Oczekiwania rynkowe względem firm produkcyjnych stale rosną. W pogoni za jak najbardziej konkurencyjną relacją ceny do jakości firmy produkcyjne skupiają się coraz bardziej na optymalizowaniu procesów wewnętrznych. Jednym z takich procesów, który może poprawić wydajność produkcji, przyspieszyć ją i w konsekwencji zaoferować lepszy produkt jest kompletacja komponentów do montażu wyrobu gotowego.
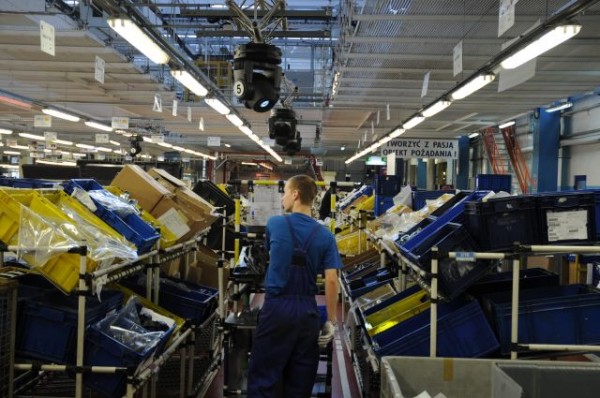
Osiągnięcie takiego stanu przyczyni się niewątpliwie to tego, iż na etapie komisjonowania podzespołów zapanuje „kompletny porządek”.
– Logistyka produkcji w dzisiejszym bardzo dynamicznym otoczeniu biznesowym staje się nie mniej ważna niż logistyka produktu końcowego. Dostawy Just-in-Time stały się wymogiem nie tylko odbiorcy końcowego, ale również dużych przedsiębiorstw produkcyjnych, wymagających najwyższej terminowości od swoich dostawców – mówi Jędrzej Iglewski, Wiceprezes firmy HIT – Kody Kreskowe.
Do najpopularniejszych rozwiązań w obszarze kompletacji na linii produkcyjnej zaliczają się takie metody komisjonowania jak:
- Just-in-Sequence Picking: metoda gwarantująca realizację zamówień bezpośrednio do gniazda produkcyjnego w precyzyjnie zdefiniowanej sekwencji czasowej. Metoda bierze pod uwagę założenia planu produkcji, gwarantując dyspozycyjność właściwych komponentów, we właściwym czasie i we właściwym miejscu;
- Pick-to-Light: metoda kompletacji produkcyjnej wsparta systemem sygnalizacji wizualnej. Operatorzy magazynowi, w oparciu o system komunikacji świetlnej, kompletują drobne komponenty produkcyjne, dysponując pełną swobodą ruchów. Systemy tego typu znajdują wykorzystanie szczególnie w branży automotive;
- kompletacja głosowa: technika kompletacji umożliwiająca realizację zadań przy użyciu głosu jako metody komunikacji z systemem. Metoda cechuje się dużą ergonomią (wygoda operowania, wolne obie ręce, łatwość komunikacji) i łatwością w adaptacji nowych pracowników.
Nie ma jednak reguły, która określałaby w sposób wiążący wyższość jednej metody nad drugą. Wszystko jest kwestią indywidualnych uwarunkowań i charakteru procesu. Może okazać się, że jedno rozwiązanie doskonale sprawdzone w danej firmie, w innej nie będzie już „lekiem na całe zło”.
Od czego zacząć?
Na co należy zwrócić uwagę, żeby tak zdefiniowaną wydajność kompletacji osiągnąć? Podobnie jak w przypadku wielu innych przedsięwzięć, również biznesowych, projektując dowolne rozwiązanie trzeba rozpocząć od szczegółowej analizy. Bez uwzględnienia wszystkich możliwych przypadków trudno zaproponować optymalne rozwiązanie. – Jest kilka sposobów kompletowania na linii produkcyjnej, ale optymalne jest rozwiązanie dedykowane, stworzone specjalnie na potrzeby konkretnego przedsiębiorstwa – radzi Krzysztof Zakrzewski, Product Manager w firmie IBCS Poland. – Należy wziąć pod uwagę przede wszystkim długość serii produkcyjnych. Konieczne jest określenie, czy do wszystkich zamówień wykorzystujemy te same podzespoły, ważne są także gabaryty detali, ich ciężar, odległości między stanowiskami i odległość do magazynu, takt, sposób montażu i konieczność rejestracji numerów seryjnych/partii produkcyjnych poszczególnych detali itd. – wylicza nasz rozmówca. Kompletacja z wykorzystaniem linii może także dotyczyć zbierania zamówionych przez klienta towarów bez ich montażu. W przypadku montażu należy zorganizować stanowisko kompletacji tak, by pracownik nie miał przestojów podyktowanych brakiem detali.
