Decydując się na rozwiązanie w postaci magazynu wysokiego składowania z wąskimi korytarzami, w których poruszają się wózki systemowe, tzw. VNA, należy zdawać sobie sprawę z kwestii związanych z zapewnieniem odpowiednich warunków bezpieczeństwa pracy w takim układzie. Ogólne zasady oceny ryzyka stwarzanego przez maszyny podaje Dyrektywa Europejskiej Wspólnoty Gospodarczej dotycząca maszyn 2006/42/WE oraz norma PN-EN ISO 12100:2012 Bezpieczeństwo Maszyn.
Systemowe wózki widłowe poruszające się pomiędzy regałami w wąskich korytarzach magazynów wysokiego składowania stwarzają duże zagrożenie dla osób pieszych potencjalnie mogących się pojawić w tych obszarach pracy wózków. I to z kilku powodów.
Po pierwsze, odstępy pomiędzy wózkiem systemowym VNA a czołem regału. Są one rzędu 10–20 cm i są zbyt małe w stosunku do wymaganych minimalnych odstępów opisanych w normie PN EN 349: Minimalne odstępy zapobiegające zgnieceniu części ciała człowieka. W tym przypadku jest to 50 cm, przyjęte w stosunku do tułowia człowieka.
Po drugie, charakter i warunki pracy operatora wózka VNA w wąskich korytarzach. Dzięki temu, że wózki te są prowadzone automatycznie wzdłuż regałów po linii prostej za pomocą prowadnic indukcyjnych lub mechanicznych, operator wózka może skupić się na wykonaniu operacji związanych z dojazdem na odpowiednią wysokość – nawet do 15 m – do wybranego miejsca paletowego w regale oraz na czynnościach związanych ze składowaniem, odkładaniem, pobieraniem, kompletowaniem ładunków. Tym samym nie jest w stanie w pełni kontrolować wszystkiego tego, co się dzieje przed i za wózkiem.
Po trzecie, cechy konstrukcyjne wózka i sposób jego pracy w bardzo dużym stopniu ograniczają widoczność zarówno przed, jak i za wózkiem, stwarzając zagrożenie dla osób, które mogłyby w tym czasie znaleźć się na trasie jazdy wózka. Przed wózkiem przeszkodę stanowi ładunek na widłach, za wózkiem – elementy kabiny i masztu. Według Rozporządzenia MGPiPS z dnia 21.10.2008 r. w sprawie zasadniczych wymagań dla maszyn i elementów bezpieczeństwa (Dz. U. Nr 199 poz. 1228), wprowadzającego Dyrektywę 2006/42/WE, widoczność ze stanowiska pracy kierowcy powinna być taka, aby mógł on sterować urządzeniem i jego częściami w przewidzianych warunkach użytkowania maszyny, przy zachowaniu całkowitego bezpieczeństwa własnego i osób narażonych, a w razie konieczności należy przewidzieć odpowiednie urządzenia, które zapobiegną niebezpieczeństwom wynikającym ze złej widoczności.
Po czwarte, sposób rozłożenia towarów w magazynie i organizacja wykonywanych tam operacji i procesów logistycznych. Często na dolnych poziomach regałów magazynowych składowane są towary, które pracownik może ręcznie wyjąć i przenieść lub przełożyć na mały wózek, a wykorzystanie w tym przypadku wózka VNA byłoby czasochłonne i nieuzasadnione ekonomicznie. Pracownik taki jest w tym przypadku narażony na kolizję z wózkiem, co stanowi dla niego bardzo duże niebezpieczeństwo.
Podstawowym warunkiem bezpiecznej pracy w wąskich korytarzach magazynów wysokiego składowania jest przestrzeganie zasady, że w obszarach, w których pracują wózki, w tym samym czasie nie powinni znajdować się piesi.
W Polsce, zgodnie z art. 207 Kodeksu pracy, pracodawca zobowiązany jest zapewnić bezpieczne warunki pracy, wykorzystując do tego celu wszystkie możliwe środki, a w szczególności osiągnięcia nauki i techniki.
W magazynach wysokiego składowania pracodawca ma do wyboru systemy ochronne, które można podzielić na trzy grupy:
– zabezpieczenia budowlane (osłony stałe),
– zabezpieczenia techniczne przy wejściach do korytarzy,
– zabezpieczenia techniczne na wózkach.
– zabezpieczenia budowlane (osłony stałe),
– zabezpieczenia techniczne przy wejściach do korytarzy,
– zabezpieczenia techniczne na wózkach.
Systemy magazynowe są tak zaplanowane, że do obszarów, w których pracują wózki wysokiego składowania, nie mają dostępu piesi. Oddzielenie tych obszarów może być zrealizowane poprzez zastosowanie różnego rodzaju środków budowlanych, do których możemy zaliczyć:
– mury,
– przegrody,
– ogrodzenia,
– miejsca przekazywania ładunku.
