Każdy zakład produkcyjny musi utrzymywać w gotowości pewną ilość surowców czy półproduktów stanowiących bufor zapasowy na wypadek nieoczekiwanych wahań w procesie produkcji. Z kolei na drugim krańcu procesu konieczna jest przestrzeń do składowania gotowego wyrobu aby „nie zakorkować” linii produkcyjnej. Dlatego tak ważny z punktu widzenia szczupłego zarządzania procesem jest sprawnie funkcjonujący magazyn zarządzany systemem WMS zgodnie z koncepcją lean production.
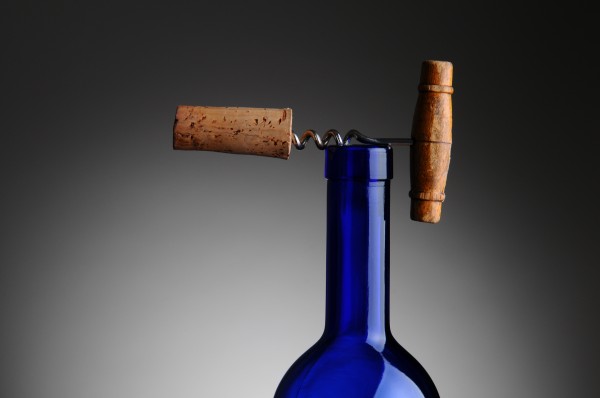
Magazyn wąskim gardłem?
Magazyny współpracujące z produkcją zgodnie z lean management muszą zapewniać surowce tylko wtedy, kiedy jest to potrzebne (system pull) i odbierać wyroby gotowe jak najszybciej, nie tworząc niepotrzebnych buforów. W wielu zakładach produkcyjnych jest to duże wyzwanie, szczególnie wtedy, gdy brak jest zaawansowanego systemu WMS. Zdarza się, że magazyn dostarcza zbyt dużą ilość towaru w niewłaściwym czasie, zabezpieczając produkcję na zasadzie „na wszelki wypadek”. Nagła potrzeba dostarczenia surowców nie może być szybko zaspokojona, gdy komunikacja między produkcją a magazynem będzie zawodzić. Tak więc magazyny odgrywają krytyczną rolę w lean management.
Dla firm produkcyjnych magazyn jest równie istotny co maszyny, które firma posiada. Braki magazynowe lub źle zorganizowany magazyn mogą skutecznie zniwelować wysiłki wdrożenia lean managemnt w całej firmie. Opóźnienia w dostawach surowców mogą powodować przestoje lub konieczność zmiany harmonogramu produkcji w ostatniej chwili. Powoduje to zwiększanie kosztów produkcji z zmniejszenie wartości dodanej dla klienta. Jeśli towar jest dostępny w magazynie, ale jego odnalezienie lub „wydobycie” jest czasochłonne, może to również powodować opóźnienia w produkcji. - Istotnym elementem wdrażania lean management jest dobra wymiana informacji pomiędzy magazynem i działami produkcji. Przekazywanie planów produkcyjnych oraz zapotrzebowań na materiały z odpowiednim wyprzedzeniem daje szansę na prawidłowe zaopatrywanie produkcji w surowce. – mówi Maciej Brzeziński, Senior Project Manager w Exact Sortware Poland.
Często przyczyną problemów na styku magazyn-produkcja jest brak prawidłowej integracji pomiędzy systemem nadrzędnym (ERP lub innym systemem zarządzania produkcją) odpowiedzialnym za opracowanie harmonogramów produkcji a system WMS, który jest odpowiedzialny za realizację przepływów materiałowych zapewniającą sprawne zaopatrzenie i odbiór z produkcji oraz przesunięcia międzyoperacyjne.
Prawidłowa interpretacja i przekształcanie harmonogramów/planów produkcji przez WMS w odpowiednie ruchy materiałowe często stanowi złożone zadanie sterowania, które rozwiązane w niewłaściwy lub tylko w niedostateczny sposób sprawia, że magazyn staje się „wąskim gardłem”. - Magazyn łatwo staje się „wąskim gardłem” również w przypadku nieprzemyślanego podziału zadań zarządzania pomiędzy systemem nadrzędnym a systemem WMS. Ze względu na bardzo różnorodny zakres zarządzania produkcją oferowany przez różne systemy w zależności od możliwości ich możliwości system WMS może albo przejmować pewne funkcje sterujące zaopatrzeniem i odbiorem albo pełnić rolę stricte wykonawczą. – mówi Andrzej Bobiński, Prezes Zarządu Logifact-Systems.
