Dobierając wózek widłowy do konkretnego zastosowania, warto wziąć pod uwagę nie tylko jego charakterystykę techniczną, ale także szereg innych elementów mogących mieć wpływ na efektywność i funkcjonalność, np. sposób wymiany baterii. Minimalizowanie przestojów, ograniczenie czasu, w którym maszyny pozostają bezproduktywne – to dla posiadaczy widlaków kwestie o pierwszorzędnym znaczeniu. A owe przestoje mogą wynikać właśnie z nieodpowiedniego obchodzenia się z bateriami trakcyjnymi.
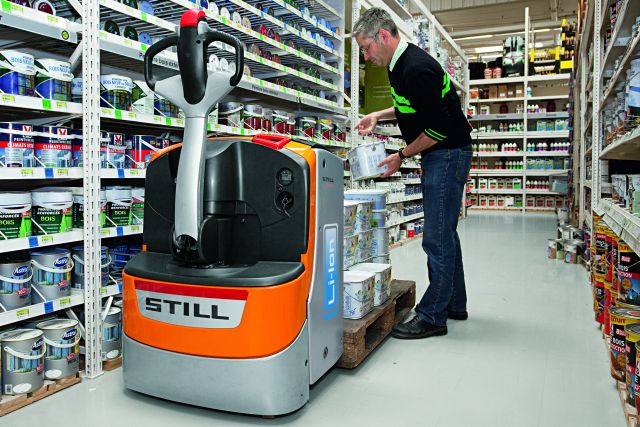
Typowa bateria trakcyjna do niewielkiego wózka widłowego waży nawet ok. tony, do maszyn większych nawet 1,5–2 t. Wymaga ładowania co najmniej raz dziennie, a nawet częściej, gdy mamy do czynienia z pracą w trybie zmianowym. Sam proces, chociażby z racji wagi baterii, może być niebezpieczny i czasochłonny, jeśli chcielibyśmy wykonywać go bez użycia specjalistycznego sprzętu. Uszkodzenie baterii, zagrożenie dla zdrowia pracowników, wyciek niebezpiecznych substancji (elektrolit zawiera kwas siarkowy), uszkodzenie podłogi w magazynie – to tylko niektóre z zagrożeń. Dostawcy urządzeń do wymiany baterii podkreślają, że praktycznie każde z nich jest szyte na miarę potrzeb konkretnego użytkownika, przy doborze urządzenia nie obejdzie się więc bez doradztwa firmy profesjonalnie zajmującej się tymi zagadnieniami.
Na rynku są zarówno ręczne, jak i automatyczne systemy do wymiany baterii trakcyjnych. Od doboru odpowiedniego rozwiązania zależy nie tylko płynność pracy i skrócenie czasu przestojów, ale także bezpieczeństwo. Wszystko przekłada się na koszty bieżącej działalności. Specjaliści zwracają uwagę na to, że zakup systemu wymiany baterii jest inwestycją, tego typu rozwiązania kupujemy raz na wiele lat. Jest to pierwszy istotny czynnik, który przekonuje o wadze właściwego doboru. Kolejnym jest redukcja czasu niezbędnego na wymianę baterii, im lepiej dopasowany system wymiany do potrzeb konkretnego użytkownika, tym większa oszczędność nakładów pracy. Przy zakupie systemu wymiany baterii należy również wziąć pod uwagę to, jak dużą flotą wózków dysponujemy oraz to, jakie wózki planujemy kupić w przyszłości.
Na rynku pojawiają się nowości, np. w ubiegłym roku firma Bater nawiązała współpracę z Sackett Systems, zajmującą się projektowaniem i produkcją systemów wymiany i obsługi baterii. Amerykański producent oferuje rozwiązania do półautomatycznej oraz w pełni automatycznej wymiany baterii, mające m.in. zwiększyć bezpieczeństwo pracowników i operacji wymiany baterii, wydajność operatorów i zapewnić oszczędności na robociźnie. Oferuje też możliwość korzystania z kalkulatora ROI, pozwalającego policzyć dokładny zwrot z inwestycji.
