Wózki systemowe to bodaj najbardziej skomplikowane urządzenia wykorzystywane w obiektach magazynowych do pracy w wąskich korytarzach. Ze względu na gabaryty i specyfikę, do ich prowadzenia wykorzystuje się wbudowaną w posadzkę pętlę indukcyjną. W związku z tym zachodzą określone wymagania w odniesieniu do specyfikacji obiektów. Warto również wziąć pod uwagę kwestię systemów bezpieczeństwa współpracujących z wózkami systemowymi.
Posadzka nie byle jaka
Wymagania dotyczące typu i jakości posadzki dla wózków systemowych precyzują europejskie normy, a inwestorzy rozważający zastosowanie takiego właśnie wózka (VNA) powinni zapoznać się z wytycznymi „VDMA” dotyczącymi posadzek przemysłowych. – W branży wózków widłowych zazwyczaj posługujemy się normami TR34 lub DIN 18185, określającymi parametry posadzki, szczególnie w kwestii równości. Niezwykle istotne w przypadku wózków prowadzonych pętlą indukcyjną jest, by odległość pomiędzy przewodem generującym pole magnetyczne a metalowym zbrojeniem posadzki nie była mniejsza niż 50 mm – mówi Tomasz Łukaszek, Menedżer Produktu w firmie Emtor.
Eksperci zaznaczają, iż poza standardowymi wymogami dotyczącymi posadzki dla wózków pracujących w wąskich korytarzach (nośność, równość, chropowatość) istotnym elementem jest rodzaj zbrojenia. Jak podaje Rafał Pańczyk, Dyrektor Działu Intralogistyki w firmie STILL Polska, w przypadku wariantu rozproszonego dopuszcza się do 20 kg zbrojenia na metr sześcienny. W przypadku rozwiązania tradycyjnego, pręty nie mogą znajdować się bliżej niż 50 mm od pętli indukcyjnej. – Należy również uwzględnić osłabienie posadzki wynikające z nacięcia betonu, które jest niezbędne do ułożenia pętli indukcyjnej. Negatywne oddziaływanie na funkcjonowanie pętli indukcyjnej mogą mieć również takie elementy, jak okucia dylatacji, rury i przewody umieszczone w posadzce w bezpośredniej bliskości pętli – przestrzega Rafał Pańczyk.
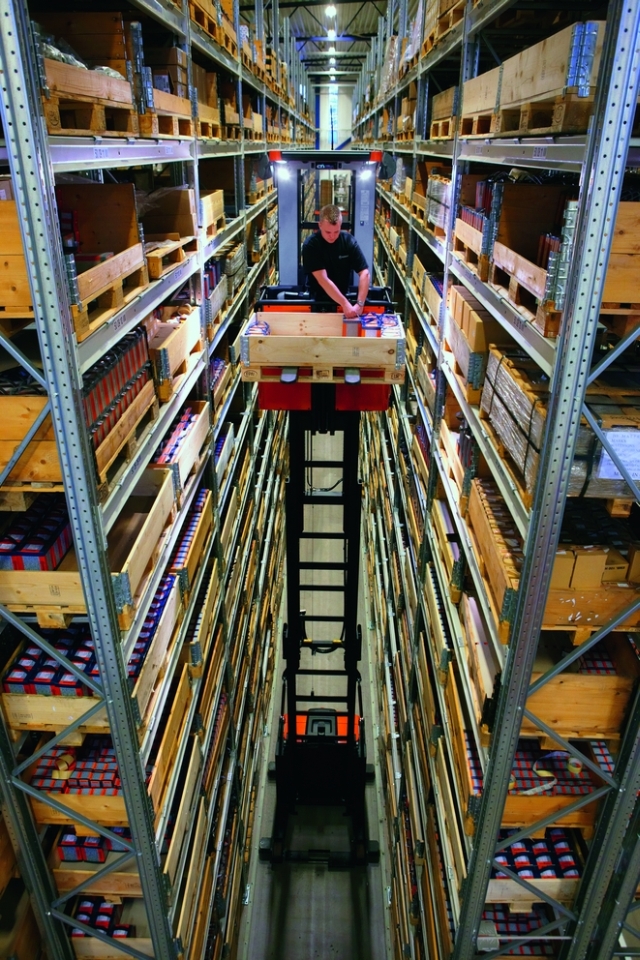
Konfiguracja korytarzy
Jak widać, zastosowanie wózków systemowych pracujących w oparciu o pętlę indukcyjną jest projektem o wysokim poziomie skomplikowania. Idealnie, jeśli to rozwiązanie zostanie wybrane i zaprojektowane od początku dla nowo powstającego magazynu. Ale co w sytuacji, gdy chcemy zwiększyć efektywność powierzchni składowania w istniejącym już obiekcie poprzez zastosowanie takich właśnie maszyn? Jakie będzie to miało reperkusje w odniesieniu do konfiguracji dotychczasowych korytarzy roboczych?
