Od doboru odpowiedniego sposobu wymiany baterii zależy nie tylko płynność pracy i skrócenie czasu przestojów wózka widłowego, ale także bezpieczeństwo. Wszystko przekłada się na koszty bieżącej eksploatacji maszyn, a tym samym działalności firmy. Specjaliści zwracają uwagę na to, że zakup systemu wymiany baterii jest inwestycją, tego typu rozwiązania kupujemy raz na wiele lat.
Czynników przekonujących o wadze właściwego doboru systemu wymiany baterii jest więcej. Należy do nich redukcja czasu niezbędnego na wymianę baterii, bo im lepiej dopasowany system wymiany do potrzeb konkretnego użytkownika, tym większa oszczędność nakładów pracy. Przy zakupie systemu wymiany baterii należy również wziąć pod uwagę to, jak dużą flotą wózków dysponujemy oraz to, jakie wózki planujemy kupić w przyszłości. Olbrzymie znaczenie mają kwestie bezpieczeństwa. Jednym z wyznaczników są wskazania zawarte w rozporządzeniu Ministra Pracy i Polityki Społecznej w sprawie bezpieczeństwa i higieny pracy przy ręcznych pracach transportowych określające warunki transportowania towarów.
– W zasadzie można powiedzieć, że każde oferowane rozwiązanie jest „szyte na miarę” potrzeb konkretnego użytkownika. Jeśli chodzi o wybór konkretnego rozwiązania w zakresie wyposażenia technicznego, takiego jak system wymiany baterii, najlepiej skorzystać z doradztwa firmy profesjonalnie zajmującej się tematem – mówi Mariusz Szewczyk, Dyrektor Sprzedaży Europa Środkowa i Wschodnia BENNING Power Electronics.
Jest z czego wybierać
Posiadacze wózków mają też coraz szerszy dostęp do wysokiej jakości urządzeń wymiany baterii. Dobór odpowiedniego rozwiązania przyspiesza proces wymiany, wyklucza możliwość ewentualnego uszkodzenia baterii. Sprzedawcy podkreślają, że klienta najczęściej interesuje to, by taka wymiana przebiegała szybko i sprawnie i by ładująca się bateria zajmowała jak najmniej miejsca (np. przy wymianie rolkowej bocznej na jedno pole baterii naładowanej trzeba przewidzieć jedno pole puste, czyli średnio ok. 1 m).
Boczna wymiana akumulatora w wózku widłowym, której prekursorem była firma STILL, jest stosowana coraz powszechniej. Nic dziwnego, czynność jest znacznie bardziej wygodna i bezpieczna niż tradycyjna metoda z dźwigiem.
Istnieje wiele rozwiązań technologicznych, które umożliwiają bezpieczną i szybką wymianę baterii. Są to zarówno systemy ręczne, jak i półautomatyczne oraz w pełni automatyczne. Podstawową kwestię stanowi ilość baterii będących w użytkowaniu oraz ich przeciętny czas pracy. W najlepszej sytuacji są właściciele wózków widłowych z bocznym ładowaniem, oferta obejmuje zarówno stosunkowo proste urządzenia dla małych baterii, jak i w pełni zautomatyzowane systemy wymiany.
Nie każdy użytkownik widlaków potrzebuje dużego systemu wymiany baterii, bo nie wszyscy pracują w systemie trzyzmianowym z pełnym wykorzystaniem dwóch lub trzech baterii. Często wystarczą im zatem mechaniczne środki wymiany baterii. Aby spełnić wymagania dotyczące BHP, można zastosować np. nakładki na wózki, pozwalające wyjąć baterię praktycznie bez żadnego wysiłku ze strony operatora. Są nakładki manualne (do wózków paletowych) i magnetyczne z napędem elektrycznym. Zaletą nakładek jest ich uniwersalność, oszczędność przestrzeni oraz relatywnie niski koszt zakupu. Nakładki sprawdzają się zwłaszcza wówczas, gdy flota liczy kilka wózków.
