Z problemem zwrotu towarów do magazynu boryka się dziś niemal każdy, a przyczyn takiego stanu rzeczy może być co najmniej kilka: dynamiczny rozwój sektora e-commerce, kapryśne gusta klientów indywidualnych, wady produktowe, błędy ludzkie i wiele innych. Sęk w tym, aby niezależnie od przyczyny zwrócony towar sprawnie obsłużyć w sposób, który nie wpłynie niekorzystnie na płynność pracy całego magazynu.
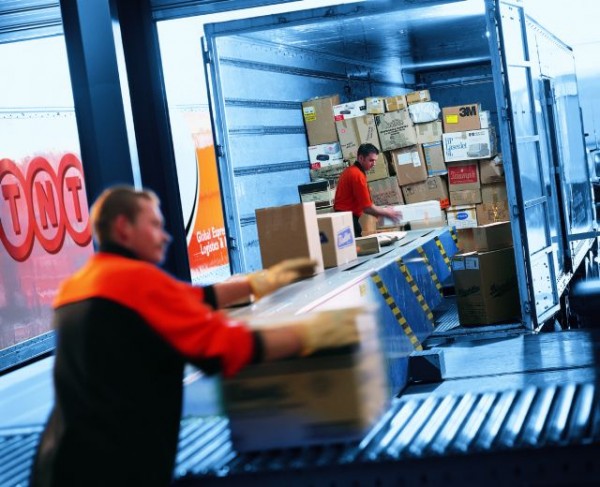
Najczęściej wymienianą przyczyną zwrotu towaru do magazynu zdaje się być błąd czynnika ludzkiego w procesie kompletacji zamówienia, bądź na etapie jego wysyłki do klienta. Wtedy to okazuje się, że na skutek pomyłki, klient otrzymuje towar uszkodzony, niekompletny, bądź zupełnie inny niż zamawiał. Taka sytuacja skutkuje odesłaniem go do sprzedawcy i koniecznością powtórnego przyjęcia do magazynu z uwzględnieniem pewnych wymaganych procedur.
Pomyłki mogą wkraść się już na etapie rejestracji towaru w magazynie dostawcy, przez co są one trudne do wykrycia w procesie realizacji wysyłki. Mogą one dotyczyć źle wprowadzonych danych w przypadku braku lub nieczytelnych kodów kreskowych lub też złej ilości przyjętych danych. Błędy mogą zdarzyć się również podczas procesu kompletacji. – Pracownik skanując kod lokalizacji może niechcący pobrać towar z innej lokalizacji i jeśli system WMS nie wymaga weryfikacji artykułu, mamy źle pobraną pozycję. Błąd może zdarzyć się nawet podczas ładowania towaru na samochód. Pobranie niewłaściwej palety i odłożenie do niewłaściwego samochodu to problem, z jakim mierzą się na co dzień wielkie centra dystrybucyjne, wyposażone w kilkadziesiąt doków – mówi Marcin Figlarek, Konsultant ds. logistyki i systemów WMS w Consafe Logistics.
Bardzo często przyczyną powstawania błędów w realizacji wysyłek jest niewłaściwa organizacja pracy w magazynie. Brak jasno określonych procedur postępowania sprawia, że pracownicy stosują swoje własne procedury, które są dobre dla nich, ale nie zawsze dobre dla całej organizacji. – Rodzi to chaos, który powoduje znaczący wzrost ryzyka popełnienia błędu. Poprawę organizacji pracy należy rozpocząć od właściwego zamodelowania procesów logistycznych, które następnie powinny zostać odwzorowane w systemie WMS. Takie połączenie gwarantuje ograniczenie liczby pomyłek do minimum – radzi Jacek Gabryel, Dyrektor IT w firmie Elandis.