– mury,
– przegrody,
– ogrodzenia,
– miejsca przekazywania ładunku.
Systemy takie są sztywne i każda zmiana organizacji pracy w magazynie wymaga zmiany systemu.
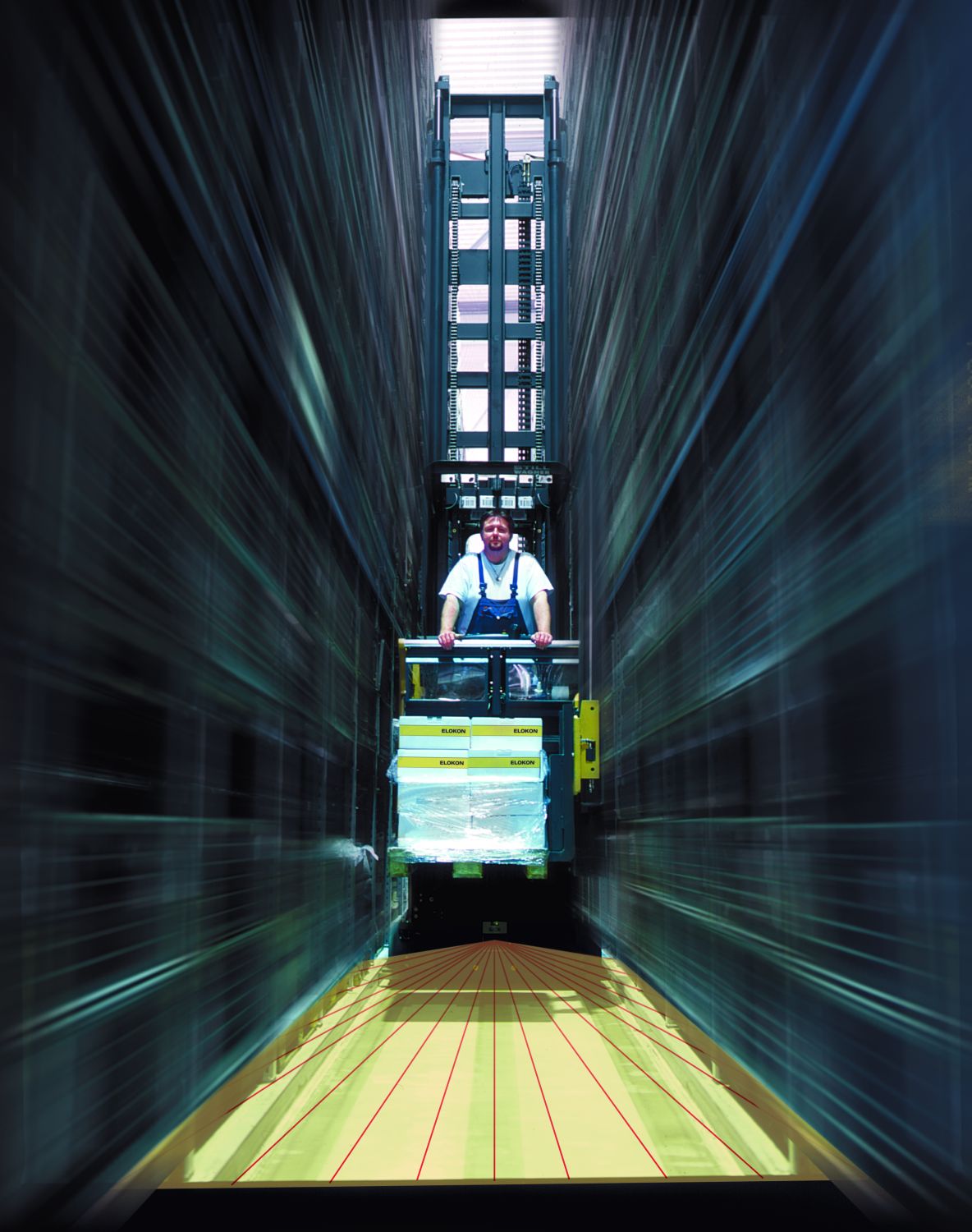
źródło: Elokon
Zabezpieczenia techniczne przy wejściach do korytarzy są urządzeniami stacjonarnymi (bariery świetlne, układy fotokomórek, moduły RFID) montowanymi na regałach. Dlatego nazywa się je stacjonarnymi systemami bezpieczeństwa. Muszą one odróżniać pieszych od wózków i uniemożliwiać dostęp pieszym do korytarza, w którym pracuje wózek lub wjazd wózka, jeżeli w tym czasie znajdują się tam piesi. Zabezpieczenia takie, gdy w jednym z korytarzy znajdą się jednocześnie piesi i wózek, muszą wywoływać alarm, dając jednocześnie sygnał optyczny i akustyczny.