Kolejną metodę stanowią samodzielne urządzenia do wymiany baterii. Ich konstrukcję oparto na systemie magnetycznym, który pozwala w bardzo łatwo wyjąć baterię z wózka. System jest szczególnie efektywny wówczas, gdy użytkownik nie dysponuje zbyt dużą przestrzenią w akumulatorowni lub w sytuacjach awaryjnych oraz dla każdego z przedsiębiorców, dla którego flota liczy np. kilkanaście pojazdów. Przy bateriach małych (do 250–300 kg) można zastosować rozwiązanie z trolleyem, czyli wózkiem, który porusza się wzdłuż regałów bateryjnych i pozwala umieszczać na nich baterie podejmowane wcześniej z wózka (rozwiązanie ma możliwość niezależnej regulacji dwóch stołów bateryjnych i jest napędzane ręcznie). Zastosowanie trolleya eliminuje konieczność każdorazowego dojeżdżania wózkiem do regału, aby wypchnąć nań baterię i podjąć kolejną.
Boczna wymiana akumulatora w wózku widłowym, której prekursorem była firma STILL, jest stosowana coraz powszechniej. Nic dziwnego – czynność jest znacznie bardziej wygodna i bezpieczna niż tradycyjna metoda z dźwigiem. Konstruktorzy STILL-a podkreślają też proekologiczny walor bocznego sposobu wymiany. Dopuszczalne jest ładowanie baterii w wózku. Nie występuje wtedy niebezpieczne gromadzenie wodoru, ponieważ istnieje dostateczna wentylacja przedziału baterii.
HOPPECKE oferuje kilka wariantów systemów manualnej lub automatycznej wymiany baterii. Każdy wariant dopasowywany jest do potrzeb przyszłego użytkownika, co pozwala na obniżenie kosztów i oszczędność czasu. Przy konstruowaniu systemu bierze się pod uwagę liczbę niezbędnych do użytkowania baterii, wielkość oraz typ pojazdów, w których mają pracować baterie, a także planowaną dalszą rozbudowę floty elektrycznych wózków widłowych. Systemy wymiany baterii HOPPECKE to m.in. w pełni automatyczny trak Xchange FU, rozwiązanie dla użytkowników eksploatujących dowolną liczbę baterii różnej wielkości z przeznaczeniem do wszystkich typów pojazdów elektrycznych. Na życzenie system wymiany trak Xchange FU wykonywany jest z regałem nawet o sześciu poziomach składowania baterii. Takie ekonomiczne rozwiązanie oszczędza powierzchnię stacji ładowania, wszystkie baterie można wówczas ustawić wielopoziomowo. Elementami wyposażenia są: innowacyjny system laserowego pozycjonowania oraz łatwy w obsłudze dżojstik, zapewniające precyzyjne ustawienie urządzenia i pobranie odpowiedniej baterii trakcyjnej. Pozwala to na oszczędność czasu i uniknięcie błędów, jakie mogą wystąpić w przypadku ręcznej obsługi wymiany, a które mogłyby doprowadzić do uszkodzenia baterii lub wypadku operatora. Liczba eksploatowanych baterii jest praktycznie dowolna, czas wymiany baterii wynosi ok. 3 min. Rozwiązanie adresowane jest dla posiadaczy pojazdów elektrycznych z wymianą boczną oraz z wymianą górną. W ofercie HOPPECKE jest też m.in. automatyczna nakładka na wózek paletowy do bocznej wymiany baterii za pomocą elektromagnesu/przyssawki – trak Xchange PU, jak również półautomatyczna nakładka na wózek paletowy do manualnej bocznej wymiany baterii – trak Xchange MU. Ciągle powodzeniem cieszy się też mechaniczny wózek szynowy do manualnej bocznej wymiany baterii typu trolley – trak Xchange TU. Jest to rozwiązanie dla baterii o napięciu 12 i 24 V, zaprojektowane specjalnie dla elektrycznych wózków paletowych i wózków do komisjonowania poziomego z możliwą boczną wymianą baterii przy użyciu łoża rolkowego. Podwójne łoże rolkowe urządzenia umożliwia szybką wymianę baterii (cykl wynosi 2 min), a blokada gwarantuje jej bezpieczny transport. Wysokość i kąt nachylenia systemu można dowolnie regulować.