Rola magazynu w prawidłowym funkcjonowaniu przedsiębiorstwa zaczyna się już od momentu przyjęcia surowców do magazynu. Na tym etapie istotne jest, by przyjmowany towar był dobrej jakości, sam proces przyjęcia przebiegał płynnie, a ilości fizyczne zgadzały się z tymi awizowanymi. - Jednak największym problemem w firmach produkcyjnych często okazuje się organizacja procesu wydań. Przy dobrym zarządzaniu pracą całego przedsiębiorstwa brak odpowiedniego wsparcia technicznego w obszarze wydań z magazynu może prowadzić do dużych spadków wydajności, problemów jakościowych i ilościowych. – podkreśla Dominik Jezierski, Konsultant ds. EMS w firmie DataConsult.
Problemy i rozwiązania
Jednym z częstych problemów w zakładach produkcyjnych jest brak przepływu informacji w czasie rzeczywistym na styku magazynu i produkcji. Fakt zgłoszenia zapotrzebowania na towar bez systemu WMS wymaga poszukiwania wózkowego, który dostarczy nam następną partię towaru. Z kolei dostawa towaru na granicy magazynu i produkcji niekiedy skutkuje pozostawieniem palety „w próżni” do momentu, aż ktoś jej z produkcji nie zauważy. - System WMS pracujący na zadaniach, taki jak Astro WMS, automatycznie generuje polecenia operatorom. Odłożenie palety w miejscu pośrednim przez magazyn skutkuje wygenerowaniem zadania do kolejnego operatora, odpowiedzialnego za pobranie palety do stanowiska produkcyjnego. – mówi Marcin Figlarek, Konsultant ds. logistyki i systemów WMS w firmie Consafe Logistics.
Inny problem stanowić może płynne zaopatrzenie produkcji w odpowiednich porcjach. W tym wypadku chodzi głównie o odpowiednie przetworzenie przez WMS harmonogramów produkcji tak, aby zadania kompletacji na potrzeby zaopatrzenia produkcji jak również same ruchy materiałowe z magazynu do buforów produkcyjnych uwzględniały zarówno cechy dostarczanych materiałów jak i wielkość buforów produkcyjnych oraz zużycie materiałów produkcyjnych. - Pojęcie „harmonogramy/plany produkcji” ma charakter ogólny oznacza to, że każdorazowo przy konkretnej realizacji należy bardzo dokładnie przeanalizować jakie dane i w jakiej formie będą przesyłane do systemu WMS po to, by opracować odpowiednie algorytmy sterujące zaopatrzeniem produkcji zapewniającym jej płynność, a jednocześnie minimalizując zapasy produkcji w toku. – mówi Andrzej Bobiński z Logifact-Systems.
Konieczny z punktu widzenia zachowania ciągłości produkcji jest właściwy nadzór nad zapasami w obszarze produkcji w toku. Ta funkcjonalność wymaga przede wszystkim, żeby WMS obejmował swoim nadzorem bufory produkcyjne i międzyoperacyjne. - Oznacza to, że zarówno zasilanie (transporty zaopatrzeniowe) jak i opróżnianie buforów (zużycie produkcyjne) oraz transporty międzyoperacyjne są sterowane i nadzorowane przez WMS. Na tej podstawie możliwe jest nie tylko opracowanie szczegółowych raportów o zapasach dla produkcji w toku, ale także stworzenie odpowiedniego systemu ostrzegania (alertów) automatycznie powiadamiającego odpowiedni szczebel zarządzania o zbliżaniu się do, lub przekroczeniu założonych normatywów. – tłumaczy Andrzej Bobiński.
Dla każdego surowca lub wyrobu, który ma określoną datę przydatności, możliwe jest określenie minimalnego okresu przydatności i zastosowania algorytmu FEFO (First Expired First Out), co przy wydaniach pozwala na jak najlepsze wykorzystanie składowanych na magazynie surowców. - Do produkcji używane są tylko surowce z odpowiednio długim terminem przydatności, a system wydaje w pierwszej kolejności surowce z najkrótszym terminem przydatności. – wyjaśnia Dariusz Kuśmierek, Dyrektor Działu Produkcji Systemów ERP w Asseco Business Solutions SA. Daje to maksymalne wykorzystanie surowców i półproduktów, obniżając poziom strat w materiałach do minimum.