Zazwyczaj posiadacz pojazdu dysponuje drugą (zapasową) baterią, a wymiana dokonywana jest za pomocą dźwigu, drugiego wózka elektrycznego wraz z zawiesiem lub przy zastosowaniu manualnych, bądź też w pełni automatycznych, specjalistycznych urządzeń. – Optymalne wykorzystanie przestrzeni, indywidualne potrzeby klienta i bezpieczeństwo użytkowników, zgodność instalacji z wymogami polskiego prawa – stanowią priorytet na każdym etapie projektu związanego z systemem wymiany baterii – przekonują w HOPPECKE Polska. Specjaliści tej firmy zalecają, jako najbezpieczniejszą, rolkową, boczną wymianę. Ponieważ starsze typy wózków mogą być wyposażone jedynie w wymianę górną, należy wówczas ograniczyć taką wymianę do minimum, jeśli chodzi o drogę przemieszczania podwieszonego ciężaru. Baterię po wyciągnięciu z wózka za pomocą wciągnika, zawiesia, suwnicy należy umieścić na przygotowanym łożu rolkowym. Dalsze operacje wymiany będą przebiegały przy dużo niższym potencjalnym ryzyku wypadku operatora.
O tym, jak ważna jest rola systemów wymiany, podkreślają też w VBR Polska, zaznaczając, że systemy wymiany w wózkach są tak różne, jak różne są same wózki. Generalnie, problem narasta wraz z ciężarem baterii. Im bateria cięższa, tym wymiana jest bardziej kłopotliwa, operator ma ograniczone możliwości fizyczne w zakresie wymian ciężkich baterii. – Klienta najczęściej interesuje, by taka wymiana przechodziła szybko i sprawnie i by ładująca się bateria zajmowała jak najmniej miejsca. Z reguły przy wymianie rolkowej bocznej na jedno pole baterii naładowanej trzeba przewidzieć jedno pole puste, czyli średnio ok. 1 m. Wyobraźmy sobie sytuację, kiedy klient dysponuje setką wózków. Jeśli producent wózków zastosuje jakieś medium do wymiany, baterie mogą stać jedna obok drugiej – to powierzchnia maleje o połowę – usłyszeliśmy w VBR.
Oferujący rozwiązania służące wymianie baterii nie pozostawiają wątpliwości: na wybór optymalnego rozwiązania ma wpływ nie jeden, a wiele czynników. Wśród najważniejszych z nich wymienić należy: koszt, wielkość i wysokość pomieszczenia, efektywność/produktywność. Wysokość od podłoża do sufitu determinuje użycie konkretnych rozwiązań, w zależności od ilości poziomów składowania baterii: w systemie jednopoziomowym wynosi 3,6 m, w dwupoziomowym 4,8 m, trzypoziomowym – 6 m. Przy każdym kolejnym poziomie wymagana wysokość rośnie o kolejne 1,2 m (przyjmuje się, że podniesienie systemu o jeden poziom daje oszczędności powierzchni podłogi o ok. 17 proc.). Parametr ten jest szczególnie ważny dla firm, które wykorzystują magazyny wysokiego składowania. Na produktywność ma wpływ również czas oczekiwania na wymianę baterii. – Zwiększając wysokość składowania baterii, tracimy część czasu zaoszczędzonego na zastosowaniu systemu wymiany, ponieważ maszyna zachowuje się podobnie jak wózek widłowy, który szybciej przemieszcza towary do przodu niż podnosi do góry. Należy zwrócić uwagę, że często w dokumentacji takich systemów można znaleźć informację o ograniczaniu prędkości przy różnych wysokościach unoszenia. Kolejnym ważnym argumentem, który należy brać pod uwagę, jest to, że z bardzo wysokiego miejsca może być trudno podjąć baterię za pomocą zastępczego sprzętu w momencie wykonywania przeglądu czy naprawy maszyny. Aby to zilustrować, posłużymy się przykładem. Załóżmy, że posiadamy 200 baterii. Wówczas w zależności od wybranego systemu na najniższym poziomie w przypadku awarii będziemy mieli zmagazynowaną następującą ilość baterii: system jednopoziomowy – 200 sztuk; dwupoziomowy 100 sztuk; trzypoziomowy 67 sztuk; czteropoziomowy 50 sztuk; pięciopoziomowy 40 sztuk oraz sześciopoziomowy 34 sztuki. Zwracając uwagę, że średnio przez cały czas 50 proc. baterii jest w trakcie ładowania, zauważamy, że niewiele dużych flot będzie mogło pracować przez dłuższy czas z tak małą ilością baterii dostępną w trybie awaryjnym. Dlatego bazując na tym i na odpowiednio krótkim czasie wymiany baterii można dobrać skrojony na miarę system w zależności od ilości baterii: 1–49 sztuk zmagazynowanych baterii – system jednopoziomowy; 50–139 sztuk – dwupoziomowy; 140–299 – trzypoziomowy; 300–619 – czteropoziomowy; od 620 sztuk – pięciopoziomowy – wyliczają w BENNING Power Electronics.