Instalacja wózków systemowych wąskokanałowych w swoim zamierzeniu ma za zadanie zwiększenie wykorzystania kubatury posiadanego lub budowanego magazynu. – Jeżeli klient posiada już magazyn i chciałby takie wózki zastosować, powinien przede wszystkim sprawdzić równość posadzki. – sugeruje Rafał Pawełko, Menedżer Logistyk w firmie WDX SA. Następnie następuje dobór wózka do potrzebnej aplikacji (trzeba pamiętać iż każdy wózek systemowy jest „szyty na miarę”). - Kolejnym etapem jest przestawienie regałów pod zaprojektowany korytarz i ostatnim etapem jest montaż pętli oraz uruchomienie wózka. W zależności od konfiguracji magazynu możliwe jest zwiększenie pojemności od 30 nawet do 70 proc. – mówi Rafał Pawełko.
Instalacja pętli indukcyjnej w istniejących już magazynach jest zazwyczaj możliwa, pod warunkiem spełnienia wymagań dotyczących równości posadzki dla wózków systemowych oraz struktury zbrojenia posadzki. Tomasz Łukaszek z Emtoru zwraca uwagę na istotny fakt, iż wózki VNA prowadzone ścieżką magnetyczną wymagają większej tolerancji bocznej pomiędzy zewnętrznymi krawędziami wózka a paletą na posadzce, zatem większego korytarza roboczego w stosunku do wózków VNA prowadzonych szyną. – Wielkość ta jest różna i może wynosić nawet 100 mm w zależności od wysokości podnoszenia wózka – twierdzi nasz rozmówca.
Gwarancja bezpieczeństwa?
Sterowanie wózkiem za pomocą pętli indukcyjnej stanowi niewątpliwie wsparcie czynnika ludzkiego w zakresie jego bezpiecznej obsługi. Wózki VNA pracujące w pętli indukcyjnej służą przede wszystkim do bezpiecznej obsługi regałów, załadunku, wyładunku, jak i kompletacji, które odbywają się na wszystkich poziomach składowania. Poprzez podnoszoną kabinę operator może bezpiecznie wykonywać operacje magazynowe, widząc paletę tuż przed sobą.
Należy jednak pamiętać, że w obszarze bezpieczeństwa pracy w magazynie ostrożności nigdy za wiele. Praca wózka systemowego w korytarzu z pętlą indukcyjną nie zwalnia bowiem operatora z konieczności obserwacji korytarza roboczego. – Przepisy określają, że w momencie pracy wózka w wąskim kanale nie może tam pracować inna osoba. Dodatkowo można zastosować głowice skanujące, monitorujące przestrzeń przed i za wózkiem. Pozwala to na zatrzymanie wózka w momencie natrafienia na przeszkodę w postaci osób lub rzeczy znajdujących się w torze jazdy wózka – mówi Rafał Pawełko z WDX.
Zastosowanie pętli indukcyjnej dla wózków do wąskich korytarzy oznacza, że wewnątrz korytarza roboczego nie ma żadnej „mechanicznej” bariery pomiędzy wózkiem a instalacją regałową. W opinii Tomasza Łukaszka, istnieje więc ryzyko „wypadnięcia wózka” z toru jazdy, dlatego prawdopodobieństwo takiego zdarzenia producenci wózków systemowych obniżają poprzez: zwiększenie tolerancji bocznej, zmniejszenie maksymalnej prędkości wózka i systemy automatycznego awaryjnego hamowania, w przypadku gdy wózek „zgubi ścieżkę”. – Na rynku są dostępne jednak wózki mogące przy ścieżce magnetycznej osiągać maksymalne prędkości jazdy do 12 km/h i zachowujące dzięki temu najwyższą wydajność – są to np. wózki Yale z serii MTC, wykorzystujące aż 6 czujników do prowadzenia wózka w korytarzu roboczym – mówi ekspert Emtoru.
Co do zasady, zastosowanie pętli indukcyjnej gwarantuje bezkolizyjną jazdę w korytarzu roboczym, zapewniając odpowiednią odległość wózka od regałów. Producenci wózków oferują jednak dodatkowe systemy bezpieczeństwa minimalizujące ryzyko. Zwiększenie bezpieczeństwa obsługi możliwe jest dzięki takim systemom, jak STILL OPTISAFE. Jego podstawową funkcję stanowi wywoływanie w wyznaczonych strefach automatycznej reakcji określonego typu, np.: dynamiczne wyhamowanie na końcu korytarza, blokada obrotu synchronicznego, ograniczenie wysokości podnoszenia czy asystowanie przy wyjeździe z alejki.
Przykłady z rynku
Najpopularniejszym rozwiązaniem firmy STILL do pracy w pętli indukcyjnej jest wózek MX-X. Jego wyróżnikiem jest modułowa konstrukcja, dająca niezwykłą elastyczność i pozwalająca dostosować pojazd do specyficznych warunków magazynu. Maksymalna wysokość podnoszenia na poziomie ponad 15 000 mm z udźwigiem nominalnym 1500 kg, pozwala na efektywną i precyzyjną pracę w magazynach wysokiego podnoszenia. – Model jest atrakcyjny również z punktu widzenia kosztów eksploatacji. MX-X pozwala na ograniczenie nakładów związanych z usługami serwisowymi dzięki bezawaryjności i długim okresom międzyprzeglądowym.