HOPPECKE oferuje kilka wariantów systemów manualnej lub automatycznej wymiany baterii. Każdy wariant dopasowywany jest do potrzeb przyszłego użytkownika, co pozwala na obniżenie kosztów i oszczędność czasu. Przy konstruowaniu systemu bierze się pod uwagę liczbę niezbędnych do użytkowania baterii, wielkość oraz typ pojazdów, w których mają pracować baterie, a także planowaną dalszą rozbudowę floty elektrycznych wózków widłowych. Systemy wymiany baterii HOPPECKE to m.in. w pełni automatyczny trak Xchange FU, rozwiązanie dla użytkowników eksploatujących dowolną liczbę baterii różnej wielkości z przeznaczeniem do wszystkich typów pojazdów elektrycznych. Na życzenie system wymiany trak Xchange FU wykonywany jest z regałem nawet o sześciu poziomach składowania baterii. Takie ekonomiczne rozwiązanie oszczędza powierzchnię stacji ładowania, wszystkie baterie można wówczas ustawić wielopoziomowo. Elementami wyposażenia są: innowacyjny system laserowego pozycjonowania oraz łatwy w obsłudze dżojstik, zapewniające precyzyjne ustawienie urządzenia i pobranie odpowiedniej baterii trakcyjnej. Pozwala to na oszczędność czasu i uniknięcie błędów, jakie mogą wystąpić w przypadku ręcznej obsługi wymiany, a które mogłyby doprowadzić do uszkodzenia baterii lub wypadku operatora. Liczba eksploatowanych baterii jest praktycznie dowolna, czas wymiany baterii wynosi ok. 3 min. Rozwiązanie adresowane jest dla posiadaczy pojazdów elektrycznych z wymianą boczną oraz z wymianą górną. W ofercie HOPPECKE jest też m.in. automatyczna nakładka na wózek paletowy do bocznej wymiany baterii za pomocą elektromagnesu/przyssawki – trak Xchange PU, jak również półautomatyczna nakładka na wózek paletowy do manualnej bocznej wymiany baterii – trak Xchange MU. Ciągle powodzeniem cieszy się też mechaniczny wózek szynowy do manualnej bocznej wymiany baterii typu trolley – trak Xchange TU. Jest to rozwiązanie dla baterii o napięciu 12 i 24 V, zaprojektowane specjalnie dla elektrycznych wózków paletowych i wózków do komisjonowania poziomego z możliwą boczną wymianą baterii przy użyciu łoża rolkowego. Podwójne łoże rolkowe urządzenia umożliwia szybką wymianę baterii (cykl wynosi 2 min), a blokada gwarantuje jej bezpieczny transport. Wysokość i kąt nachylenia systemu można dowolnie regulować.
BENNING Power Electronics wprowadził kilka lat temu do swojej oferty produkty największego na świecie dostawcy systemów wymiany baterii, firmy BHS. BENNING szczyci się wieloma instalacjami tego typu, włącznie z najbardziej zaawansowanymi, czteropoziomowymi, dwustronnymi systemami obsługującymi ponad 200 baterii w jednym miejscu. Gama obejmuje m.in. platformowe systemy wymiany baterii EBE-XX. Średni czas wymiany (wymiana boczna) baterii wynosi 2–3 min. System mieści do czterech poziomów baterii na regałach. Ustawienie regałów bateryjnych jest jedno- lub dwustronne. Do wyjęcia baterii używany jest elektromagnes lub przyssawka. Prostowniki montowane są na szczycie, na tylnej ścianie regałów lub w szafach systemowych systemu monitoringu i nadzoru akumulatorowni. Zdublowany układ jezdny pozwala kontynuować operacje nawet przy uszkodzonym jednym silniku jazdy, co zwiększa efektywność i dostępność maszyny.
Produktywność i bezpieczeństwo
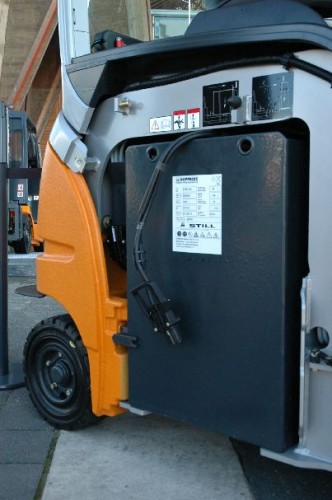
O tym jak ważna jest rola systemów wymiany przekonują też w VBR Polska, zaznaczając, że systemy wymiany w wózkach są tak różne, jak różne są same wózki. Generalnie problem narasta wraz z ciężarem baterii. Im bateria cięższa, tym wymiana jest bardziej kłopotliwa, operator ma ograniczone możliwości fizyczne do wymian ciężkich baterii.