Nie każdy użytkownik widlaków potrzebuje dużego systemu wymiany baterii, bo nie wszyscy pracują w systemie trzyzmianowym z pełnym wykorzystaniem dwóch lub trzech baterii. Często wystarczą im zatem mechaniczne środki wymiany. Aby wypełnić wymagania dotyczące BHP, można zastosować np. nakładki na wózki, pozwalające wyjąć baterię z innego wózka praktycznie bez żadnego wysiłku ze strony operatora. To jedno z najtańszych i najprostszych rozwiązań. Przy bateriach małych (do 250–300 kg) można zastosować rozwiązanie z trolleyem, czyli wózkiem, który porusza się wzdłuż regałów bateryjnych i pozwala umieszczać na nich baterie podejmowane wcześniej z wózka (rozwiązanie ma możliwość niezależnej regulacji dwóch stołów bateryjnych i jest napędzane ręcznie). Zastosowanie trolleya eliminuje konieczność każdorazowego dojeżdżania wózkiem do regału, aby wypchnąć nań baterię i odjąć kolejną.
Boczna wymiana akumulatora w wózku widłowym, której prekursorem była firma STILL, jest stosowana coraz powszechniej. Nic dziwnego – czynność jest znacznie wygodniejsza i bezpieczniejsza niż tradycyjna metoda z dźwigiem. Sami producenci wózków mają dla swych klientów własną ofertę. Przykładem może być wykorzystywany w pracy wielozmianowej wózek Toyota Traigo 48. Oferowane są w nim dwie opcje bocznej wymiany baterii. Kieszenie na widły pod baterią pozwalają na jej szybką wymianę za pomocą wózka widłowego, natomiast alternatywą dla tego rozwiązania jest umieszczenie baterii na łożu rolkowym. Konstruktorzy STILL-a podkreślają też proekologiczny walor bocznego sposobu wymiany. Dopuszczalne jest ładowanie baterii w wózku. Nie występuje wtedy niebezpieczne gromadzenie wodoru, ponieważ istnieje dostateczna wentylacja przedziału baterii.
– Najprostszym systemem wymiany baterii są nakładki na wózek widłowy. Możemy rozróżnić je na manualne nakładki do wózków paletowych i magnetyczne z napędem elektrycznym. Zaletą nakładek jest ich uniwersalność, oszczędność przestrzeni oraz niższy koszt zakupu. Jeżeli flota elektrycznych wózków widłowych jest mniejsza niż 10, to manualne nakładki na wózek paletowy idealnie spełniają potrzeby. Kolejną metodę stanowią samodzielne urządzenia do wymiany baterii. Ich konstrukcję oparto na systemie magnetycznym, który pozwala bardzo łatwo wyjąć baterię z wózka. Jest to wydajny, szybki i efektywny rodzaj wymiany baterii, szczególnie korzystny, gdy użytkownik nie dysponuje zbyt dużą przestrzenią w akumulatorowni lub w sytuacjach awaryjnych oraz dla każdego z przedsiębiorców, którego flota liczy powyżej 10 pojazdów – usłyszeliśmy w firmie LINK. Warto dodać, że istnieje też sporo systemów wymiany baterii skonstruowanych na potrzeby akumulatorowni, umożliwiających wyjęcie baterii z wózka i przeniesienie jej bezpośrednio do stacji ładowania.
