Koncepcja pętli jakości Deminga opiera się na założeniu nieprzerwanego doskonalenia. Każdy niekorzystny sygnał jest punktem wyjścia do działań korygujących, które ponownie są oceniane pod kątem ich skuteczności.
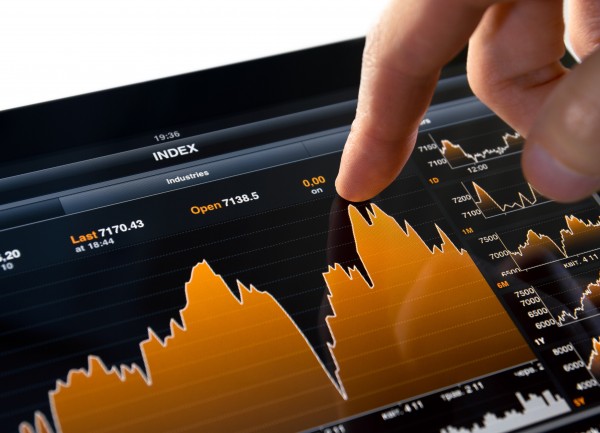
Amerykański statystyk William Edwards Deming opracował podstawy statystycznego procesu kontroli, zakładającego wykorzystanie narzędzi statystycznych do oceny poziomu jakości. Ponieważ w USA jego koncepcja nie wzbudziła zainteresowania, przeniósł się do Japonii, gdzie z powodzeniem wdrażał swoje pomysły. Deming to twórca koncepcji zarządzania jakością opartej na trzech zasadach: orientacji na klienta (szczególnie istotnej przy planowaniu, projektowaniu nowego wyrobu lub usługi), ciągłym doskonaleniu (opartym na uwzględnianiu opinii klientów), systemowym zapewnieniu jakości (obejmującym całą firmę). Doskonalenie jest tutaj jednym z podstawowych wymagań wobec systemu zarządzania jakością. Ma być celem wszystkich operacji realizowanych na różnych poziomach zarządzania firmą, w obszarach planowania, projektowania, zaopatrzenia (cena nie może być podstawowym kryterium wyboru), technologii.
Deming określił 14 zasad zarządzania projakościowego. Najważniejsze z nich dotyczą realizacji działań nastawionych na uzyskanie trwałej przewagi konkurencyjnej. Ocena poziomu jakości obejmuje projekt produktu lub usługi, metody produkcji, specyfikacje materiałowe, narzędzia marketingu i reklamy, strategię sprzedaży i dystrybucji. Celem nie jest rozbudowa tradycyjnie rozumianej kontroli jakości. Kontrola w potocznym rozumieniu ma charakter rygorystyczny, polega na odrzuceniu wyrobu gotowego, który nie spełnia standardów. W tym przypadku celem jest sprawdzenie efektów, zgodności z oczekiwaniami klienta, a następnie weryfikacja. Zasady te stały się podstawą idei ciągłego doskonalenia, która została nazwana pętlą (kołem) jakości.
Koncepcja pętli Deminga zakłada wykonywanie uporządkowanych, następujących po sobie w ustalonej kolejności i w nieprzerwanym cyklu działań, typowych dla układu ze sprzężeniem zwrotnym, czyli takich, gdzie sygnał na wyjściu staje się impulsem do uruchomienia działań w kolejnej pętli.
Czynności określone jako Plan, Do, Check, Act, (w skrócie PDCA) oznaczają: planowanie, wykonanie, kontrolę i ponowne działanie połączone z korektą wcześniejszych ustaleń. Na pierwszym etapie PDCA znajduje się planowanie, stanowiące działania przygotowujące do projektowania produktu lub usługi. Obejmują one określenie najważniejszych oczekiwań klientów wobec produktów lub usług, wskazanie innowacji i nowości, jakie mogą się wkrótce pojawić na rynku (np. telewizory LED, które mają wyprzeć telewizory LCD), najbardziej wartościowe zdaniem klientów produkty i usługi w danej branży. Na tym etapie należy odpowiedzieć na pytania, co może być źródłem przewagi konkurencyjnej (produkt, cena, jakość, dostępność), co ma być kluczową zaletą, która pozwoli przekonać do siebie klientów. Określa się aktualny poziom produkcji konkurentów i prognozuje przewidywaną dynamikę zmian ich potencjału produkcyjnego w przyszłości.