Najczęstsze pomyłki
Problem częstego pojawiania się zwrotów występuje najczęściej w przypadku magazynów manualnych. Dodatkowym czynnikiem, wpływającym negatywnie na jakość wysyłek, jest duża baza indeksów, która dodatkowo często rotuje, np. w wyniku częstego wprowadzania nowych produktów. – W takim przypadku, jeśli system WMS nie wspiera odpowiednio procesów kompletacji, operator magazynu musi podejmować decyzję na podstawie własnej wiedzy, co rodzi potencjalną możliwość powstawania błędów – przestrzega Jerzy Danisz, WMS Competence Center Manager w firmie PSI. Jeśli mamy do czynienia z dużą liczbą pobrań, wówczas występuje wiele czynności polegających na identyfikacji, weryfikacji i pobraniu, a to sprzyja pojawieniu się pomyłek na skutek czynnika ludzkiego. Dodatkowo, jeśli towary mają zbliżone opakowania i wymiary, są w podobnych lub wręcz identycznych kolorach, zdarza się, że najlepsze procedury mogą zawieść, gdy będą egzekwowane przez niedoświadczonych pracowników. Oznacza to, że niekoniecznie sama wielkość magazynu i ilość indeksów przekłada się wprost proporcjonalnie na liczbę błędów. – Istnieje ścisły związek pomiędzy rotacją pracowników magazynowych a ilością pomyłek. Pracownicy pracujący dłużej znają towar lepiej i wiedzą z doświadczenia, przed jakimi błędami się ustrzec. Systemy motywacyjne dodatkowo mogą zmniejszyć współczynnik błędów – mówi Marcin Figlarek z Consafe Logistics.
Pomyłki mogą wkraść się już na etapie rejestracji towaru w magazynie dostawcy, przez co są one trudne do wykrycia w procesie realizacji wysyłki. Mogą one dotyczyć źle wprowadzonych danych w przypadku braku lub nieczytelnych kodów kreskowych lub też złej ilości przyjętych danych.
Opinię na temat znaczenia czynnika ludzkiego w magazynie potwierdza Michał Czerwiec, Dyrektor ds. Rozwoju Biznesu w firmie ELSE, który twierdzi, że łatwiej działa się firmie, która obraca wąskim asortymentem i wydaje go w dużych ilościach. – Wówczas magazynier jest w stanie szybko „nauczyć” się produktów, przez co błędów jest relatywnie mniej. Najgorzej jest w magazynach, gdzie towar jest mocno zróżnicowany i wydaje się go w niewielkich ilościach – twierdzi nasz rozmówca. – W takich miejscach automatyczna identyfikacja i system WMS najszybciej dają zauważalne korzyści – dodaje.
Problem zwrotów pojawia się w każdej branży, natomiast różne może być jego nasilenie. Firmy działające w sektorze e-commerce oraz prowadzące bezpośrednią sprzedaż do klienta końcowego borykają się z nim najczęściej, ponieważ konsument posiada szereg praw umożliwiających mu rezygnację z zakupu, nawet jeśli dostawca w stu procentach wywiązał się ze swoich obowiązków. – Sprzedaż detaliczna wiąże się generalnie z większym ryzykiem dokonywania przez klientów zakupów nieprzemyślanych, które skutkują licznymi reklamacjami. Natomiast ze strony sprzedawcy częste zwroty wiążą się z m.in. z błędami popełnianymi podczas wysyłki, np. dostarczenie produktu innego niż zamawiany, wysyłka w nieodpowiednie miejsce lub niewłaściwej ilości towaru – mówi Jacek Gabryel z Elandis. Kwestia ta dotyka przede wszystkim firm, których magazyny borykają się z problemem nieuporządkowania towarów oraz niestosowania szczegółowych procedur przyjmowania i wysyłki produktów.
Okazuje się, że z bardzo dużą ilością zwrotów mamy do czynienia również w magazynach obracających towarem sezonowym. Szczególnie dzieje się to w firmach, które wysyłają asortyment nie bezpośrednio do odbiorcy, ale do sklepów. – Często bowiem sklepy mają prawo zwrotu w przypadku braku sprzedaży i zakończeniu sezonu na dany towar. Przykładem mogą być artykuły instalacyjne. U jednego z naszych klientów są okresy, gdzie zwrotów ze sklepów jest więcej niż dostaw od producentów – obrazuje Marcin Figlarek z Consafe Logistics.