HOPPECKE oferuje kilka wariantów systemów manualnej lub automatycznej wymiany baterii. W pełni automatyczny trak Xchange FU to rozwiązanie dla użytkowników eksploatujących dowolną liczbę baterii różnej wielkości z przeznaczeniem do wszystkich typów pojazdów elektrycznych. Na życzenie system wymiany trak Xchange FU wykonywany jest z regałem nawet o sześciu poziomach składowania baterii. Takie rozwiązanie oszczędza powierzchnię stacji ładowania, wszystkie baterie można wówczas ustawić wielopoziomowo. Elementami wyposażenia są: innowacyjny system laserowego pozycjonowania oraz łatwy w obsłudze dżojstik, zapewniające precyzyjne ustawienie urządzenia i pobranie odpowiedniej baterii trakcyjnej. Pozwala to na oszczędność czasu i uniknięcie błędów, jakie mogą wystąpić w przypadku ręcznej obsługi wymiany, a które mogłyby doprowadzić do uszkodzenia baterii lub wypadku operatora. Liczba eksploatowanych baterii jest praktycznie dowolna, czas wymiany baterii wynosi ok. 3 min. Rozwiązanie adresowane jest dla posiadaczy pojazdów elektrycznych z wymianą boczną oraz z wymianą górną. W ofercie HOPPECKE jest też m.in. automatyczna nakładka na wózek paletowy do bocznej wymiany baterii za pomocą elektromagnesu/przyssawki – trak Xchange PU, jak również półautomatyczna nakładka na wózek paletowy do manualnej bocznej wymiany baterii – trak Xchange MU oraz mechaniczny wózek szynowy do manualnej bocznej wymiany baterii typu trolley – trak Xchange TU. Jest to rozwiązanie dla baterii o napięciu 12 i 24 V, zaprojektowane specjalnie dla elektrycznych wózków paletowych i wózków do komisjonowania poziomego z możliwą boczną wymianą baterii przy użyciu łoża rolkowego. Podwójne łoże rolkowe urządzenia umożliwia szybką wymianę baterii (cykl wynosi 2 min), a blokada gwarantuje jej bezpieczny transport. Wysokość i kąt nachylenia systemu można dowolnie regulować.
BENNING Power Electronics wprowadził kilka lat temu do swojej oferty produkty największego na świecie dostawcy systemów wymiany baterii, firmy BHS. Gama obejmuje m.in. platformowe systemy wymiany baterii EBE-XX. Średni czas wymiany baterii (wymiana boczna) wynosi 2–3 min. System mieści do czterech poziomów baterii na regałach. Ustawienie regałów bateryjnych jest jedno- lub dwustronne. Do wyjęcia baterii używany jest elektromagnes lub przyssawka. Prostowniki montowane są na szczycie lub na tylnej ścianie regałów lub w szafach systemowych system monitoringu i nadzoru akumulatorowni. Zdublowany układ jezdny pozwala kontynuować operacje nawet przy uszkodzonym jednym silniku jazdy, co zwiększa efektywność i dostępność maszyny.
Adam Brzozowski
Na rynku pojawiają się nowości, np. w ubiegłym roku firma Bater nawiązała współpracę z Sackett Systems, zajmującą się projektowaniem i produkcją systemów wymiany i obsługi baterii. Amerykański producent oferuje rozwiązania do półautomatycznej oraz w pełni automatycznej wymiany baterii, mające m.in. zwiększyć bezpieczeństwo pracowników i operacji wymiany baterii, wydajność operatorów i zapewnić oszczędności na robociźnie. Oferuje też możliwość korzystania z kalkulatora ROI, pozwalającego policzyć dokładny zwrot z inwestycji.
