Firma BURY Technologies to wiodący producent samochodowych zestawów głośnomówiących, wielofunkcyjnych uchwytów do telefonów komórkowych oraz elektronicznych ewidencji przebiegu pojazdów.
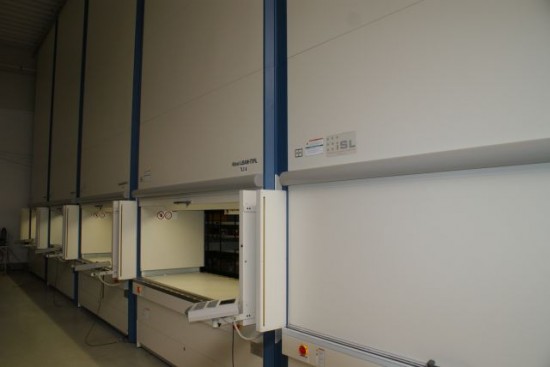
Firma kooperuje z najważniejszymi producentami telefonów komórkowych oraz z czołowymi przedstawicielami zdygitalizowanych danych nawigacji, co pozwala na szybkie reagowanie na potrzeby rynku. Bazując na własnych rozwiązaniach technologicznych, BURY Technologies tworzy innowacyjne urządzenia – jako dodatkowe wyposażenie samochodów, jak również specyficzne rozwiązania dla klientów – producentów oryginalnego wyposażenia głównych marek samochodowych (OEM). Firma dystrybuuje produkty do 50 krajów za pośrednictwem sprzedaży branżowej i serwisów samochodowych oraz dzięki swoim partnerom OEM.
BURY zatrudnia ok. ośmiuset pracowników, z czego jedną trzecią z nich stanowi kadra inżynierska. Zakłady produkcyjne, jednostki dystrybucyjne, służby marketingowe i jednostki rozwoju znajdują się w Niemczech (w Lohne w Westfalii) oraz w południowo-wschodniej Polsce (w Mielcu i Rzeszowie). Mielecki zakład jest największy, tam oprócz Działu Produkcji i Logistyki zlokalizowane są również Dział Kontroli Jakości, Dział Budowy Prototypów oraz Dział Budowy Narzędzi.
Stan faktyczny
Potrzeba dokonania zmian w funkcjonowaniu wynikała z dynamicznego rozwoju firmy. Systematycznemu poszerzaniu ulegała paleta produktów, czemu nie zawsze towarzyszyły działania optymalizujące funkcjonowanie np. procesów logistycznych. Przez lata nieustannie rosły wolumeny magazynowe. Za swoistą „piętę achillesową” uznać można dość skomplikowane zarządzanie FIFO (first in, first out – pierwsze weszło, pierwsze wyszło) dla poszczególnych półproduktów. Specyfiką zarządzania logistycznego pewnej grupy towarów było zachowanie bezwzględnego FIFO przy jednoczesnym fakcie wydawania częściowego i zwrotów resztek do zbioru, który w tym samym czasie może przyrastać o nowe zasilenia.
Ambitne zadania
Firmy produkcyjne w warunkach potężnej konkurencji muszą szybko reagować na sygnały docierające z rynku. Dostosowanie do tych wymogów powoduje jednak szereg konsekwencji. Większa zmienność niejako wymusza krótszy horyzont planowania. Oczywistą stała się potrzeba planowania krótkoterminowego, produkowanie krótkich serii produktów, częste przezbrojenia maszyn. To spore wyzwanie dla logistyków, którzy zazwyczaj preferują duże partie jednorodnego towaru. Istniejąca sytuacja oznacza coś dokładnie odwrotnego.
Ze względu na wzrost zainteresowania produktami firmy ze strony klientów, należało dostosować zasoby do nowych warunków. Założono wzrosty wolumenów w poszczególnych zakresach, zaczęto przygotowania do przemodelowania procesów intralogistycznych uwzględniających większe przepływy towarowe. Perspektywa dalszego, służącego zwiększeniu sprzedaży, rozwoju palety produktów związana jest z wkraczaniem na nowe tereny, jak również wprowadzeniem wielowariantowości produktowej w zakresie istniejących linii. To spore wyzwanie dla logistyki.
Możliwości i korzyści.