Drugi etap to wykonanie. W czasach Deminga kluczowe było pytanie, jak wykonać produkt, by spełniał on wymagania klienta, by cena była do zaakceptowania, by poziom jakości był stabilny. Współcześnie częściej podejmowane są decyzje "make or buy" – czyli czy wykonywać zadanie samodzielnie, czy skorzystać z oferty firm zewnętrznych.
Trzeci etap dotyczy kontroli (określanej także jako ocena, weryfikacja). Pozwala on stwierdzić, na ile wysiłki podjęte na pierwszych dwóch etapach okazały się skuteczne; czy zaawansowany technologicznie produkt nie jest zbyt drogi albo wyposażony w zbędne funkcje, które są potwierdzeniem zaawansowania technicznego, ale w efekcie okazują się niepotrzebne klientowi. Celem tego etapu jest identyfikacja słabych punktów produktu lub usługi, która umożliwi dokonanie korekt i usprawnień. Metody, które stosowane są zwykle na tym etapie, to:
1. metoda pomiarowa (prędkość, wskaźniki eksploatacyjne, koszty obsługi, zużycie energii);
2. metoda rejestracji (np. uszkodzeń);
3. badanie satysfakcji klientów.
2. metoda rejestracji (np. uszkodzeń);
3. badanie satysfakcji klientów.
W metodzie pierwszej stosuje się głównie wskaźniki jednostkowe (np. poziom zużycia paliwa). Druga z nich bazuje na wskaźnikach pokazujących stopień niezawodności (brak uszkodzeń, trwałość, awaryjność). Metody stosowane przy badaniu satysfakcji klienta mogą polegać na:
- ocenie poziomu sprzedaży na tle konkurencji lub procentowym udziale w rynku – należy pamiętać, że nie zawsze jest to dobre źródło informacji, spadek sprzedaży może być krótkotrwały, np. jako skutek krótkotrwałej akcji promocyjnej realizowanej przez konkurencję;
- analizie reklamacji – jest to zwykle wiarygodne źródło informacji, jednak brak skarg nie musi oznaczać, że klienci są zadowoleni z produktu lub usługi; pewien właściciel hotelu zwykł twierdzić, że jeśli klient opuszczający takie miejsce nie zgłasza żadnych uwag, to znaczy, że już nigdy nie skorzysta z usług tego hotelu.
Ostatni, czwarty etap to korekta, czyli wprowadzenie zmian i modyfikacji. Po nim następuje kolejny krąg pętli planowanie – wdrożenie – kontrola – korekta. Podejmowane działania zależą od cyklu życia i etapu rozwoju technologii (wprowadzenie na rynek, wzrost, dojrzałość, schyłek). Na etapie wprowadzania na rynek liczy się rozwój i innowacyjność nowej technologii, na etapie wzrostu nowe możliwości ekspansji, na etapie dojrzałości i schyłku istotne jest ograniczanie kosztów i dokonywanie drobnych modyfikacji. Planuje się wtedy wdrażanie technologii kolejnej generacji i stopniowe dopasowywanie jej (przy pomocy PDCA) do oczekiwań rynku.
Stworzona przez Deminga koncepcja okazuje się wciąż żywa, z powodzeniem wykorzystywana jest w przedsiębiorstwach, w których potrzeba ciągłej zmiany jest podstawą innowacyjności. Teoria koła powraca też za sprawą ożywionego zainteresowania w obecnym okresie koncepcjami szczupłej produkcji. Pozwala powiem w prosty sposób oceniać wymiar każdej zmiany dotyczącej firmowego produktu i procesu.
Mariusz Szuster
Uniwersytet Ekonomiczny w Poznaniu
Uniwersytet Ekonomiczny w Poznaniu