Różnica zwrot vs. przyjęcie
Na pierwszy rzut oka wydawać by się mogło, że obsługa zwracanego do magazynu towaru to prawie jak przyjęcie nowej jednostki do systemu. W rzeczywistości jednak to mylne stwierdzenie, co wynika chociażby z konieczności zakwalifikowania każdego produktu z osobna ze względu na przyczynę zwrotu. To z kolei determinuje dalszy los zwracanego produktu. Wskutek wady czy uszkodzenia może zostać całkowicie wycofany z systemu. Z kolei jeżeli wraca do magazynu w stanie nienaruszonym, a zwrot jest efektem kaprysu klienta, z pewnością trafi do dalszej sprzedaży.
Bardzo często przyczyną powstawania błędów w realizacji wysyłek jest niewłaściwa organizacja pracy w magazynie. Brak jasno określonych procedur postępowania sprawia, że pracownicy stosują swoje własne procedury, które są dobre dla nich, ale nie zawsze dobre dla całej organizacji.
Różnica pomiędzy zwrotem a standardowym przyjęciem towaru polega na tym, że obsługa zwrotów jest przede wszystkim procesem dodatkowym, który nie zawsze można przewidzieć i odpowiednio zaplanować. Bardzo często konieczne jest oderwanie ludzi od ich regularnej pracy, przez co zaplanowane działania ulegają opóźnieniu i wzrasta ryzyko popełnienia błędu podczas pogoni za terminem. – Ta nieprzewidywalność rodzi również kolejny problem – konieczność wygospodarowania dodatkowej przestrzeni do przechowywania zwróconego towaru, który zwykle przebywa w specjalnych strefach do momentu, kiedy nie zostanie zweryfikowany i sklasyfikowany. Bardzo często taka weryfikacja nie następuje w chwili przyjęcia zwrotu, a w zależności od polityki firmy, w przeciągu kilku godzin lub dni – mówi Jacek Gabryel z Elandis.
Ponadto różnica pomiędzy obsługą zwrotów a standardowym przyjęciem towaru polega na tym, że system WMS „wie”, co wcześniej zostało wydane. – Dzięki temu możliwe jest połączenie wcześniejszego zlecenia wydania towaru z procesem przyjęcia zwrotu. Dzięki temu system WMS może przejąć dane o wydanych produktach z wcześniej zrealizowanych zleceń i automatycznie utworzyć awizację dla zwrotu, ułatwiając fizyczne przeprowadzenie procesu przyjęcia towaru – wyjaśnia Jerzy Danisz z PSI.
WMS obsłuży zwroty
Aby system WMS mógł stanowić skuteczne narzędzie do obsługi zwrotów w magazynie, powinien bezwzględnie posiadać kilka ważnych funkcjonalności. Aplikacje klasy WMS posiadają najczęściej zdefiniowaną klasyfikację ze względu na przyczynę zwrotu. – Dzięki temu mogą zarządzać ulokowaniem takich produktów, np. inaczej WMS będzie zarządzał pełnowartościowym towarem, który został zwrócony, bo nie został zamówiony przez klienta, a inaczej towarem, który ma uszkodzone opakowania, a jeszcze inaczej towarem, który jest przeterminowany – tłumaczy Michał Czerwiec z ELSE. Takie informacje muszą być przechowywane w systemie, aby możliwe było tworzenie raportów i statystyk.
Przyjęcie zwrotu najczęściej jest implementowane na bazie standardowego procesu przyjęcia z dobudowaną obsługą ewentualnych dodatkowych czynności. – Jeśli potrzebne są jakieś dodatkowe podprocesy, to realizuje się je w oparciu o wewnętrzne procedury, a tylko ich przebieg rejestruje się w systemie WMS. Czasem obsługa zwrotu polega na wykonanie korekty stanów z odpowiednią przyczyną (procedura skrócona) – mówi Jacek Liber, Dyrektor ds. Rozwoju Biznesu w BCS Polska.
