Centrum logistyczne ICT Poland – 60 tys. miejsc paletowych w automatycznym magazynie.
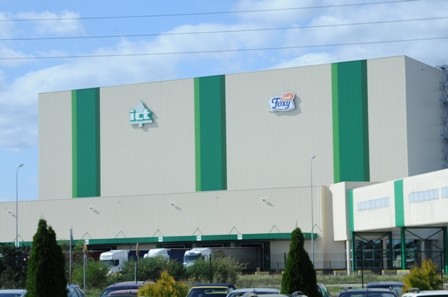
"Co czwarta rolka papieru toaletowego na polskim rynku, pod własną marką Foxy i wieloma handlowymi, pochodzi z naszej fabryki."- mówi Dariusz Drzazga dyrektor logistyki i zakupów ICT Poland z Kostrzynia, największego zintegrowanego zakładu produkcji i przetwarzania papieru higienicznego, który należy do włoskiego koncernu ICT Industrie Cartarie Tronchetti S.p.A. Skala produkcji tłumaczy, dlaczego dla towaru o małej wartości dodanej zdecydowano się na budowę w pełni automatycznego centrum logistycznego.
Argumenty "Za"
Jedna z najpoważniejszych trudności na drodze do budowy automatycznego magazynu typu silos, dotyczy określenia perspektywy czasu zwrotu z inwestycji, która wynosi często dekadę. Ale mimo tego kluczowym argumentem „Za” realizacją takiego magazynu jest wydajność dystrybucji, jaką osiąga się stosują automatyzację procesu logistycznego, poprzez pracę układnic i przenośników transportowych. "Zdecydowaliśmy się na budowę automatycznego magazynu z powodu ciągłego rozwoju fabryki w Kostrzynie, a tym samym pojawiające się potrzeby optymalizacji procesu jego wytwarzania. Chcieliśmy zmienić priorytet, aby magazyn nie rządził produkcją."- tłumaczy Dariusz Drzazga. ICT Poland korzystał głównie z wynajmowanej zewnętrznie powierzchni magazynowej, która była rozproszona w różnych lokalizacjach. Przy trwającej nieustanie rozbudowie fabryki, stanowiło to piętę achillesową producenta, utrudniając planowanie produkcji. Brak wolnej powierzchni składowania potrafił spowolnić a nawet zatrzymać linie. Magazyn rządził produkcją, co przy skali 90 tys. palet z papierem toaletowym, który produkuje kostrzyński zakład, stanowiło wąskie gardło.
Dylematy koncepcyjne
W 2010 roku przy fabryce wybudowano nowe centrum dystrybucji o powierzchni użytkowej 16 tysięcy metrów kwadratowych. Jego głównym elementem stał się magazyn wysokiego składowania na 60 tysięcy miejsc paletowych, w systemie podwójnej głębokości składowania. Instalację obsługuje 9 układnic wyposażonych w teleskopowe widły, tak by mogły obsłużyć podwójne gniazda palet. Nim jednak powstał silos i wybrano dostawcę instalacji zatrudniono firmę konsultingową. "Nikt nie rodzi się z tego rodzaju specjalistyczną wiedzą. Dla nas konsultingowa firma wykonała ogromne zadania na etapie przedprojektowym, który trwał ponad rok." - opowiada dyrektor logistyki i zakupów. W tym czasie rodziły się rozmaite warianty rozwiązań, aż dopracowano się ostatecznej koncepcji przyszłej inwestycji. Powstała ponad tysiąc stronicowa dokumentacja przedprojektowa. Określono w niej funkcjonalność instalacji, brzegowe założenia techniczne dla dostawcy systemu, zdefiniowano zasady odbioru i testów urządzeń. Jak wspominają w ICT- skorzystanie z usług firmy konsultingowej było bardzo dobrą decyzją, pozwoliło profesjonalnie przygotować się inwestorowi do rozmów z oferentami.