Strefa kompletacji czy też montażu na linii produkcyjnej powinna być nastawiona na maksymalną produktywność przy jednoczesnym zachowaniu warunków, które uniemożliwiają popełnienie błędu. Wojciech Sobczyk, specjalista w dziedzinie logistyki w produkcji dla branży automotive, sugeruje dodać do tego jeszcze ergonomię pracy, gdyż ma to bezpośredni wpływ na aspekty wydajnościowe. – Kierując się tymi wyznacznikami, powinno się planować stanowisko pracy, czyli strefę kompletacji. Zacząć należy od pracownika – organizacja ergonomicznego miejsca pracy minimalizującego działania bez wartości dodanej (NVA). Jeśli w danej strefie będzie pracować więcej osób, to analogicznie muszą być zorganizowane wszystkie stanowiska – mówi Wojciech Sobczyk. W opinii naszego rozmówcy, w dalszej kolejności należy zaplanować najbardziej optymalny (pod względem kosztowym) przepływ materiału do stanowiska pracy. Zaprojektowanie optymalnego i efektywnego layoutu strefy kompletacji wcale nie jest sprawą prostą, jednak jeśli poświęcimy odpowiednią ilość czasu na wypracowanie najlepszego rozwiązania, na pewno znacząco przybliży nas do osiągnięcia celu.
Najczęstsze błędy
W kontekście różnych projektów biznesowych można powiedzieć, że teoria teorią, a życie sobie. Praktyka pokazuje, że nie zawsze wszystko robione jest tak, jak zalecają „złote” wydawałoby się zasady. Jednym z czynników, który wielokrotnie decyduje o niepowodzeniu projektów, okazuje się kwestia mentalna, a dokładniej – niechęć do zmian. Ten problem nie omija z pewnością również obszaru logistyki zakładów przemysłowych, w tym procesów komisjonowania na liniach produkcyjnych.
Zdaniem Krzysztofa Zakrzewskiego z IBCS Poland, największym zidentyfikowanym problemem jest zbytni konserwatyzm w doborze rozwiązań do kompletacji czy w ogóle w podejściu do zmian. – Wiele spółek cały czas stosuje metody dopasowane do potrzeb i wielkości przedsiębiorstw z końca ubiegłego wieku – przyznaje ekspert IBCS. – Proces kompletacji powinien być regularnie przeglądany, a osoba odpowiedzialna powinna orientować się w nowościach rynkowych w tym zakresie. Przedsiębiorstwa walczą ze sobą na wielu frontach i koszty produkcji są niezmiernie ważne – dodaje nasz rozmówca.
Z całą pewnością najgorszym błędem, jaki można popełnić, jest wdrożenie rozwiązania bez uprzedniej dogłębnej analizy problemu. Bez identyfikacji przyczyny źródłowej problemu nawet najbardziej znane, najdroższe i najbardziej zaawansowane technologicznie rozwiązanie może nie przynieść oczekiwanego rezultatu, jakim jest eliminacja problemu. W skrajnych przypadkach może to okazać się całkowicie nietrafioną inwestycją. – Istnieje szereg uniwersalnych metod analizy problemu (5 x Dlaczego, 5W1H, 4M itp.), które możemy zastosować dla większości zagadnień – podpowiada Wojciech Sobczyk. – Są również bardziej zaawansowane narzędzia pozwalające na dokładniejsze zbadanie problemu. Jedne będziemy stosować w przypadku potrzeby zwiększenia wydajności, inne w przypadku błędów ludzkich – dodaje. Identyfikacja problemu (przyczyny źródłowej) oraz wyznaczenie celu nakierowują na wybór odpowiedniego rozwiązania, a następnie jego wdrożenie.
Wojciech Sobczyk przyznaje również, że bardzo często bagatelizuje się istotę tworzenia strefy kompletacji (komisjonowania). – Jest nią, a przynajmniej powinno być, uzyskanie maksymalnej wydajności głównego procesu poprzez przejęcie działań bez wartości dodanej – twierdzi nasz ekspert. – Organizując strefę komisjonowania należy tak ją zaprojektować, aby zarówno proces główny, jak i sama strefa były maksymalnie wydajne. Inaczej mówiąc, należy dążyć do minimalizacji NVA i maksymalizacji VA – dodaje. Tylko wtedy globalny bilans projektu przyniesie ekonomiczne korzyści.
Innym często popełnianym błędem jest zbyt szybki proces wdrażania, niepowiązany z weryfikacją implementacji poszczególnych etapów. Nierzadko skutkuje to dodatkowymi kosztami, a w konsekwencji – wydłużeniem czasu całego wdrożenia rozwiązania.
Michał Klecha