Dominujący trend w światowym przemyśle motoryzacyjnym zakłada zastępowanie pracowników robotami. Podejście Toyoty jest inne – udział ludzi w procesie produkcji jest niezbędny, a zadaniem robotów jest ułatwienie im pracy.
Amerykańska fabryka Toyota Motor Manufacturing Kentucky w Georgetown jest największym i najnowocześniejszym zakładem japońskiego koncernu. W halach o powierzchni ponad 750 tysięcy metrów kwadratowych powstaje co roku 550 tysięcy samochodów – sedanów Toyota Camry i Avalon oraz limuzyn Lexus ES. W tym roku Toyota zakończyła wartą 1,33 miliarda dolarów modernizację zakładu i zatrudniła 700 dodatkowych pracowników z myślą o produkcji nowej generacji najpopularniejszego w USA modelu Camry, opartego na nowej platformie TNGA.
Bez inwazji robotów
Mimo tych inwestycji, udział pracowników w montażu pojazdów nie zmniejszył się. „Stopień automatyzacji procesu nie jest dziś większy niż 15 lat temu” – mówi Wil James, prezes Toyota Motor Manufacturing Kentucky. „Maszyny znakomicie wykonują powtarzalne zadania, ale nie są w stanie same poprawiać wydajności ani jakości pracy. To potrafią tylko ludzie”.
Właśnie dlatego choć od dekady udział robotów w procesach produkcyjnych w zakładach Toyoty pozostaje na poziomie średnio 8 procent, wydajność produkcji nieustannie rośnie. Kluczem do sukcesu jest tu japońskie słowo kaizen, oznaczające ciągłe doskonalenie, w którym uczestniczą wszyscy pracownicy Toyoty. To oni z bliska obserwują codzienną pracę, dzięki czemu są w stanie zauważyć niedoskonałości procesów i zaproponować ich usprawnienia.
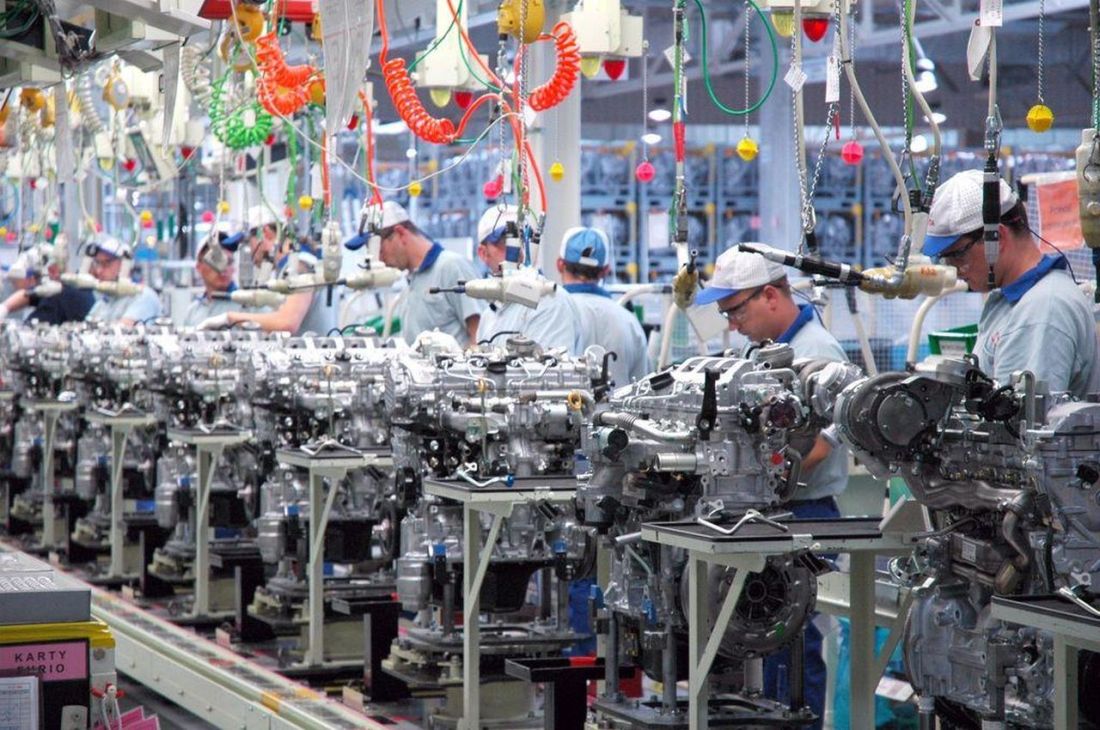
Przykładem może być racjonalizacja metody montażu zbiorników paliwa w Kentucky. Wcześniej ciężki zbiornik był unoszony przez podnośnik, po czym robotnicy mocowali go obejmami i śrubami. Wiązało się to z pracą w niewygodnej pozycji z rękami uniesionymi do góry, więc pracownicy wymyśli sprytne urządzenie, które jednym ruchem unosi zbiornik, ustawiając go we właściwej pozycji, po czym mocuje go do nadwozia.