Nie każdy użytkownik widlaków potrzebuje dużego systemu wymiany baterii, bo nie wszyscy pracują w systemie trzyzmianowym z pełnym wykorzystaniem dwóch lub trzech baterii. Często wystarczą im zatem mechaniczne środki wymiany baterii.
– Optymalne wykorzystanie przestrzeni, indywidualne potrzeby klienta i bezpieczeństwo użytkowników, zgodność instalacji z wymogami polskiego prawa, stanowią priorytet na każdym etapie projektu związanego z systemem wymiany baterii – przekonują w HOPPECKE Polska. Specjaliści tej firmy zalecają, jako najbezpieczniejszą, rolkową, boczną wymianę dodatkowej baterii w wózkach widłowych. Ponieważ starsze typy wózków mogą być wyposażone jedynie w wymianę górną, należy wówczas ograniczyć taką wymianę do minimum, jeśli chodzi o drogę przemieszczania podwieszonego ciężaru. Baterię po wyciągnięciu z wózka za pomocą wciągnika, zawiesia, suwnicy należy umieścić na przygotowanym łożu rolkowym. Dalsze operacje wymiany będą przebiegały przy dużo niższym potencjalnym ryzyku wypadku operatora.
Oferujący rozwiązania służące wymianie baterii nie pozostawiają wątpliwości, na wybór optymalnego rozwiązania ma wpływ nie jeden, a wiele czynników. M. Szewczyk (BENNING Power Electronics) zwraca uwagę np. na wysokość od podłoża do sufitu. To parametr determinujący użycie konkretnych rozwiązań w zależności od ilości poziomów składowania baterii: w systemie jednopoziomowym wynosi 3,6 m, w dwupoziomowym 4,8 m, trzypoziomowym – 6 m. Przy każdym kolejnym poziomie wymagana wysokość rośnie o kolejne 1,2 m (przyjmuje się, że podniesienie systemu o jeden poziom daje oszczędności powierzchni podłogi o ok. 17 proc.). Na produktywność ma wpływ też czas oczekiwania na wymianę baterii.
– Zwiększając wysokość składowania baterii, tracimy część czasu zaoszczędzonego na zastosowaniu systemu wymiany, ponieważ maszyna zachowuje się podobnie jak wózek widłowy, który szybciej przemieszcza towary do przodu niż podnosi do góry. Należy zwrócić uwagę, że często w dokumentacji takich systemów można znaleźć informację o ograniczaniu prędkości przy różnych wysokościach unoszenia. Kolejnym ważnym argumentem, który należy brać pod uwagę, jest to, że z bardzo wysokiego miejsca może być trudno podjąć baterię za pomocą zastępczego sprzętu w momencie wykonywania przeglądu czy naprawy maszyny. Aby to zilustrować posłużymy się przykładem. Załóżmy, że posiadamy 200 baterii. Wówczas, w zależności od wybranego systemu, na najniższym poziomie w przypadku awarii będziemy mieli zmagazynowaną następującą ilość baterii: system jednopoziomowy – 200 sztuk; dwupoziomowy 100 sztuk; trzypoziomowy 67 sztuk; czteropoziomowy 50 sztuk; pięciopoziomowy 40 sztuk oraz sześciopoziomowy 34 sztuki. Zwracając uwagę, że średnio przez cały czas 50 proc. baterii jest w trakcie ładowania, zauważamy, że niewiele dużych flot będzie mogło pracować przez dłuższy czas z tak małą ilością baterii dostępną w trybie awaryjnym. Dlatego bazując na tym i na odpowiednio krótkim czasie wymiany baterii można dobrać skrojony na miarę system, w zależności od ilości baterii: 1–49 sztuk zmagazynowanych baterii – system jednopoziomowy; 50–139 sztuk – dwupoziomowy; 140–299 – trzypoziomowy; 300–619 – czteropoziomowy; od 620 sztuk- pięciopoziomowy – wylicza M. Szewczyk.
Adam Brzozowski