Postępująca globalizacja zmusza producentów samochodów do ciągłego skracania czasu produkcji i optymalizacji przebiegu procesów wytwórczych. To zaś ma bezpośredni wpływ na działalność ich dostawców, którzy muszą tak zorganizować swoje procesy logistyczne, aby sprostać zapotrzebowaniu na określone części. Aby to osiągnąć, Continental w swoim zakładzie w Regensburgu postawił na model „Just in Sequence” będący rozwinięciem koncepcji „Just in Time“ (JIT), zgodnie z którym materiał wydawany jest działowi produkcji w określonej kolejności zgodnej z kolejnością zamówień. To jednak nie wszystko: firma zadbała również o przejrzystość procesów logistycznych wdrażając innowacyjny system, w ramach którego każdy wózek transportowy został wyposażony w kolumnę sygnalizacyjną zintegrowaną z radiowym systemem przyzywowym. System w czasie rzeczywistym informuje o wszelkich zakłóceniach, umożliwiając maksymalne skrócenie czasu reakcji, a tym samym zapewniając znaczne oszczędności czasu i kosztów oraz – a może przede wszystkim – pełną transparentność procesów.
O Continental Regensburg
Zakład produkcyjny w niemieckim Regensburgu należy do grupy ponad 300 obiektów międzynarodowego koncernu Continental. Na powierzchni niemal 22 tys. m2 pracuje tu 8000 pracowników. Największą dumą zakładu jest utworzone w 2001 r. centrum logistyczne, które w 2016 roku przyjmowało ok. 1150 palet dziennie, a wydawało ok. 390 palet dziennie. Obiekt dysponuje m.in. zautomatyzowaną siecią transportową łączącą dział logistyki z produkcją. Umożliwia ona obsługę towarów w modelu „Just in Sequence”, zapewniając bezpieczeństwo, niezawodność i wysoką jakość dostaw.
„Just in Sequence“ – królowa logistyki
Koncepcja „Just in Sequence“(JIS) z roku na rok zyskuje na popularności zarówno wśród dostawców dla branży motoryzacyjnej, jak i w sektorze logistyki. Podobnie jak w metodzie JIT, jej podstawowym założeniem jest realizacja dostaw materiału w odpowiedniej ilości, we właściwym czasie i bezpośrednio na miejsce produkcji. JIS idzie jednak jeszcze o krok dalej i postuluje, aby materiał dostarczany był dokładnie w takiej kolejności, jakiej wymaga proces wytwórczy. Zaletą takiego podejścia jest z jednej strony oszczędność zasobów materiałowych i przestrzeni magazynowej, a z drugiej – zwiększenie elastyczności produkcji i montażu, skrócenie czasu wytwarzania oraz redukcja kosztów przy zachowaniu, a nawet zwiększeniu produktywności procesów.
Z zalet JIS korzysta także zakład Continental w Regensburgu. Producent wdrożył regułę sekwencyjności w całym procesie dostaw: zamówiony przez dział produkcji materiał zostaje automatycznie pobrany z jednego z 6200 stanowisk tworzących długi na 60 m i wysoki na 30 m regał wysokiego składowania. Jego dostawą do hali produkcyjnej zajmuje się autonomiczny wózek transportowy.
Transport w „czarnej strefie“
Stałe dostawy materiału do produkcji zabezpiecza w Regensburgu dwanaście automatycznie sterowanych, samobieżnych pojazdów poruszających się po zamontowanych w podłodze szynach elektrycznych (ilustracja 2). Docelowo system powinien zapewniać realizację poszczególnych zamówień produkcyjnych w czasie ok. 1 godziny.
Ok. 130-metrowy dystans, jaki muszą pokonać wózki, początkowo był swego rodzaju „czarną strefą” – nie można było bowiem sprawdzić, co w danym momencie dzieje się z pojazdem. Jeśli na trasie przejazdu wydarzyło się coś, co zakłóciło normalną pracę wózka, potrzeba było niekiedy 10 minut, aby sterownik PLC wysłał komunikat do centrali. Przy ok. 10 zakłóceniach w tygodniu zakład tracił w ten sposób ok. 100 cennych minut. A przyczyn problemów było bez liku – od przerw w zasilaniu szyny po zakrycie fotokomórki wózka dokumentami zamówienia.
W poszukiwaniu rozwiązania
Mathias Meier, kordynator zespołu ds. projektowania przemysłowego w zakładzie Continental w Regensburgu, od dawna szukał rozwiązania tego problemu: “Ze względu na to, że zdecydowaliśmy się wprowadzić w życie koncepcję Just in Sequence, skrócenie czasu reakcji na zakłócenie nawet o jedną minutę było dla nas na wagę złota”.
Rozważane dotąd rozwiązania, np. systemy oparte na sieci WLAN, okazywały się dla firmy zbyt drogie, a dodatkowo wymagały czasochłonnej instalacji i zaangażowania działu IT. I wówczas nastąpił przełom: w zakładzie w Regensburgu pojawili się przedstawiciele firmy Werma.
– Po pierwszej rozmowie od razu otrzymaliśmy i zainstalowaliśmy zestaw testowy systemu przyzywowego firmy Werma. Był niezwykle prosty w instalacji i gotowy do natychmiastowego wdrożenia – wspomina Mathias Meier.