Czyżby robotnicy sami zlikwidowali swoje miejsca pracy? Nic z tych rzeczy – zyskali nowe, ważne zadanie. Dokonują teraz kontroli jakości montażu zbiorników, wnikliwie sprawdzając wszystkie zamocowania i połączenia. Żadna maszyna nie potrafi zrobić tego lepiej od nich.
TNGA – kaizen do kwadratu
Wydawałoby się, że rezygnacja z zastępowania ludzi robotami pogarsza zdolność konkurencyjną Toyoty w stosunku do firm, które właśnie w ten sposób obniżają koszty produkcji. Japoński koncern zdecydował się jednak na inną drogę redukcji kosztów – poprzez rozwój technologii. Jest to naturalne rozwinięcie słynnego systemu produkcyjnego Toyoty, polegającego na optymalizacji zarządzania zasobami. Służy temu nowa architektura TNGA (Toyota New Global Architecture), obejmująca nie tylko modułową, zunifikowaną konstrukcję elementów pojazdu, w tym przede wszystkim płyty podłogowej, struktury nadwozia, zespołu napędowego i sterowania, ale i technologię oraz organizację produkcji.
Tworząc TNGA, Toyota położyła nacisk na lepsze wykorzystanie materiałów i projektowanie pojazdów w sposób pozwalający zmniejszyć masę oraz wymiary elementów, a przy tym uzyskać optymalne położenie środka masy, co zapewnia lepsze własności jezdne i osiągi, a także zmniejsza zużycie paliwa. Zwrócono także uwagę na unifikacje podzespołów, w tym silników i struktur – liczbę platform ograniczono z około 100 do mniej niż dziesięciu. Jednocześnie wprowadzono procesy produkcyjne, umożliwiające wytwarzanie kilku modeli samochodów na tej samej linii bez konieczności przerw w produkcji.
TNGA to również zmiany w procesie produkcji – zmienił się nawet kształt linii produkcyjnej. Wielkie przenośniki, podwieszone na szynach zamocowanych pod dachem zastąpiono autonomicznymi wózkami, które przewożą silniki po ścieżkach wyznaczonych elektronicznie na podłodze. Tego rodzaju rozwiązania pozwoliły ograniczyć rozmiary hal produkcyjnych, co zmniejsza wydatki na oświetlenie, ogrzewanie i klimatyzację, a w przypadku nowych zakładów – również na ich budowę.
W koncepcji TNGA roboty nie odgrywają głównej roli, lecz są pomocnikami pracowników, ułatwiającymi ich pracę i pozostawiającymi więcej czasu na innowację. To stymuluje dalsze udoskonalenia w duchu kaizen, dzięki któremu Toyota stała się największą i najbardziej nowatorską firmą motoryzacyjną świata.
źródło: Toyota