Proces kompletacji zarówno w magazynie, jak i na produkcji ma zasadnicze znaczenie dla końcowego powodzenia projektu. Wydajna kompletacja umożliwia bezprzestojową realizację planów produkcyjnych, a przy tym zapewnia kompletność i wysoką jakość wyrobów finalnych. Rynek oferuje szeroki zakres narzędzi kompletacji, z których korzystają firmy produkcyjne, poczynając od kodów kreskowych i terminali, przez technologie świetlne, głosowe, po łączące obie metody.
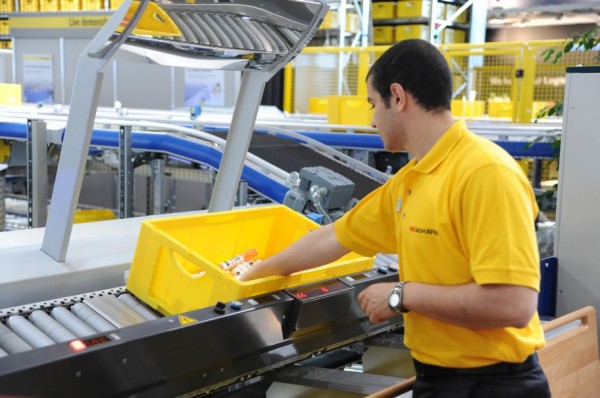
– O ile na zwykłym magazynie zazwyczaj występują okna kompletacyjne, w których musimy się zmieścić ze wcześniej zaplanowanymi zleceniami, o tyle w obszarze produkcji plan taki można określić bardzo szacunkowo i trzeba na bieżąco, szybko reagować na zmienne zapotrzebowanie z gniazd produkcyjnych. Bardziej istotna jest więc organizacja procesu niż szybkość działania – mówi Jacek Liber, Dyrektor Działu badań i Rozwoju w firmie BCS Polska.
Najprościej rzecz ujmując, wydajność kompletacji stanowi wypadkowa szybkości i jakości kompletacji, a więc realizacja bezbłędnego pickingu w jak najkrótszym czasie. Dodatkowo pojęcie wydajności kompletacji można wzbogacić o takie czynniki, jak ergonomia i komfort pracy, bezpieczeństwo i elastyczność w przypadku zmian zachodzących w procesie.
Co oferuje rynek?
W zależności od charakteru procesu produkcyjnego, który w każdym przedsiębiorstwie wygląda inaczej, dla każdego inne rozwiązanie może okazać się optymalne.
Pierwszym przykładem może być automatyczna identyfikacja, czyli kompletowanie elementów w oparciu o kody kreskowe z wykorzystaniem skanerów i ręcznych terminali danych, na których operator otrzymuje z systemu informacje o zestawie elementów, które należy skompletować na danym etapie procesu. Czytniki kodów paskowych, kodów 2D czy tagów RFID pozwalają jednoznacznie zidentyfikować produkt, co minimalizuje możliwość pomyłki. To uniwersalna metoda umożliwiająca dokładne sprawdzenie zarówno numeru seryjnego danego produktu (konieczne w takich przypadkach, jak np. silniki samochodowe), jak i potwierdzenia właściwego miejsca poboru lub odłożenia nawet dla produktów, które takich kodów nie posiadają, przez zeskanowanie kodu miejsca magazynowego.
Skorzystanie z tej metody eliminuje konieczność wydruku i obsługi dokumentów papierowych i zmniejsza ilość popełnianych błędów w porównaniu z przechodzącą już do lamusa metoda kompletacji papierowej. Dokładny zapis danych pozwala monitorować produkcję w toku. Do minusów tej metody pickingu można zaliczyć konieczność angażowania wzroku i rąk operatora, co może wpływać na rozproszenie jego uwagi.
– Kompletacja dzięki informacjom przekazywanym na wyświetlaczu skanera czy terminala nie sprawdza się przy kompletacji dużej liczby produktów, ponieważ podobnie jak w metodzie papierowej pracownik potrzebuje czasu na odnalezienie właściwego miejsca w magazynie. Dodatkowo terminale zajmują ręce pracownika, a w przypadku skanerów nadgarstkowych lub napalcowych obciążają jego ręce, zmniejszając komfort pracy – potwierdza Sławomir Skarbecki, Dyrektor firmy LUCA Systemy Logistyczne.