Pamiętajmy, że magazyn w zakładzie produkcyjnym, to także składowanie wyrobów gotowych, magazyn może zatem pełnić kluczową funkcję w realizacji zadań dystrybucyjnych – bezpośrednio z zakładu produkcyjnego do pośredników lub odbiorców końcowych. Odpowiednie zinformatyzowanie przepływów jest zatem niezbędne. - W magazynie wyrobów gotowych ważne jest śledzenie partii produktu – możemy zablokować wybraną partię, a z magazynu przyprodukcyjnego zaopatrywać zakład w towar odpowiedniej jakości, minimalizując negatywny wpływ magazynu i dostaw na wydajność i płynność pracy linii produkcyjnej. – zaznacza Piotr Kulesz, Sales Manager w PSI Polska.
Odchudzające WMS-y
Gama dostępnych na rynku systemów WMS jest bardzo szeroka. Wiele spośród tych aplikacji wyposażonych jest w funkcje, które z powodzeniem pomagają w rozwiązywaniu wyżej opisanych problemów.
Na przykład Astro WMS w ofercie firmy Consafe Logistics posiada szereg funkcjonalności, dzięki którym łatwiej jest wprowadzić zmiany w zakładzie z wykorzystaniem lean management. Praca na zadaniach, a nie na dokumentach minimalizuje przestoje w miejscach pośrednich. - Dzięki tzw. multicyklom operatorzy wózków widłowych mogą dostawać różne zadania on-line, minimalizując dzięki temu jazdę „na pusto”. – tłumaczy Marcin Figlarek. - Moduł Performance Management z kolei powiadomi o wszelkich możliwych opóźnieniach w dostawach do produkcji i umożliwi symulacje, dzięki którym można podjąć odpowiednie decyzje organizacyjne. - dodaje nasz rozmówca. Jest to szczególnie ważne w przypadku np. dostaw surowców do lakierni – lakiernia powinna mieć jak najmniej przestojów w produkcji.
Coraz częściej wymagane jest bieżące rejestrowanie zużycia surowców i generowanie zadań pobierania małych partii towaru na stanowisko produkcyjne. - Jeśli system MES nie obsługuje dobrze tego procesu lub nie jest on wdrożony, wówczas moduł Astro WMS o nazwie Material Supply może wesprzeć ten proces, raportując bieżące zużycie materiałów na każdej linii produkcyjnej. – mówi Marcin Figlarek.
System logifact®WMS wspomaga bezpośrednie zarządzanie procesami magazynowymi i produkcyjnymi w czasie rzeczywistym zapewniając integrację obszarów produkcyjnych i magazynowych w procesach przepływu materiałów, zapewniając jednolite środowisko zarządzania i eliminując dzięki temu bariery na styku magazyn-produkcja. Tym samym zapewnia zintegrowane zarządzanie ogółem procesów przepływu ładunków z uwzględnieniem surowców, półwyrobów, wyrobów gotowych czy opakowań. Przy zastosowaniu systemu oznakowania kodami kreskowymi oraz terminali radiowych, w oparciu o pełny nadzór i rejestrację zadań transportowych, system zapewnia transparentność przeprowadzanych operacji i dostarcza on-line wiarygodnych informacji o:
- stanie zapasów w magazynach surowców/półwyrobów, wyrobów gotowych oraz buforach produkcyjnych (zapasy w toku)
- przepływach ładunków w magazynach i na produkcji
- zużyciu dostarczonych materiałów produkcyjnych, powstającej produkcji, niewykorzystanych surowcach przeznaczonych do zwrotu do magazynu, odpadach użytkowych itp.
- efektywności pracy operatorów
- Powyższe zapewnia możliwość efektywnego i wiarygodnego rozliczania materiałowego produkcji tzn. ile i jakie materiały zużyto do wyprodukowania określonej ilości wyrobu/półwyrobu. Obecnie system WMS rozszerzany jest o moduł rejestracji czasów pracy. Po przekazaniu tych danych do systemu ERP możliwe staje się szybkie i poprawne rozliczenie produkcji a także szersza analiza i ocena kosztów produkcji. – mówi Andrzej Bobiński.