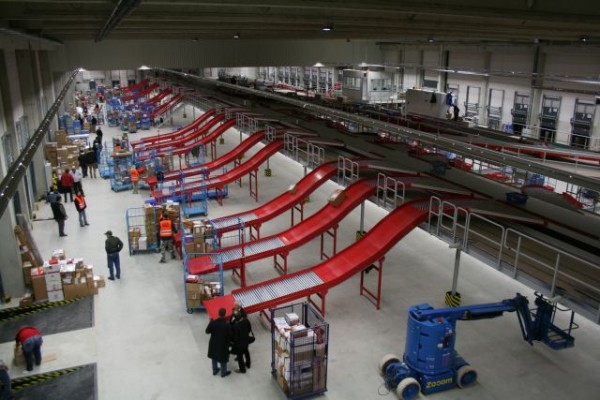
Innym przykładem typowej dla wsparcia obsługi zwrotów funkcjonalności jest automatyczne przyjęcie danych o wydanych towarach ze zleceń i utworzenie awizacji. Jeżeli towar znajdował się wcześniej w magazynie, to musi istnieć możliwość szybkiej weryfikacji, jakim dokumentem został wydany. Na jego podstawie system powinien automatycznie wygenerować dokument zwrotu. – Dalej wymienić należy procesy kontroli jakości po przyjęciu polegające na ocenie towaru pod kątem możliwości ich ponownego użycia w celu realizacji zleceń – wylicza Jerzy Danisz z PSI. Kolejnym elementem procesu, w przypadku kiedy towar ze zwrotu został zakwalifikowany do ponownego wykorzystania, jest proces rozłożenia towaru. – Towar zwracany jest z reguły w jednostce wysyłkowej (kartonie) i często zawiera różne produkty. Proces rozłożenia polega na dołożeniu towaru do lokacji magazynowych zawierających już ten indeks w celu optymalnego wykorzystania przestrzeni magazynowej – objaśnia Jerzy Danisz.
Gdy towar ponownie został przyjęty do magazynu, kolejną ważną funkcjonalnością jest blokowanie go do momentu weryfikacji. Towar nie może zostać wydany, jeśli nie zostanie zweryfikowany przez uprawnioną osobę. – Biorąc pod uwagę, że w zatłoczonych magazynach zwroty nie zawsze są fizycznie odseparowane od produktów pełnowartościowych, to system WMS musi uniemożliwić jego ponowne wydanie i wyeliminować ryzyko błędu ze strony pracownika magazynu – zaznacza Jacek Gabryel z Elandis. Inną, ale nie mniej istotną kwestią jest możliwość dynamicznego rozdzielania zadań pomiędzy magazynierów. Jeśli w normalnym cyklu pracy pojawi się zadanie dodatkowe, takie jak przyjęcie zwrotu, to za sprawą systemu WMS kierownik magazynu powinien mieć sposobność przydzielenia zadania odpowiedniej osobie i monitorowania statusu jego wykonania.
Michał Klecha
***
Błędy ludzkie
– Nieprawidłowości podczas realizacji wysyłek towarów to zazwyczaj powiązanie błędu ludzkiego z nieodpowiednią konfiguracją systemu WMS, co pozwala na „obejście” pewnych kroków w procesach magazynowych. Jeśli system WMS dopuszcza wprowadzenie niektórych informacji bez weryfikacji np. kodu kreskowego, wtedy pracownicy mogą błędnie identyfikować lub pomijać system, pobierając inny zasób. Częsty problem podczas wydań to również brak weryfikacji wysyłek przez innego pracownika lub sprzętowo np. przy użyciu wag weryfikujących, które porównują masę skompletowanego towaru z sumą wag zapisanych na kartach wydawanych towarów.
Jakub Bieszke
Starszy konsultant
Insoft Consulting sp. z o.o.
Starszy konsultant
Insoft Consulting sp. z o.o.