Często spotykaną w zakładach produkcyjnych metodą pickingu jest system Pick-to-Light, czyli wskazujący operatorowi kolejne miejsca poboru elementów za pomocą światła w postaci specjalnych diod wmontowanych w gniazda regałowe. Komunikacja operatora z systemem odbywa się poprzez panele zlokalizowane zwykle pod gniazdami, które wyświetlają dodatkowe informacje np. o ilości elementów do pobrania i wyposażone są w przyciski do potwierdzania wykonanych czynności. Ta prosta w obsłudze metoda umożliwia bardzo dużą wydajność przy małych strefach (mała ilość SKU na operatora). Sławomir Skarbecki szczególnie poleca tę właśnie metodę pickingu na produkcji, która w ofercie firmy LUCA dostępna jest w różnych odsłonach.
– W naszej ocenie światło jest najlepszym wskaźnikiem miejsc magazynowych przy kompletacji, dlatego polecamy metodę Pick-by-Light, Pick-by-Point® lub Pick-by-Frame® wszędzie, gdzie jest to możliwe. Moduły Pick-by-Light oraz lampy Pick-by-Point® umożliwiają stosowanie wielu kolorów i mruganie światła, dzięki czemu w prosty sposób można przekazać pracownikowi dodatkowe informacje, np. o miejscu odłożenia, poborze wielokrotnym itp. – przekonuje Sławomir Skarbecki.
W systemach LUCA, które są łatwo konfigurowalne, w razie potrzeby informacje o ilości produktów można przekazać dzięki wyświetlaczom numerycznym umieszczonym na modułach, a w metodzie Pick-by-Point® przez słuchawki bezprzewodowe. Potwierdzenie poboru może odbywać się ręcznie przez naciśnięcie przycisku kwitującego lub automatycznie za pomocą czujników podczerwieni umieszczonych w modułach, a w metodzie Pick-by-Point® za pomocą kurtyny podczerwieni Pick-Radar® kontrolującej dostęp do wielu gniazd magazynowych jednocześnie.
Oczywiście wszelkie metody z wykorzystaniem światła trudno zastosować w magazynach oświetlonych bezpośrednim światłem słonecznym. Inne ograniczenie stanowi fakt, że zainstalowanie standardowego systemu Pick- to-Light na regałach nie nadaje się do procesów, w których miejsca magazynowe są często rotowane, ponieważ występuje konieczność kablowego połączenia modułów wyświetlaczy. Dodatkowym problemem może być ograniczona pojemność i utrudnienia w pracy wielu pracowników w jednym obszarze.
W procesach pickingu na produkcji znajdują również zastosowanie systemy głosowe. W tym przypadku wolne ręce operatora i odciążenie wzroku dzięki komunikacji werbalnej z systemem pozwala skupić koncentrację pracownika na zadaniach kompletacji. Korzystając z technologii głosowej operator dodatkowo optymalizuje wykorzystanie czasu, np. poprzez możliwość zadawania systemowi pytań podczas przechodzenia do kolejnych lokalizacji. Prostota rozwiązań głosowych pozwala też w łatwy sposób elastycznie reagować na zwiększenie zapotrzebowania na siłę roboczą w strefach kompletacji.
– W rekomendowanym przez nas systemie topSPEECH-Lydia wszystkie informacje, takie jak miejsce magazynowe i ilość do pobrania, są przekazywane naturalnym głosem. Dzięki zastosowaniu wielojęzykowego systemu rozpoznawania mowy nie jest konieczny żaden trening językowy, przez co możliwe jest natychmiastowe zatrudnienie pracowników sezonowych lub czasowych – mówi Sławomir Skarbecki (LUCA). – Z terminalami głosowymi współpracować mogą bezprzewodowe skanery nadgarstkowe, co eliminuje zbyt częste lub zbyt szczegółowe potwierdzanie głosem (np. czytanie długich liczb kontrolnych miejsc magazynowych). System umożliwia wprowadzenie różnych scenariuszy i dialogów dopasowanych do indywidualnych potrzeb (np. podawanie nazwy produktu i jego cech, zbieranie w wielu etapach itp.) – dodaje.
Jak każda, również ta metoda nie jest wolna od ograniczeń i z pewnością nie może zostać zastosowana wszędzie. Na przykład w strefach o podwyższonym poziomie hałasu komunikacja głosowa między pracownikiem a systemem mogłaby zostać zaburzona. Dodatkowo warto zwrócić uwagę na czynnik typowo ludzki.
– Pracownicy z czasem uczą się „na pamięć” tak zwanych „sum kontrolnych” i zaczynają potwierdzać kompletację towaru przed jego faktycznym pobraniem – przestrzega Mateusz Mrozowski, WMS OPTIpromag Manager w firmie Optidata.