Firma DataConsult również posiada bardzo dużo wdrożeń w przedsiębiorstwach produkcyjnych, w różnych gałęziach przemysłu. System ExpertWMS® działa głównie na magazynach, ale także wspiera samą produkcję dzięki swojej szerokiej funkcjonalności. - Zaletą systemu jest możliwość tworzenia technologii, receptur, które wykorzystuje się w procesie produkcji. WMS wspomaga także planowanie. Może automatycznie tworzyć zlecenia produkcyjne, na podstawie zamówienia sprzedaży. – zaznacza Dominik Jezierski. Kolejną zaletą systemu jest to, że prowadzi całkowitą zgodność ilościową i jakościową przy wydawaniu surowców, komponentów na produkcje. Możliwość pomyłki w tym przypadku jest znikoma.
Wspomniano już, że elementem kluczowym dla systemu WMS jest utrzymywanie pożądanych stanów minimalnych i wysyłanie zapotrzebowania np. do dostawców zewnętrznych celem automatycznego zamawiania towaru. - System WMS ostrzega o spadku poziomu zapasów poniżej założonego poziomu. - I tak na przykład PSIwms za pomocą modułu Event Management informuje konkretnych użytkowników o wybranych nieprawidłowościach w pracy magazynu. Dzięki temu unikamy strat, eliminując problemy u źródła. – mówi Piotr Kulesz z PSI Polska.
PSI proponuje de facto dwa różne systemy magazynowe – niezależny system PSIwms lub moduł WMS jako część rozbudowanego systemu ERP. W magazynach przyprodukcyjnych zastosowanie znajduje czasem także ten drugi. Taki moduł jest bezpośrednio sprzężony z produkcją, obsługuje produkcję zgodnie z filozofią Just-in-time czy Just-in-sequence – czyli nie tylko na czas, ale i w odpowiedniej kolejności. Dlaczego to tak ważne? - Odpowiednio dobrany system magazynowy zapewnia wsparcie zarówno prostego magazynu przyprodukcyjnego jak i zaawansowanego, całkowicie niezależnego od realizowanej produkcji obiektu dystrybucyjnego. – wyjaśnia Piotr Kulesz.
Michał Klecha
***
Uszczelnianie magazynu
Jednym z głównych celów wdrażania odchudzonej produkcji jest zapewnienie terminowej i adekwatnej ilościowo produkcji oraz zakupu surowców, który pozwoli zrealizować plany produkcyjne bez opóźnień. Z tej perspektywy wszelkie nadwyżki, niedobory, czy opóźnienia (a także wyprzedzenia) w procesie należy traktować jako straty. Warto zdawać sobie sprawę, że skutecznego planowania produkcji absolutnie nie da się przeprowadzić bez precyzyjnej informacji o stanach magazynowych zarówno produktów jak i surowców. Bez bieżącej i precyzyjnej informacji o stanach wyrobów nie uda się skutecznie zaplanować produkcji, bez informacji o stanach materiałów, nie uda się zaplanować zakupów, a co za tym idzie – zrealizować planów produkcyjnych. Z tej perspektywy jednym z najważniejszych (często także pierwszych) kroków podczas wdrażania odchudzonej produkcji jest właśnie uszczelnienie gospodarki magazynowej metodami organizacyjnymi i technologicznymi.
Dariusz Kuśmierek
Dyrektor Działu Produkcji Systemów ERP
Asseco Business Solutions S.A.
***
WMS wpisany w Lean
Odchudzona produkcja to m.in. redukcja poziomu zapasów i odpowiednia gospodarka magazynowa, zatem system WMS doskonale wspiera koncepcję Lean Management. Kluczową funkcją magazynu może stać się na przykład obsługa dostaw typu cross-dock (PSIwms by-pass) łączący dostawy półproduktów bezpośrednio z produkcją. Oczywiście nie eliminuje to zapasu bezpieczeństwa, stanowiącego naturalne i wciąż pożądane zaplecze na wypadek sytuacji i zdarzeń niedających się przewidzieć. Magazyn przyprodukcyjny może pełnić rolę punktu konsolidacyjnego czy montażowego – możemy w nim łączyć elementy od różnych dostawców w „zestawy” i już jako całą „paczkę” dostarczać na linię produkcyjną. Taka konsolidacja zmniejsza ilość dostaw realizowanych na linię produkcyjną, stanowi zatem naturalny krok w stronę usprawniania transportu wewnętrznego… wpisując się w filozofię Lean.
Piotr Kulesz
Sales Manager
PSI Polska Sp. z o.o.