Pod koniec 2014 r. na każdym z 12 pojazdów transportowych odpowiedzialnych za dostawy materiału między centrum logistycznym a halą produkcyjną zainstalowano nadajnik radiowy oraz kolumnę sygnalizacyjną firmy Werma z dwoma modułami: zielonym i żółtym. To wystarczyło, aby stworzyć kompletny system przyzywowy bazujący na bezprzewodowej sieci radiowej „Wireless Information Network” (WIN) i działający na zasadzie niedrogiego systemu gromadzenia danych maszynowych do celów optymalizacji dostaw, produkcji i montażu.
Kolumna sygnalizacyjna jako interfejs radiowy
Jako interfejs służy tu kolumna sygnalizacyjna zamontowana na pojeździe. Można ją bowiem w prosty sposób, na zasadzie plug & play wyposażyć w nadajnik radiowy firmy Werma – dzięki zamkowi bagnetowemu oba urządzenia można zintegrować mechanicznie i elektrycznie w ciągu zaledwie kilku sekund. Nadajnik drogą radiową przekazuje informacje o stanie poszczególnych modułów kolumny bezpośrednio do odbiornika podłączonego przez złącze USB do centralnego komputera (nowsza wersja odbiornika komunikuje się serwerem poprzez interfejs Ethernet, co pozwala na umieszczenie urządzenia WIN Master w dowolnym miejscu).
W zakładzie w Regensburgu komputer ten znajduje się piętro niżej – w biurze Mathiasa Meiera. Za każdym razem, gdy kolumna pojazdu zmienia status na awaryjny, na ekranie PC natychmiast pojawia się stosowny komunikat (ilustracja 3). Informacja o awarii dostarczana jest także w formie SMS-a wszystkim pracownikom danej zmiany. Dzięki temu mogą oni natychmiast przyjrzeć się problemowi i szybko usunąć jego przyczynę.
Aby mimo znacznego dystansu sygnał z kolumny dotarł do odbiornika, na trasie przejazdu wózków rozlokowano dodatkowy nadajnik, który pełni funkcję „repeatera“ – przekazuje sygnał dalej. Pozwoliło to znacznie zwiększyć zasięg przestrzenny systemu.
Komunikaty o błędach w czasie rzeczywistym
Jak podkreśla Mathias Meier, efekt wprowadzenia systemu przyzywowego firmy Werma przerósł jego oczekiwania: – Niewątpliwie ogromną zaletą systemu jest szybkość reakcji. Komunikaty o błędach wysyłane są niemal w czasie rzeczywistym.
Ów szybki przepływ informacji umożliwia zaś natychmiastową reakcję, redukując do minimum straty spowodowane nieplanowanymi przestojami pojazdów.
Co więcej, wszystkie przesyłane sygnały są archiwizowane w dostarczonej z systemem bazie danych i – dzięki możliwości ich przetwarzania i wizualizacji w oprogramowaniu WIN – zapewniają pełną transparentność przebiegu procesów logistycznych za jednym naciśnięciem klawisza. Dostępne w oprogramowaniu moduły oferują bowiem szereg użytecznych funkcji i możliwości raportowania, zapewniając pełny wgląd w całość logistyki zakładu i umożliwiając różnorodne analizy pozwalające na optymalizację procesów.
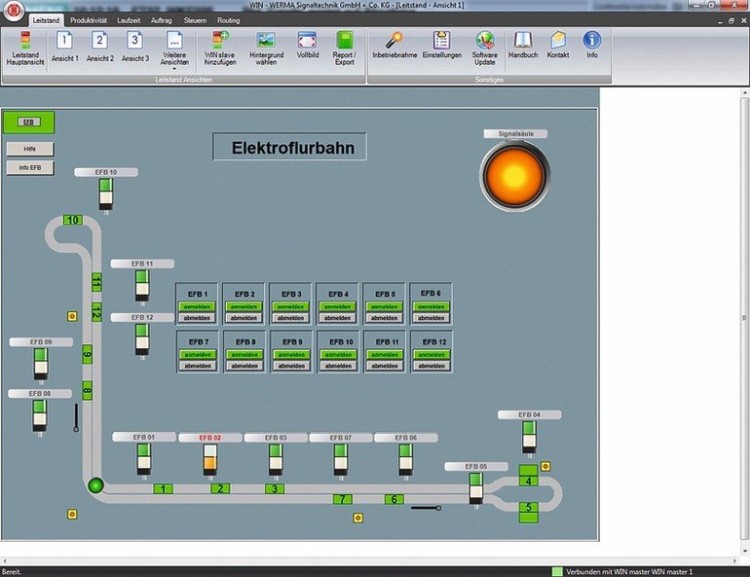
Ilustracja 2: Dostarczone z systemem oprogramowanie stale wyświetla aktualny status pojazdów transportowych. Jego funkcje można łatwo dostosować do potrzeb użytkownika, zaś prosty interfejs zapewnia intuicyjną obsługę systemu.
Aktualności, wydarzenia, komentarze, branżowe czasopisma - bądź na bieżąco. Zapisz się do newslettera portalu logistyczny.com - KLIKNIJ