Zgodność sekwencyjna
Kompletowanie określonych zestawów elementów i dostarczanie ich na odpowiednie miejsce w toku produkcji w ściśle określonym czasie jest szczególnie istotne w zakładach produkujących w oparciu o koncepcję Just-in-Sequence. Tutaj tym bardziej nie ma miejsca na jakiekolwiek błędy czy przestoje na etapie pickingu poszczególnych zestawów.
– Dzisiaj śmiało można powiedzieć, że dzięki inteligentnym rozwiązaniom skutecznego i przede wszystkim wydajnego kompletowania, firma uzyskuje znacznie wyższą dochodowość. Procesy komisjonowania ułatwiają w pełni automatyczne udostępnianie produktów bądź zautomatyzowane systemy kontrolne. Wiąże się to z niezwykłą elastycznością systemów pick-by, które można zintegrować w każdy przebieg procesu, niezależnie od stopnia automatyzacji. W tym do realizacji koncepcji Just-in-Sequence na produkcji – komentuje Mateusz Mrozowski.
W opinii Jacka Libra omawiane technologie to tylko narzędzia, które sprawdzą się dopiero wtedy, kiedy zostaną wyposażone w odpowiednio zaprojektowane oprogramowanie. – Myślę, że technologie te potrafią sobie w obecnych czasach bardzo dobrze radzić z takimi wymaganiami. Dzisiejsze czytniki kodów potrafią bardzo szybko i bezbłędnie odczytywać kody (nawet te gorszej jakości), a systemy głosowe bezbłędnie rozpoznają komendy, nawet w głośnym otoczeniu – twierdzi nasz rozmówca. Jego zdaniem kluczem do uzyskania oczekiwanej wydajności procesu jest odpowiednie zaprojektowanie i zaimplementowanie. Wybór technologii powinien być elementem wtórnym wynikającym z tego projektu, a niebędącym jego podstawą.
Kompletacja sekwencji jest bardzo popularna w przemyśle automotive, gdzie dużym doświadczeniem może pochwalić się LUCA. W zrealizowanych wdrożeniach w fabrykach Fiat Auto Poland, Škoda Auto, General Motors Espana, GM Vauxhall, Iveco, New Holland Tractor, Schnellecke Slovakia, Volkswagen AG, firma z powodzeniem wykorzystuje różne kombinacje łączące odmiany autorskich systemów z wykorzystaniem światła, głosu czy e-papieru.
– Największą popularnością cieszy się jednak ostatnio nasz autorski system Pick-by-Frame®, w którym pracownik kompletuje części dla sekwencji samochodów za pomocą samonośnej ramy z modułami Pick-by-Light – mówi Sławomir Skarbecki.
Przykładowe wdrożenia
BCS Polska ma na koncie wdrożenie systemu wydawania na produkcję u producenta z branży automotive, które zostało zrealizowane w oparciu o aplikację przygotowaną na platformie bcsDragon ze zintegrowaną funkcjonalnością obsługi pozostałych magazynów w przedsiębiorstwie (magazyn wyrobów gotowych i magazyn surowców). W systemie zostały przygotowane dwa procesy zasilania produkcji:
1. dostawa na produkcję z magazynu ‘supermarket’ w oparciu o zapotrzebowanie ustalane na podstawie systemu Kanban (karty zapotrzebowania),
2. dostawa na magazyn ‘supermarket’ z magazynu głównego.
Obsługa zasilania gniazd produkcyjnych została zrealizowana przy wykorzystaniu stacjonarnych urządzeń (kiosków informacyjnych) wyposażonych w czytnik kodów, gdzie operator zajmujący się dostawą na gniazda produkcyjne odczytywał pobrane karty Kanban, rejestrując w ten sposób pobranie z magazynu ‘supermarket’ odpowiedniej ilości danego asortymentu. Zastosowanie kiosków pozwoliło wyeliminować niepotrzebne ruchy manualne.
– Zasilanie magazynu ‘supermarket’ zostało zrealizowane w oparciu o przenośne terminale mobilne. Zapotrzebowanie na towar było ustalane na podstawie zużycia lub mogło być wywoływane Ad-Hoc z poziomu terminala operatora odpowiedzialnego za poprawną realizację tego procesu – mówi Jacek Liber z BCS Polska.
W listopadzie ubiegłego roku Carlsberg Polska, jedna z najsilniejszych grup piwowarskich w Polsce, wdrożyła system Traceability – oparty o WMS OPTIpromag® firmy Optidata. Głównym celem projektu była możliwość uzyskania natychmiastowej i pewnej informacji o produkcie ulokowanym na rynku. System OPTIpromag wspiera kontrolę procesu wydań piwa z magazynów browarów w Brzesku, Sierpcu oraz Szczecinie. Wdrożone rozwiązanie pomocne jest także przy znakowaniu palet etykietą zgodną z GS1, wydawaniu palet oraz kontroli zapasów. Wszystkie procesy są realizowane w oparciu o maszyny etykietujące, instalację sieci bezprzewodowej oraz terminale radiowe. OPTIpromag wymienia dane dzięki dedykowanemu interfejsowi z systemem SAP.