***
Szczególna uwaga
– Obsługa zwrotów wymaga od magazynu szczególnej uwagi. Towary mogą bowiem przyjść do magazynu często w nieoryginalnych opakowaniach lub też zupełnie luzem bez żadnych oznaczeń. Bywa też tak, że zwrot od klienta nie jest w ogóle awizowany, więc z góry nie wiemy, co będzie przyjęte i w jakiej ilości. Same produkty są często pomieszane na palecie, co wymaga dużej pracochłonności przy rozkładaniu towaru na półki. Z tego względu proces ten musi różnić się od standardowego procesu przyjęć towaru. Wymagana jest większa weryfikacja, kontrola i dodatkowe procedury w celu określenia przyczyny zwrotu oraz możliwości naprawy lub też zaklasyfikowania towaru jako sprawny, częściowo sprawny lub niesprawny.
Marcin Figlarek
Konsultant ds. logistyki i systemów WMS
Consafe Logistics
Konsultant ds. logistyki i systemów WMS
Consafe Logistics
***
Wiele źródeł błędów
– Przyczyn powstawania błędów w realizacji wysyłek można dopatrywać się w kilku miejscach. Najczęściej wymienianym powodem powstawania błędów są pomyłki spowodowane przez człowieka. Ten czynnik jest wskazywany najczęściej, ponieważ błędy „ludzkie” powstają bez względu na to, czy w magazynie działa system WMS, czy nie. Do takich błędów można zaliczyć błędy w liczeniu i błędy w identyfikacji produktu. Z założenia system WMS nigdy nie jest przyczyną powstawania błędów. Można oczywiście założyć, że błędy programistyczne spowodują, iż pracownik w magazynie skanuje nieprawidłowy produkt, a system WMS „nie reaguje”. Byłoby to natomiast założenie z góry niewłaściwe, ponieważ każdy WMS (plus stosowanie kodów kreskowych na produktach i lokacjach) to główny czynnik eliminacji pomyłek w magazynach. Przy okazji nie można zapomnieć, że przyczyną zwrotów są nie tylko błędy powstałe w obszarze magazynu. Często powody sytuacji, w których następuje zwrot towaru, leżą poza wpływem magazynu.
Krzysztof Kalisz
Logifact-Systems Sp. z o.o.
Logifact-Systems Sp. z o.o.
***
Więcej czasu i uwagi
– Przyjęcie towaru zwracanego wymaga od operatora więcej czasu i uwagi niż standardowa obsługa przyjęcia. Zarówno zwroty planowane, jak i te poza planem wymagają przeprowadzenia szczegółowej kontroli przesyłki zarówno pod względem kompletności, jak i ewentualnych uszkodzeń. W celu monitorowania powodu zwrotów każdy z nich musi zostać dokładnie opisany. Kolejnym krokiem jest weryfikacja, czy powinna zostać przesłana do klienta przesyłka z brakującym lub wolnym od wad produktem. Idealną sytuacją jest taka, w której o sposobie postępowania i ewentualnym podjęciu dodatkowych kroków decyduje system WMS. Bez zastosowania takiego rozwiązania obsługa zwrotów staje się niezwykle czaso- i kosztochłonną operacją.
Radosław Majer
Key Account Manager
DataConsult Sp. z o.o.
Key Account Manager
DataConsult Sp. z o.o.
***
Nikt nie jest nieomylny
– Mimo zaawansowanych technologii stosowanych dziś w magazynach, w dalszym ciągu ludzie są tym czynnikiem, który najczęściej powoduje błędy. Zaawansowane systemy IT, automatyczna identyfikacja oraz rozwiązania procesowe, póki co muszą być wspomagane przez człowieka, więc i ryzyko błędów pozostanie. Dużo rzadziej problemem jest system informatyczny. Te problemy zazwyczaj wynikają z błędów w danych podstawowych, wprowadzonych przez użytkowników lub niewłaściwych założeń kluczowych algorytmów.
Michał Czerwiec
Dyrektor ds. Rozwoju Biznesu
ELSE Systemy Informatyczne
Dyrektor ds. Rozwoju Biznesu
ELSE Systemy Informatyczne