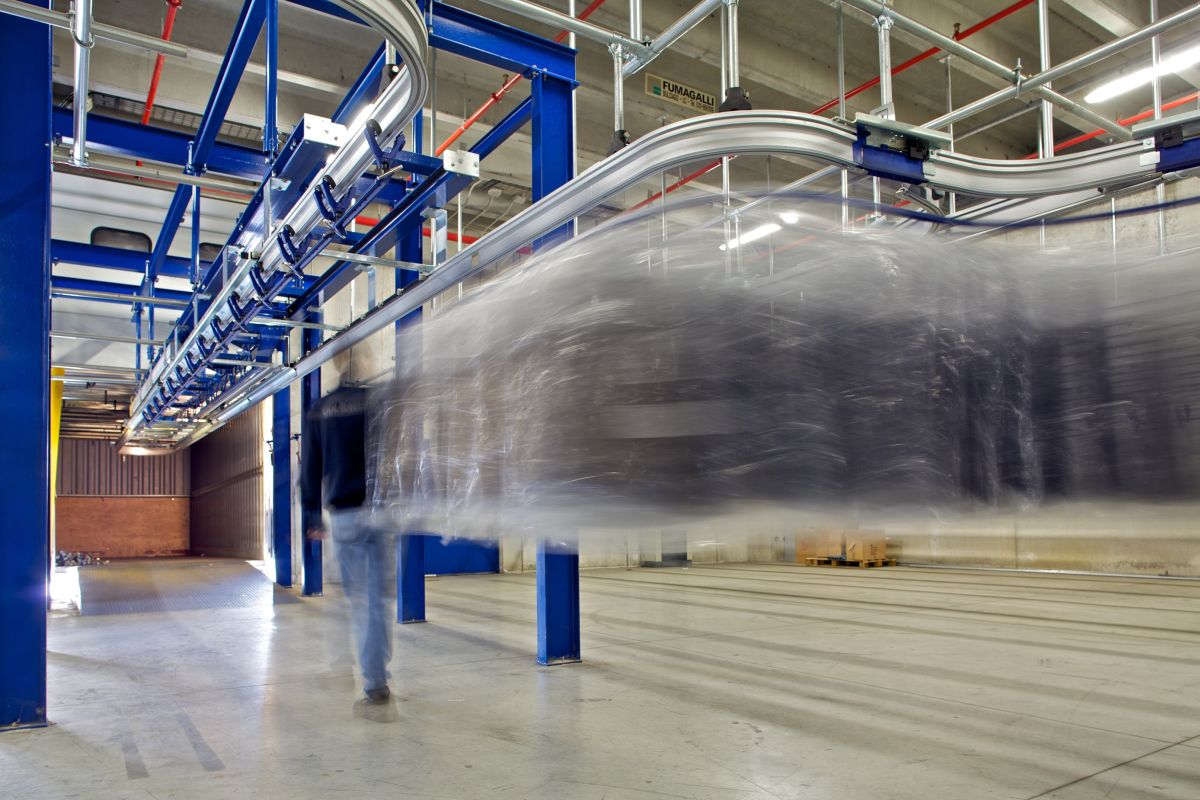
Jak podaje Andrzej Malec z WDX SA, zazwyczaj elementy systemu podwieszanego mają budowę modułową – oznacza to, że jest możliwość zmiany konfiguracji linii transportowych. „Zmianę taką należy jednak każdorazowo skonsultować z producentem – dostawcą. Konstrukcja systemu podwieszanego bardzo często połączona jest z elementami konstrukcji budynku. W takim przypadku konieczne jest sprawdzenie warunków wytrzymałościowych zarówno z dostawcą systemu, jak i projektantem hali magazynowej” – sugeruje nasz rozmówca.
Podobnie projekty, konstruowane przez firmę Dematic, budowane są na bazie sprawdzonych, modułowych i skalowalnych podsystemów. Podsystemy w tym kontekście to nie to samo, co produkty – podsystem obejmuje grupę zintegrowanych produktów (technologii) zaprojektowanych w celu spełniania konkretnej funkcji w magazynie, np.: składowanie towaru plus transport plus skompletowanie zamówienia. „Wykorzystywanie takich modularnych podsystemów pozwala na niezwykle szybką skalowalność rozwiązania. Klienci mogą dokonywać szybkiej rozbudowy w obliczu zwiększonego wolumenu poprzez dodanie kolejnego modułu. A jednocześnie istniejący, jak i dodany moduł wykorzystują tę samą metodę pracy i procedury oraz systemy kontrolne i oprogramowanie” – mówi Magdalena Choquet.
Przykład z branży motoryzacyjnej
Magna Automotive jest głównym dostawcą komponentów dla przemysłu motoryzacyjnego.