Regały Lean-Lift z jednej strony wykorzystywały pełną wysokość pomieszczenia, z drugiej – odciążały operatorów, przy czym nie wymagały do pracy żadnych wózków. Walorem jest to, że można je dowolnie przestawiać. Same dostosowują się do wysokości towarów na półkach. Dodatkowym atutem były podobne wdrożenia w wielu firmach z branży, a także możliwość odkupienia używanych modułów przed dostawcę w razie dekoniunktury. Ważna również była możliwość stopniowego rozwijania systemu, stosownie do nowych, pojawiających się potrzeb.
Czy możliwości BURY Technologies odpowiedzą na nowe zadania rynkowe przy jednoczesnych tendencjach w kierunku oszczędności i elastyczności? To jedno z kluczowych pytań. Koniecznością stało się m.in. znalezienie rozwiązań magazynowych, które najlepiej potrafią wpasować się w zorientowane potrzeby. Ustalono, iż optymalne rozwiązanie powinno bazować na technologiach automatycznych, zapewniając przy tym należytą elastyczność i możliwości adaptacyjne w zakresie wielkości i ilości towarów. Taki wybór, dzięki zastosowaniu wysokiego składowania, potrafi znacząco oszczędzać dostępną powierzchnię. Korzyścią jest też możliwość odciążenia operatorów, by mogli skupić się na ważniejszych czynnościach, niż np. odnajdywanie lokalizacji konkretnych towarów. Istotne było również zmniejszenie udziału wózków widłowych w procesach mających miejsce wewnątrz magazynu. Dla firmy jednym z najważniejszych priorytetów stało się zastosowanie systemu modułowego, który dawałby możliwość pełnej dowolności w rozbudowie i przekształceniach części systemu.
Przeanalizowano szereg możliwości poszczególnych systemów składowania (układnice, miniload, tradycyjne regały rolkowo-przepływowe, regały Lean-Lift). Sporządzono listę plusów i minusów.
Uznano np. że regały rolkowe nie dawały możliwości szybkiego dostosowania do zmiany opakowań/warstw, nie można było zastosować wysokiego składowania, a stopień wykorzystania powierzchni okazał się niezadowalający. Z kolei układnice i miniloady pozwalały wprawdzie na wykorzystanie wysokości pomieszczenia, ale nie są elastyczne w zakresie modyfikacji systemu, jego podziału, stworzenia dwóch z jednego, sprzedaży elementów używanych.
Konkretny wybór
Fotokomórki w oknie dostępowym regału magazynowego Lean-Lift. Zapadła decyzja o zastosowaniu technologii Lean-Lift. Tylko regały tego rodzaju spełniły bowiem wszystkie postawione warunki. Z jednej strony wykorzystywały pełną wysokość pomieszczenia, z drugiej – odciążały operatorów, przy czym nie wymagały do pracy żadnych wózków. Walorem jest to, że można je dowolnie przestawiać. Same dostosowują się do wysokości towarów na półkach. Dodatkowym atutem były podobne wdrożenia w wielu firmach z branży, a także możliwość odkupienia używanych modułów przed dostawcę w razie dekoniunktury. Ważna również była możliwość stopniowego rozwijania systemu, stosownie do nowych, pojawiających się potrzeb, a bez konieczności inwestowania w cały duży system bez gwarancji, iż sprawdzi się w pełni, uwzględniając specyfikę firmy.
Podjęto też decyzję o zastosowaniu pośredniczącego oprogramowania do zarządzania zleceniami. Główną przesłanką był wysoki stopień komplikacji procesów, jak również dążenie do maksymalnego wykorzystania możliwości, jakie dają regały Lean-Lift współpracujące z oprogramowaniem ISL Innowacyjne Systemy Logistyczne, np. diodowe wskazywanie towarów (minimalizacja prawdopodobieństwa popełnienia pomyłek), realizacja wielu zleceń równocześnie (znaczne przyspieszenie kompletacji). Decyzję poprzedziło wstępne zbadanie oczekiwań firmy BURY w zakresie sposobu realizacji procesów logistycznych, które miały dotyczyć nowego systemu regałowego. Zaakceptowano wniosek dostawcy, by zamiast standardowych sterowników zapisać dedykowane oprogramowanie, dostosowane na miarę do wymagań (Taylor made).