Nie zapomnieć o szczegółach
Zazwyczaj posiadacz pojazdu dysponuje drugą (zapasową) baterią, a wymiana dokonywana jest za pomocą dźwigu, drugiego wózka elektrycznego wraz z zawiesiem lub przy zastosowaniu manualnych, bądź też w pełni automatycznych, specjalistycznych urządzeń. – Optymalne wykorzystanie przestrzeni, indywidualne potrzeby klienta i bezpieczeństwo użytkowników, zgodność instalacji z wymogami polskiego prawa – stanowią priorytet na każdym etapie projektu związanego z systemem wymiany baterii – przekonują w HOPPECKE Polska. Specjaliści tej firmy zalecają, jako najbezpieczniejszą, rolkową, boczną wymianę. Ponieważ starsze typy wózków mogą być wyposażone jedynie w wymianę górną, należy wówczas ograniczyć taką wymianę do minimum, jeśli chodzi o drogę przemieszczania podwieszonego ciężaru. Baterię po wyciągnięciu z wózka za pomocą wciągnika, zawiesia, suwnicy należy umieścić na przygotowanym łożu rolkowym. Dalsze operacje wymiany będą przebiegały przy dużo niższym potencjalnym ryzyku wypadku operatora.
Ręczny czy automatyczny systemy do wymiany baterii trakcyjnych? Od doboru odpowiedniego rozwiązania zależy nie tylko płynność pracy i skrócenie czasu przestojów, ale także bezpieczeństwo. Wszystko przekłada się na koszty bieżącej działalności. Specjaliści zwracają uwagę na to, że zakup systemu wymiany baterii jest inwestycją, tego typu rozwiązania kupujemy raz na wiele lat.
O tym, jak ważna jest rola systemów wymiany, podkreślają też w VBR Polska, zaznaczając, że systemy wymiany w wózkach są tak różne, jak różne są same wózki. Generalnie, problem narasta wraz z ciężarem baterii. Im bateria cięższa, tym wymiana jest bardziej kłopotliwa, operator ma ograniczone możliwości fizyczne w zakresie wymian ciężkich baterii. – Klienta najczęściej interesuje, by taka wymiana przechodziła szybko i sprawnie i by ładująca się bateria zajmowała jak najmniej miejsca. Z reguły przy wymianie rolkowej bocznej na jedno pole baterii naładowanej trzeba przewidzieć jedno pole puste, czyli średnio ok. 1 m. Wyobraźmy sobie sytuację, kiedy klient dysponuje setką wózków. Jeśli producent wózków zastosuje jakieś medium do wymiany, baterie mogą stać jedna obok drugiej – to powierzchnia maleje o połowę – usłyszeliśmy w VBR.
Oferujący rozwiązania służące wymianie baterii nie pozostawiają wątpliwości: na wybór optymalnego rozwiązania ma wpływ nie jeden, a wiele czynników. Wśród najważniejszych z nich wymienić należy: koszt, wielkość i wysokość pomieszczenia, efektywność/produktywność. Wysokość od podłoża do sufitu determinuje użycie konkretnych rozwiązań, w zależności od ilości poziomów składowania baterii: w systemie jednopoziomowym wynosi 3,6 m, w dwupoziomowym 4,8 m, trzypoziomowym – 6 m. Przy każdym kolejnym poziomie wymagana wysokość rośnie o kolejne 1,2 m (przyjmuje się, że podniesienie systemu o jeden poziom daje oszczędności powierzchni podłogi o ok. 17 proc.). Parametr ten jest szczególnie ważny dla firm, które wykorzystują magazyny wysokiego składowania. Na produktywność ma wpływ również czas oczekiwania na wymianę baterii. – Zwiększając wysokość składowania baterii, tracimy część czasu zaoszczędzonego na zastosowaniu systemu wymiany, ponieważ maszyna zachowuje się podobnie jak wózek widłowy, który szybciej przemieszcza towary do przodu niż podnosi do góry. Należy zwrócić uwagę, że często w dokumentacji takich systemów można znaleźć informację o ograniczaniu prędkości przy różnych wysokościach unoszenia. Kolejnym ważnym argumentem, który należy brać pod uwagę, jest to, że z bardzo wysokiego miejsca może być trudno podjąć baterię za pomocą zastępczego sprzętu w momencie wykonywania przeglądu czy naprawy maszyny. Aby to zilustrować, posłużymy się przykładem. Załóżmy, że posiadamy 200 baterii. Wówczas w zależności od wybranego systemu na najniższym poziomie w przypadku awarii będziemy mieli zmagazynowaną następującą ilość baterii: system jednopoziomowy – 200 sztuk; dwupoziomowy 100 sztuk; trzypoziomowy 67 sztuk; czteropoziomowy 50 sztuk; pięciopoziomowy 40 sztuk oraz sześciopoziomowy 34 sztuki. Zwracając uwagę, że średnio przez cały czas 50 proc. baterii jest w trakcie ładowania, zauważamy, że niewiele dużych flot będzie mogło pracować przez dłuższy czas z tak małą ilością baterii dostępną w trybie awaryjnym. Dlatego bazując na tym i na odpowiednio krótkim czasie wymiany baterii można dobrać skrojony na miarę system w zależności od ilości baterii: 1–49 sztuk zmagazynowanych baterii – system jednopoziomowy; 50–139 sztuk – dwupoziomowy; 140–299 – trzypoziomowy; 300–619 – czteropoziomowy; od 620 sztuk – pięciopoziomowy – wyliczają w BENNING Power Electronics.