– Wdrożenie systemu Traceability jest odpowiedzią na rosnące wymagania klientów, ciągłe doskonalenie naszych procesów wraz z podnoszeniem jakości usług świadczonych naszym kontrahentom. Etykieta logistyczna usprawni przepływ informacji wewnętrznej. Mamy nadzieję, iż obecna możliwość szczegółowej kontroli wydań zostanie doceniona przez nowoczesne magazyny naszych partnerów – komentuje Daniel Domanowski, kierownik projektu z ramienia Carlsberg Polska.
Ciekawym wdrożeniem w czeskich fabrykach Škody może pochwalić się LUCA. Co roku w Wolfsburgu odbywają się Dni Innowacji Logistyki Volkswagen, podczas których fabryki koncernu z 56 krajów przedstawiają swoje najlepsze rozwiązania. W ubiegłym roku prestiżową pierwszą nagrodę otrzymała Škoda Auto, która zaprezentowała system kompletacji Pick-by-Frame® firmy LUCA wykorzystujący dodatkowo bezpapierowy obieg informacji oparty na wyświetlaczach ePaper.
– Naszą metodę Pick-by-Frame® Škoda Auto wykorzystuje w wielu strefach kompletacyjnych w fabrykach w Mlada Boleslav i Kvasiny – mówi Sławomir Skarbecki.
Jak to działa? W pierwszym kroku pracownik łączy samonośną ramę z wózkiem komisjonującym. Po zeskanowaniu swojego identyfikatora wszystkie zdarzenia, logowane z dokładnością tysięcznej części sekundy, identyfikowane są dodatkowo numerem pracownika. System LUCA pobiera z WMS dane niezbędne do kompletacji części dla danej sekwencji aut. Na centralnym wyświetlaczu pracownik otrzymuje informacje o pierwszej lokacji w zoptymalizowanej ścieżce komisjonowania wraz z nazwą i opisem produktu. Skan kodu produktu lub miejsca magazynowego potwierdza prawidłowe miejsce poboru, a na modułach odpowiadających miejscom odkładczym na wózku, do których należy włożyć daną część, zaświecają się diody. Poprawne odłożenie kwitowane jest przyciśnięciem przycisku lub automatycznie za pomocą podczerwieni. Proces powtarza się dla kolejnych produktów. W ten sposób pracownik kompletuje części dla sekwencji 12 lub 24 aut przy jednym przejściu przez strefę komisjonującą.
– Dodatkowo w czasie kompletacji na e-papierowym wyświetlaczu zainstalowanym na wózku zapisywany jest numer aktualnej sekwencji wraz z jej kodem kreskowym i dodatkowe informacje potrzebne pracownikom podczas montażu na linii produkcyjnej. Metoda znacząco skróciła czas kompletacji, niemal całkowicie eliminując pomyłki pracowników. Jednocześnie znacząco podniesiono komfort pracy i całkowicie wyeliminowano z procesu drogie wydruki papierowe – podsumowuje Sławomir Skarbecki.
Przykładem zastosowania automatycznej identyfikacji na produkcji jest wdrożenie SKK w firmie Hilding Anders Polska, która jest częścią międzynarodowego koncernu Kulding Anders AB, wiodącego producenta łóżek i materaców działającego od ponad 70 lat na rynkach Europy i Azji. Aby zapewnić najwyższą jakość produkowanych towarów i obsługi klienta koniecznym było wdrożenie systemu identyfikacji zarówno wyrobu końcowego jak i poszczególnych półproduktów i surowców do produkcji. Każdy produkt finalny musi być odpowiednio oznaczony tak, aby klient w sklepie bez problemu mógł zidentyfikować gotowy, odpowiedni dla siebie wyrób. Hilding Anders Polska postanowił wdrożyć w zakładzie w Murowanej Goślinie nowoczesną technologię produkcyjną, wykorzystującą system automatycznej identyfikacji oparty o kody kreskowe oraz o tagi radiowe pracujące w paśmie UHF. Połączenie obu tych technologii w jednym rozwiązaniu sterowania procesem produkcyjnym jest pionierskim pomysłem dla tego rodzaju zakładów przemysłowych. Aby spełnić wymagania klientów, zastosowane tagi radiowe muszą być zgodne ze standardem EPC Class 1 Gen 2 ISO 18 000-6C.
Michał Klecha