Elementami nowego systemu są:
- sekcja magazynu SMD, wydzielony magazyn elementów elektronicznych o podwyższonych standardach ochrony, w tym elektrostatycznej (składowanie laminatów i towarów do produkcji SMD);
- pięć regałów Lean-Lift na komponenty do produkcji (ponad 6 m, przystosowane do współpracy z zewnętrznym oprogramowaniem, o podwyższonej szybkości działania, z dodatkową ochroną operatorów z uwagi na zewnętrzne sterowanie systemem;
- jeden regał Lean-Lift dedykowany do składowania narzędzi. Ze względu na odmienny tryb pracy i odmienny kształt realizowanych procesów logistycznych został on jednak wyłączony z głównego trybu sterowania przewidzianego dla zasadniczej części instalacji. W tym przypadku za optymalne uznano podstawowe oprogramowanie sterownikowe, będące podstawowym wyposażeniem regału Lean-Lift.
Wszystkie zastosowane regały ze względu na kontakt z elementami stosowanymi w elektronice są w wersji ESD (z ochroną antyelektrostatyczną).
System przyjmuje zlecenia z MRP; kolejkuje i rozdziela zadania przy poszczególnych procesach, dysponuje funkcją „hold”, wydziela poszczególne zbiory do baz zewnętrznych, zapewnia konserwację oprogramowania.
To nie koniec, ważne oprogramowanie
Ciągła optymalizacja sposobów składowania wymaga, by zasadnicza część instalacji służącej do szybkiej kompletacji półproduktów podlegała stałej optymalizacji. Dotyczy to np. wykorzystania możliwości regałów Lean-Lift (optymalne rozłożenie towarów na półce), co staje się szczególnie istotne zwłaszcza w sytuacji zmienności produktowej, a także rozmiarów i ilości półproduktów. Wynikiem są np. dynamiczne zmiany warunków i kluczy przydzielania lokalizacji, poszukiwanie najlepszego sposobu wyboru nowej lub kolejnej lokalizacji, w oparciu o ilość dostarczonych towarów, spodziewaną rotację, wyniki korelacji wydań danego towaru z wydaniami innych. Oprogramowanie pośredniczące (autorstwa ISL), które zarządza pracą regałów, stanowi jednocześnie swoisty łącznik między oprogramowaniem stosowanym w firmie BURY, a językiem maszynowym systemu regałowego. Zadaniem tego oprogramowania jest spełnienie szeregu warunków sprecyzowanych przez BURY Technologies. Zastrzeżono m.in., że takie oprogramowanie musi współpracować z oprogramowaniem zarządzającym zasobami firmy. Wymagało to ustalenia sposobów komunikacji miedzy systemami, zastrzeżenia zakresów odpowiedzialności, szczegółowego rozpisania procesów, które są realizowane zarówno przez oprogramowanie główne firmy BURY, jak i Middle-ware opracowywane przez ISL.
Regał magazynowy Lean-LiftRegał magazynowy Lean-Lift wykorzystuje dostępną wysokość pomieszczeń w podobnym stopniu, jak magazyny wysokiego składowania czy systemy wielopiętrowe. Różnica polega na tym, że system Lean-Lift dostosowuje odległości pomiędzy półkami do wysokości przechowywanych towarów, nie trwoniąc dostępnego miejsca na puste przestrzenie. Dzięki temu rozwiązaniu można wydatnie obniżyć koszty i oszczędzić powierzchnię magazynową. Regał automatyczny Lean-Lift zbudowany jest z ruchomego podajnika, którego zadaniem jest pobieranie lub umieszczanie ruchomych półek z towarem w docelowych lokalizacjach składowania wewnątrz regału. Półki mogą być umieszczane na przedniej i tylnej ścianie regału w rozmieszczonych co kilka centymetrów prowadnicach. Na poziomie operatora znajduje się okno dostępowe, w którym zlokalizowany jest zespół fotokomórek. Żądany towar wraz z daną półką jest umieszczany w oknie dostępowym, skąd operator może go wygodnie odebrać. Rolą fotokomórek jest określenie maksymalnej wysokości produktu na półce i zarezerwowanie dla niej dokładnie tyle miejsca, ile potrzebuje. W przypadku produktów o zróżnicowanej wysokości pozwala to uzyskać wysoką optymalizację i wykorzystanie miejsca, co wiąże się z redukcją wymaganej powierzchni do składowania. Półki mogą być wyciągane z regału, pełniąc funkcję palety i pozwalając na pobieranie większej ilości produktów na raz. Lean-Lift znajduje szerokie zastosowanie w przemyśle, dystrybucji, magazynowaniu, np. w działach utrzymania ruchu: części zamienne, narzędzia, matryce, magazynach komponentów i wyrobów gotowych, polach buforowych (odkładczych), pomieszczeniach specjalnych (np. laboratoriach) i wielu innych.