Zakład produkcyjny Magna Automotive w Burton Business Park (Burton-on-Trent, Wielka Brytania) stanowi część Interiors Division. Zakład ten specjalizuje się w dostawach modelowanych wtryskowo wewnętrznych paneli drzwi samochodowych do pobliskiej fabryki samochodów. Zamówienia paneli do dwóch różnych modeli samochodów realizowane są na zasadach just-in-time – zamówienia przyjmowane są z jedynie czterogodzinnym wyprzedzeniem.
Sytuacja wyjściowa
Chociaż zakład produkuje panele drzwiowe tylko dla dwóch modeli samochodów, oferta dla konsumenta zawiera wiele różnych opcji uzależnionych od projektu wnętrza pojazdu. Ze względu na planowaną zmianę modelu w pierwszej połowie 2008 r., Magna Automotive była zmuszona do podniesienia liczby opcji paneli pasujących zarówno do produkowanych, jak i świeżo wdrażanych modeli. Liczba oferowanych opcji wzrosła o około 17 proc. „W rezultacie konieczne stało się zwiększenie powierzchni produkcyjnej przeznaczonej dla nowych, dodatkowych urządzeń. Wyzwaniem, przed którym stanęła firma, było znalezienie najbardziej elastycznego i kosztowo korzystnego rozwiązania, które zapewniałoby utrzymanie wyśrubowanych wymagań klientów. Dodatkowo, firmie zależało na porównaniu kosztów nowego rozwiązania z kosztami przeprowadzki do większego budynku mieszczącego się w tej samej miejscowości” – mówi Magdalena Choquet z Dematic Poland.
Poszukiwanie rozwiązania
Magna Automotive zwróciła się z prośbą do SDI Group UK (obecnie firma należy do Grupy Dematic) o zaprojektowanie systemu magazynowania i transportowania paneli wytwarzanych w części produkcyjnej. Główne cele projektowanej optymalizacji zakładały przede wszystkim uwolnienie powierzchni magazynowej pod instalację nowych maszyn produkcyjnych, a także przeprowadzenie wdrożenia przy minimalnych zakłóceniach bieżącej produkcji. „Do listy głównych celów dodano również niezwykle istotne dla Magna Automotive cele drugorzędne, takie jak wzrost wydajności w przeliczeniu na roboczogodzinę, lepszą kontrolę procesów, możliwość śledzenia na bieżąco poszczególnych aktywności, przygotowanie systemu na wzrost biznesu planowany na nadchodzące lata” – wymienia Magdalena Choquet.
Rozwiązanie: dodatkowa powierzchnia
Hala mieszcząca część produkcyjną i magazynową miała 10 m wysokości, jednak najwyższe urządzenia miały wysokość nie większą niż 4 m. Nietrudno było obliczyć, że ok. 60 proc. objętości całego budynku nie było właściwie wykorzystane. SDI zaproponowało wybudowanie dwupoziomowej antresoli o powierzchni całkowitej 1700 mkw. Przeniesienie części aktywności na antresolę zwolniło niemal 1000 mkw. powierzchni na poziomie zero. Ta dodatkowa powierzchnia została przeznaczona na nowe maszyny produkcyjne. Magna Automotive mogła zrezygnować z planów relokacji całego magazynu i produkcji do nowego obiektu.
Branża spożywcza
Firma WDX zaprojektowała i wdrożyła system transportu pustych kartonów z pomieszczenia produkcji kartonów do pomieszczenia pakowania. Grupa producencka owoców i warzyw firma Amplus w swoim magazynie koło Krakowa postawiła na wysoką automatyzację: załadunek kartonów na specjalne haki wykonują automaty załadowcze. System przebiega przez kilka pomieszczeń między innym przez ścianę ppoż. z automatyczną bramą i z wykorzystaniem unikatowego rozwiązania rozdzielania systemu transportu przy zamykaniu bramy ppoż. Transport katonów różnego rodzaju odbywa się w sposób płynny, a niewykorzystane do pakowania kartony krążą w pętli buforowej. System został wdrożony i pracuje z powodzeniem od 2013 roku.
Garnitury na wieszakach
Kolejną ciekawą instalacją, jaką wdrożył WDX w roku 2015, jest instalacja do transportu odzieży w firmie Lancerto. Priorytetem dla firmy było składowanie i transport produkowanych garniturów na wieszakach: od produkcji, przez magazyn, aż po sklepy detaliczne. Magazyn został wyposażony przez WDX w antresolę dwupoziomową, regały do składowania odzieży wieszakowej oraz system transportu z buforowaniem. System transportu zapewnia wydajność 1200 sztuk wieszaków na godzinę, co pozwala obsłudze realizować jednocześnie również inne zadania w magazynie.
Michał Klecha