Proste i systemowe
Nie każdy użytkownik widlaków potrzebuje dużego systemu wymiany baterii, bo nie wszyscy pracują w systemie trzyzmianowym z pełnym wykorzystaniem dwóch lub trzech baterii. Często wystarczą im zatem mechaniczne środki wymiany. Aby wypełnić wymagania dotyczące BHP, można zastosować np. nakładki na wózki, pozwalające wyjąć baterię z innego wózka praktycznie bez żadnego wysiłku ze strony operatora. To jedno z najtańszych i najprostszych rozwiązań. Przy bateriach małych (do 250–300 kg) można zastosować rozwiązanie z trolleyem, czyli wózkiem, który porusza się wzdłuż regałów bateryjnych i pozwala umieszczać na nich baterie podejmowane wcześniej z wózka (rozwiązanie ma możliwość niezależnej regulacji dwóch stołów bateryjnych i jest napędzane ręcznie). Zastosowanie trolleya eliminuje konieczność każdorazowego dojeżdżania wózkiem do regału, aby wypchnąć nań baterię i odjąć kolejną.
Nie każdy użytkownik widlaków potrzebuje dużego systemu wymiany baterii, bo nie wszyscy pracują w systemie trzyzmianowym z pełnym wykorzystaniem dwóch lub trzech baterii. Często wystarczą im zatem mechaniczne środki wymiany.
Boczna wymiana akumulatora w wózku widłowym, której prekursorem była firma STILL, jest stosowana coraz powszechniej. Nic dziwnego – czynność jest znacznie wygodniejsza i bezpieczniejsza niż tradycyjna metoda z dźwigiem. Sami producenci wózków mają dla swych klientów własną ofertę. Przykładem może być wykorzystywany w pracy wielozmianowej wózek Toyota Traigo 48. Oferowane są w nim dwie opcje bocznej wymiany baterii. Kieszenie na widły pod baterią pozwalają na jej szybką wymianę za pomocą wózka widłowego, natomiast alternatywą dla tego rozwiązania jest umieszczenie baterii na łożu rolkowym. Konstruktorzy STILL-a podkreślają też proekologiczny walor bocznego sposobu wymiany. Dopuszczalne jest ładowanie baterii w wózku. Nie występuje wtedy niebezpieczne gromadzenie wodoru, ponieważ istnieje dostateczna wentylacja przedziału baterii.