Między fabryką a magazynem
Zlecenie na realizację inwestycji automatycznego magazynu otrzymała firma SSI Schäfer. Zakres dostaw i usług w tym kontrakcie dotyczył wzniesienia stalowej konstrukcji regałów wysokiego składowania w samonośnym magazynie silosie, dostarczenia automatycznych układnic, ale również powiązania nowego magazynu z linią produkcji poprzez rolkowy system transportu palet. –Wykonaliśmy ciąg transportowy o długości prawie dwóch kilometrów, który połączył fabrykę z magazynem wysokiego składowania. Na początku linii przenośników zastosowano windy, które umożliwiły zniwelowanie wysokości, między halą zakładu produkcyjnego a magazynem - tłumaczy Bartosz Jankowski z firmy SSI Schäfer. Obie hale oddalone są od siebie o kilkaset metrów. Silos zrealizowano z dala od fabryki, aby nie zabierać terenu pod dalsza rozbudowę części produkcyjnej w przyszłości. Poza tym zaważyły względy bezpieczeństwa pożarowego. Magazyn wypełniony łatwopalnym papierem, stwarza ryzyko, mimo że wyposażony został w automatyczny system tryskaczowy. Obiekty połączył korytarz zbudowany kilkanaście metrów nad ziemią. Stąd potrzeba transferu towaru między dwiema częściami ICT. Między nimi prowadzą dwie linie przenośników rolkowych, łączące strefę wydania w fabryce i obszar przyjęcia w magazynie.
SMS do kierowcy
W magazynach automatycznych, kluczowym ogniwem powodzenia inwestycji jest software. Jego zadaniem polega zarówno na zarządzaniu lokacjami w przestrzeni regałowej i sterowaniem maszyn pracujących w instalacji. Układnice, przenośniki, windy, bramki obrysowe stanowią układ zależny od siebie i dynamiczny, generują szereg informacji wzajemnych, które dodatkowo muszą współgrać z danymi o zamówieniach, które wysyła aplikacja ERP. Jako aplikację WMS, SSI Schäfer stosuje własny produkt pod rynkową nazwą „ant”, który został opracowany z myślą o zaawansowanych wdrożeniach w magazynach automatycznych. Oprócz sterowania strumieniem towarów aplikacja, posiada dodatkowe funkcje kierowania układnicami, które gwarantują efektywne wykorzystanie miejsca. Przy czym jest to oprogramowanie otwarte na nowe funkcjonalności, wynikające ze specyfiki pracy klientów. Bardzo interesującą funkcją jest w nim zarządzanie yard management do nadzorowania wewnętrznego placu manewrowego. –Kierowcy ciężarówek nie czekają u nas dłużej niż 20 minut, system informatyczny poprzez komunikat sms, wskazuje czas załadunku i numer rampy magazynowej. W sumie mamy dedykowanych 700 funkcji na softwarze - mówi Dariusz Drzazga.
W tempie 460 palet na godzinę
Każda z 600 palet trafiająca do wysokiego magazynu w ciągu godziny jest dwukrotnie sprawdzana pod względem poprawnego ułożenia ładunku. Pierwsza bramka kontrolna znajduje się na początku linii przenośników jeszcze w fabryce. Jednostka paletowa, w której czujniki stwierdzą nieprawidłowość odsyłana jest do bufora. Ładunki poprawne trafiają po dwa do windy, a następnie w kilkuminutową podróż przez górny korytarz przenośnikami rolkowymi do strefy przyjęcia magazynu. Tuż przed samym silosem następuje powtórna kontrola obrysu ładunku. "Drugą strefę bramek zastosowaliśmy po zaleceniach konsultantów. Długa nitka transportowa, podczas której następuje zmiana kierunku jazdy na obrotnicach może zmienić ułożenie ładunku. Czuwa nad tym automatyczna kontrola." - mówi Dariusz Drzazga. Prawidłowo ułożona paleta z ładunkiem dostaje wolną drogę od systemu do jednego z kilku pół odkładczych, skąd zabrana zostanie przez układnicę w pierwsze wolne miejsce na regale. Dopiero w nocy dokonuje się proces rekonfiguracji ułożenia towaru w magazynie zgodnie z zasadą ABC.
W strefie wydań można załadować do 460 palet na godzinę, co odpowiada 15 ciężarówkom. Zbudowano w niej szereg linii złożonych z grawitacyjnych przenośników rolkowych, do których jednostki paletowe dostarczają elektryczne wózki szynowe, poruszające się wzdłuż stacji wydań. Każdy z wózków jeździ po stałej trasie i obsługuje kilka stacji w swoim zasięgu. Pobiera dostarczone z magazynu przez układnice po 2 palety jednocześnie. Dzięki znajdujących się na platformach rolkach są one wciągane na wózek, a następnie spychane na stacji docelowej wprost na linię grawitacyjną. Stąd trafiają do ładowni ciężarówek.
Magazyn ICT Poland zaprojektowany jest już z myślą o spodziewanym wzroście produkcji papieru. Ponadto projekt uwzględnia kolejny etap rozbudowy obejmujący dodatkowo 30 tysięcy stanowisk do składowania palet.
Krzysztof Pograniczny
Więcej o SSI Schäfer - http://www.ssi-schaefer.pl/
Więcej zdjęć z obiektu ICT Poland TUTAJ