Systemy te, w zależności od wersji, mają swoje ograniczenia i niedoskonałości. Mogą na przykład nie rozpoznawać liczby osób wchodzących i wychodzących i w tym przypadku może zdarzyć się sytuacja, że do korytarza wejdą równocześnie obok siebie dwie osoby, a wyjdzie jedna. Dla systemu oznacza to, że korytarz jest wolny i możliwa jest w nim praca wózka. Dlatego też, aby uniknąć takiej sytuacji, osoby piesze zobowiązane są do bezwzględnego przestrzegania odpowiednich zasad i reguł bezpieczeństwa przy użytkowaniu systemów stacjonarnych.
Obydwa wyżej opisane systemy stanowią jedynie zabezpieczenie dostępu dla osób trzecich do korytarzy i w swoich wersjach standardowych nie oddziałują w żaden sposób na system sterowania pracą wózka i nie są zabezpieczeniem dla pieszych, którzy pomimo zakazów mogą znaleźć się w korytarzu podczas pracy wózka. Dlatego też coraz częściej doposaża się systemy stacjonarne w moduły transmisji sygnału z bramki kontrolnej do wózka, aby ostrzec operatora lub nawet wywołać odpowiednią automatyczną interakcję wózka (np. spowolnienie jazdy, zatrzymanie).
W końcu lat 80. pojawiły się zabezpieczenia techniczne na wózkach, tzw. mobilne systemy bezpieczeństwa. Jest to metoda, która może zostać zastosowana w już pracującym magazynie, ponieważ związana jest z wózkiem, nosicielem niebezpieczeństwa, a nie z konstrukcją regałów czy magazynów. Normy, które powstały i dotyczą tych urządzeń, mówią, że „Na wózkach musi znajdować się samodzielnie działające urządzenie, które w wystarczającej odległości kontroluje obszar poruszania się wózka i w momencie wykrycia człowieka lub przeszkody daje operatorowi wózka sygnał optyczny i akustyczny, a jeżeli na to pozwala techniczne wyposażenie wózka, to automatycznie zatrzymuje go”.
Metoda ta jako jedyny środek zabezpieczający oddziałuje na układ sterowania i hamowania wózka i umożliwia zatrzymanie go przed przeszkodą w bezpiecznej odległości.
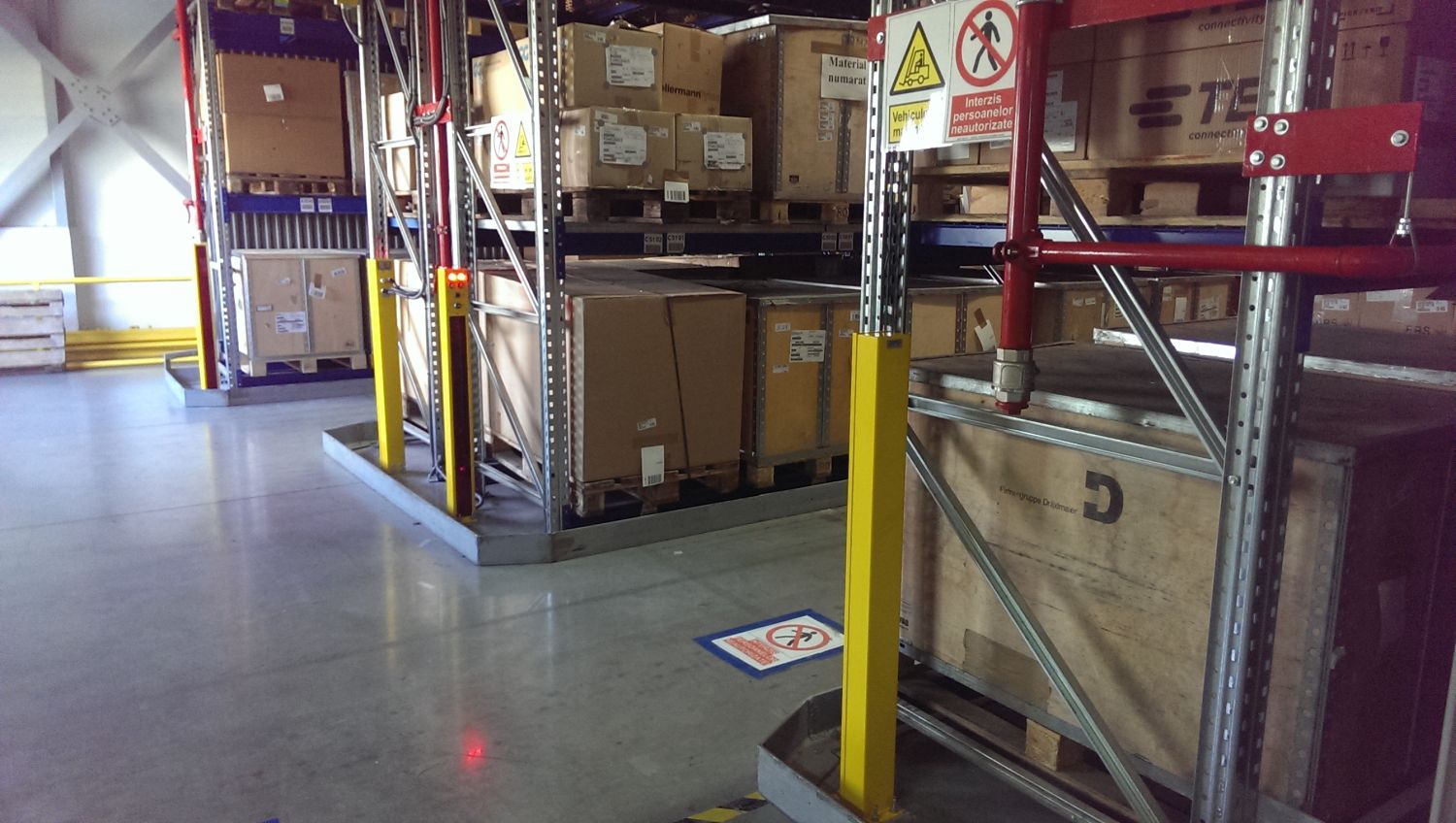
źródło: Elokon
Mobilne systemy bezpieczeństwa są rozwiązaniami najbardziej zaawansowanymi, niezwykle skutecznymi i elastycznymi w zastosowaniu.