– Najprostszym systemem wymiany baterii są nakładki na wózek widłowy. Możemy rozróżnić je na manualne nakładki do wózków paletowych i magnetyczne z napędem elektrycznym. Zaletą nakładek jest ich uniwersalność, oszczędność przestrzeni oraz niższy koszt zakupu. Jeżeli flota elektrycznych wózków widłowych jest mniejsza niż 10, to manualne nakładki na wózek paletowy idealnie spełniają potrzeby. Kolejną metodę stanowią samodzielne urządzenia do wymiany baterii. Ich konstrukcję oparto na systemie magnetycznym, który pozwala bardzo łatwo wyjąć baterię z wózka. Jest to wydajny, szybki i efektywny rodzaj wymiany baterii, szczególnie korzystny, gdy użytkownik nie dysponuje zbyt dużą przestrzenią w akumulatorowni lub w sytuacjach awaryjnych oraz dla każdego z przedsiębiorców, którego flota liczy powyżej 10 pojazdów – usłyszeliśmy w firmie LINK. Warto dodać, że istnieje też sporo systemów wymiany baterii skonstruowanych na potrzeby akumulatorowni, umożliwiających wyjęcie baterii z wózka i przeniesienie jej bezpośrednio do stacji ładowania.
Boczna wymiana akumulatora w wózku widłowym, której prekursorem była firma STILL, jest stosowana coraz powszechniej. Nic dziwnego – czynność jest znacznie wygodniejsza i bezpieczniejsza niż tradycyjna metoda z dźwigiem.
HOPPECKE oferuje kilka wariantów systemów manualnej lub automatycznej wymiany baterii. W pełni automatyczny trak Xchange FU to rozwiązanie dla użytkowników eksploatujących dowolną liczbę baterii różnej wielkości z przeznaczeniem do wszystkich typów pojazdów elektrycznych. Na życzenie system wymiany trak Xchange FU wykonywany jest z regałem nawet o sześciu poziomach składowania baterii. Takie rozwiązanie oszczędza powierzchnię stacji ładowania, wszystkie baterie można wówczas ustawić wielopoziomowo. Elementami wyposażenia są: innowacyjny system laserowego pozycjonowania oraz łatwy w obsłudze dżojstik, zapewniające precyzyjne ustawienie urządzenia i pobranie odpowiedniej baterii trakcyjnej. Pozwala to na oszczędność czasu i uniknięcie błędów, jakie mogą wystąpić w przypadku ręcznej obsługi wymiany, a które mogłyby doprowadzić do uszkodzenia baterii lub wypadku operatora. Liczba eksploatowanych baterii jest praktycznie dowolna, czas wymiany baterii wynosi ok. 3 min. Rozwiązanie adresowane jest dla posiadaczy pojazdów elektrycznych z wymianą boczną oraz z wymianą górną. W ofercie HOPPECKE jest też m.in. automatyczna nakładka na wózek paletowy do bocznej wymiany baterii za pomocą elektromagnesu/przyssawki – trak Xchange PU, jak również półautomatyczna nakładka na wózek paletowy do manualnej bocznej wymiany baterii – trak Xchange MU oraz mechaniczny wózek szynowy do manualnej bocznej wymiany baterii typu trolley – trak Xchange TU. Jest to rozwiązanie dla baterii o napięciu 12 i 24 V, zaprojektowane specjalnie dla elektrycznych wózków paletowych i wózków do komisjonowania poziomego z możliwą boczną wymianą baterii przy użyciu łoża rolkowego. Podwójne łoże rolkowe urządzenia umożliwia szybką wymianę baterii (cykl wynosi 2 min), a blokada gwarantuje jej bezpieczny transport. Wysokość i kąt nachylenia systemu można dowolnie regulować.
BENNING Power Electronics wprowadził kilka lat temu do swojej oferty produkty największego na świecie dostawcy systemów wymiany baterii, firmy BHS. Gama obejmuje m.in. platformowe systemy wymiany baterii EBE-XX. Średni czas wymiany baterii (wymiana boczna) wynosi 2–3 min. System mieści do czterech poziomów baterii na regałach. Ustawienie regałów bateryjnych jest jedno- lub dwustronne. Do wyjęcia baterii używany jest elektromagnes lub przyssawka. Prostowniki montowane są na szczycie lub na tylnej ścianie regałów lub w szafach systemowych system monitoringu i nadzoru akumulatorowni. Zdublowany układ jezdny pozwala kontynuować operacje nawet przy uszkodzonym jednym silniku jazdy, co zwiększa efektywność i dostępność maszyny.
Adam Brzozowski