Instalowany w standardzie system Blue-Q pozwala na dalsze oszczędności, wynikające z odłączania niewykorzystywanych w danym momencie układów – mówi Rafał Pańczyk. Dostępne są także liczne usprawnienia i elektroniczne systemy wspomagania operatora: STILL OPTISPEED 3.3 i 4.0 oraz STILL OPTISAFE. OPTISPEED 3.3 umożliwia identyfikację ładunku i jego wagi oraz optymalizację prędkości jazdy w zależności od wysokości podnoszenia. Dodatkowo, alarmuje i zabezpiecza przed przeciążeniem wózka. System OPTISPEED 4.0, czyli tzw. „nawigacja magazynowa”, to układ półautomatycznego sterowania dojazdem do lokalizacji wskazanej przez system WMS. Korzyści z jego zastosowania to: wyeliminowanie pomyłek, większa wydajność, niższe zużycie energii i większy komfort pracy operatora.
Crown TSP 6500 to z kolei wózek z podnoszoną kabiną operatora dostępny w udźwigu 1,0; 1,25 i 1,5 t. Wyposażony w potężny silnik prądu przemiennego o napięciu 48 V zapewnia wyższą wydajność w zastosowaniach wymagających wysokiej prędkości przemieszczania towaru. Przy swoich osiągach TSP 6500 jest przy tym wyjątkowo ekonomiczny i gwarantuje bardzo niskie koszty eksploatacji. – Wydajność energetyczna jest zapewniana poprzez regeneracyjne obniżanie platformy oraz system kompensacji, który wychwytuje utraconą energię i zwraca ją do akumulatora. Przekłada się to na dłuższy czas pracy na jednym ładowaniu, rzadsze wymiany akumulatorów, a tym samym niższe koszty – wyjaśnia Rafał Pawełko z WDX. Opatentowany przez firmę Crown maszt MonoLift umożliwia przemieszczanie towaru na wysokość 13,5 m, zapewniając przy tym niespotykaną wśród innych wózków stabilność. Na konstrukcję zamkniętą masztu MonoLift składają się ciężkie stalowe belki dwuteowe połączone ze sobą za pomocą masywnych poprzecznic, dzięki czemu skręcanie i kołysanie zostaje zredukowane do minimum. Zapewnia to elastyczność składowania, bowiem nie ma już ograniczeń związanych z umieszczaniem cięższych ładunków na większych wysokościach. – TSP 6500 wyróżnia się także doskonałą ergonomią pracy oraz płynnym i komfortowym sterowaniem. Innowacyjny dyszel sterujący można obsługiwać za pomocą palca lub przy użyciu otwieranej gałki sterującej – dodaje Rafał Pawełko.
Flagowym modelem w gamie systemowych wózków Yale jest z kolei model MTC15SWB, łączący w sobie kompaktowe wymiary z dużymi udźwigami rezydualnymi i najwyższą wydajnością. Stabilne dwupunktowe mocowanie masztu oraz głowicy obrotowej gwarantuje duże bezpieczeństwo ładunku, specjalna konstrukcja kabiny i masztu pomocniczego zapewnia najlepszy dostęp do palety w tej klasie wózków. – Na dużą uwagę zasługuje fakt, że konstrukcja głowicy obrotowej zapewnia pobieranie palety 1200 x 1200 mm, czego w standardzie nie oferują inne wózki z tego segmentu – zauważa Tomasz Łukaszek z Emtoru. Opatentowany system hydrauliczny MTC firmy Yale umożliwia dostęp do wszystkich funkcji hydraulicznych jednocześnie, w połączeniu z lepszym zarządzaniem energią. Wózek posiada dwa niezależne silniki z pompami hydraulicznymi, które w zależności od obciążenia wspomagają się wzajemnie. Pompy są dwukierunkowe i pozwalają na odzysk energii w trakcie opuszczania kabiny. Integralnym wyposażeniem wózków z serii MTC jest opatentowany pantograf wideł, regulowany elektronicznie. – Umożliwia on pracę wózków w najwęższych korytarzach, z optymalnymi prześwitami bocznymi. Zastosowanie pantografu ułatwia także pobieranie ładunku z „pola odkładczego” znajdującego się na końcach instalacji regałowej – mówi Tomasz Łukaszek. Stabilność kabiny wózka Yale MTC gwarantuje specjalna konstrukcja masztu z oktagonalnymi stężeniami sekcji. Dzięki takiemu rozwiązaniu maszt jest bardzo stabilny i nie potrzebuje wzmocnień dodatkowych w postaci skośnych usztywnień przymocowanych do tylnej części ramy wózka. Opatentowany przez Yale maszt typu Quadform zapewnia bezpieczeństwo pracy wózkiem i stabilność ładunku przy wysokościach podnoszenia przekraczających nawet 16 m.
Michał Klecha