Systemy te w ciągu ostatnich dziesięciu lat bardzo się rozpowszechniły i są propagowane przez kręgi BHP. Stanowi to odzwierciedlenie przepisów unijnych, dotyczących bezpieczeństwa pracy, w których jest jednoznacznie określony zakres wyposażenia maszyn i urządzeń w systemy zabezpieczające (Dyrektywa Unii Europejskiej 98/37/EWG).
Pomimo że praca wózka jest zabezpieczona przez jeden z wyżej podanych systemów, należy pamiętać, że zgodnie z obowiązującymi przepisami każdy korytarz musi posiadać odpowiednie oznakowanie, wyraźnie wskazujące, że przebywanie w jednym czasie wózków i pieszych w jednym korytarzu jest niedozwolone. Jest to bardzo istotne, gdyż urządzenie zabezpieczające może zawieść i jego zastosowanie nie zwalnia pracodawcy z obowiązku przeszkolenia i dokładnego poinformowania pracowników o ryzyku szczątkowym oraz zagrożeniu stwarzanym przez poruszający się wózek widłowy.
Logistyka rozwija się bardzo dynamicznie i ciągle idzie do przodu w zakresie nowych rozwiązań i optymalizacji już istniejących. Przykładem tego jest, pojawiające się coraz częściej, dążenie do tworzenia tzw. układów pracy mieszanej polegających na jednoczesnym przebywaniu pieszych i wózków w wąskich korytarzach. Takie rozwiązanie jest bardzo niebezpieczne, aczkolwiek nie niemożliwe do realizacji. I w tym przypadku bezwzględnie wymagane jest stosowanie mobilnych systemów bezpieczeństwa i to o podwyższonej klasie, jak również dodatkowych specjalnych zabezpieczeń montowanych na regałach. Dokładny opis odnośnie wymagań, założeń i sposobu rozwiązania podaje niemiecka norma DIN 15185 (DIN 15185-2:2013-10 Flurförderzeuge – Sicherheitsanforderungen – Teil 2: Einsatz in Schmalgängen // Industrial trucks – Safety requirement – Part 2: Use in narrow aisles)
ELOKON posiada w swojej ofercie zarówno stacjonarne, jak i mobilne systemy bezpieczeństwa. Są to odpowiednio ELObar i ELOprotect, które mogą występować w różnych wariantach. Oczywiście standardowo oferujemy każdemu klientowi pełne wsparcie w analizie problemu, oszacowaniu i ocenie ryzyka związanego z pracą wózków w magazynach (w szczególności wózków systemowych VNA w magazynach wysokiego składowania z wąskimi korytarzami) oraz doborem i zastosowaniem właściwych rozwiązań.
Jarosław Kociszewski
Prezes Zarządu, Dyrektor Zarządzający
ELOKON Logistics Sp. z o.o.