Continuous flow, czyli tak zwany przepływ ciągły, charakteryzuje nie tylko podejście do tematu produkcji w lean manufacturing, ale również stosunek do zapasów i ich logistyki. Ta szczególnie w swojej odmianie wewnątrzzakładowej nie lubi już przestojów jak dawniej. Teraz wszystko musi być w ruchu, wszystko płynie.
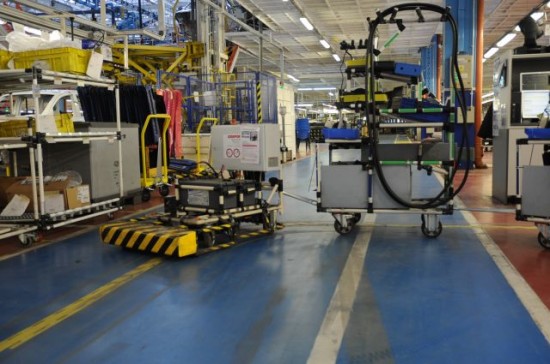
Do lamusa odeszły czasy, kiedy obszar produkcji był zawalony materiałem do produkcji. Słynny argument brygadzistów czy też kierowników produkcji, że musi stać zapas, ponieważ stanie linia, a to będzie kosztować, już nie działa. Właśnie wcześniejsze stanie zapasu kosztowało firmy zbyt dużo. Kilkutygodniowe bufory na każdej stacji roboczej powodowały, że czas transformacji od surowca do gotowego towaru trwał na linii produkcyjnej miesiącami, mrożąc tym samym kapitał zakładowy przedsiębiorstwa i narażając je na brak płynności finansowej. Teraźniejszość dla tych, co idą z duchem czasu, to niewielkie partie dostarczane bardzo często na linię produkcyjną, starczające czasami na zaledwie kilka godzin pracy. Wymogły to z jednej strony uwarunkowania ekonomiczne, a z drugiej nowoczesny sposób kreowania produkcji. Kompaktowe stanowiska pracy, gdzie pracownik na niewielkim obszarze obsługuje czasami nawet po kilka maszyn, nie zapewniają miejsca na składowanie miesiącami dużych partii towarów. Pomimo to linie produkcyjne nie stoją, a ciągłość ich pracy zapewniają im różne rozwiązania z obszaru logistyki.
Sztandarowym przykładem jest rozwiązanie dwupojemnikowe, nazywane też kanbanem dwupojemnikowym. Idea tego rozwiązania polega na tym, iż przy danym stanowisku roboczym znajdują się dwa pojemniki z tymi samymi częściami. Kiedy w pierwszym z nich się kończą części, pracownik pobiera je z drugiego, a ten pusty staje się sygnałem dla logistyki, aby go zabrać i dostarczyć kolejny pełny. W ten sposób zapewniony jest ciągły dostęp do części bez posiadania dużych zapasów przy linii produkcyjnej.
Sprawa się komplikuje, kiedy jeden pojemnik starcza na niewiele wyrobów gotowych, a tym samym czas na jego dostarczenie jest bardzo krótki. Wtedy to zwiększa się partie dostaw, biorąc pod uwagę czas zużycia części z pojemnika i odpowiedni czas na nową dostawę. W zależności od charakterystyki linii produkcyjnej dostawy starczają na godzinę, dwie, pół lub całą zmianę.
Sytuacje montowania tylko jednego podzespołu na danym stanowisku roboczym są niezmiernie rzadkie bądź prawie nie występują. W efekcie mamy do czynienia z szeregiem małych pojemników z częściami, które oczywiście najlepiej ułożyć na regale, który z zasady zatrzymuje zapas, a przecież założyliśmy, że będzie on w ruchu. Rozwiązaniem są niewielkie regały przepływowe do obsługi pojemników, bardzo rozpowszechnione w branży motoryzacyjnej. Zbudowane z systemu rurek o wysokości do dwóch metrów, bardzo często stoją na kółkach tak, aby zapewnić elastyczność i mobilność w kształtowaniu stanowiska pracy i jego otoczenia. Układ rolek w regale jest ułożony w dwóch kierunkach. Od strony drogi magazynier wkłada pełne pojemniki, które staczają się w kierunku pracownika linii produkcyjnej. Natomiast z drugiej strony wkładane są puste pojemniki, które staczają się w stronę drogi i są zabierane przez magazyniera. Dodatkowo regały przepływowe zapewniają zachowanie zasady FIFO.
Regały przepływowe na produkcji zaopatrywane nie są przez wózki widłowe, ale przez niewielkie ciągniki z podczepionymi wagonikami. Na nich umieszczone są plastikowe pojemniki z niewielkimi partiami towarów. Spotyka się też rozwiązania, gdzie całe regały podczepiane są do ciągników i zawożone na produkcję, będąc swoistą kombinacją wózka transportowego z regałem.
W wysoce zmechanizowanych fabrykach stosuje się bezosobowe systemy zaopatrzenia linii produkcyjnych. Niewielkie platformy prowadzone pętlą indukcyjną w podłodze jeżdżą bez ustanku po stałych trasach po fabryce, dowożąc pełne pojemniki, a odbierając puste. Niemieccy fani motoryzacji, będąc w Dreźnie, odwiedzając szklaną manufakturę, mają możliwość obserwowania zaopatrzenia linii produkcyjnej, gdzie z piwnicy wyjeżdżają windą części do montażu flagowych modeli jednego z największych koncernów motoryzacyjnych. Komputerowo sterowane wózki dowożą samodzielnie nie tylko drobne elementy, ale również tak spore, jak fotele.
Henry Ford, tworząc w swojej fabryce samochodów linię produkcyjną, zaplanował stałe stanowiska pracy, przypisane do jednego miejsca. Wśród ostatnich najnowszych rozwiązań stosuje się mobilne stanowiska pracy, gdzie nie tylko sam przedmiot produkcji się przemieszcza, ale również razem z nim materiał niezbędny do montażu. Niekiedy nawet sam pracownik przesuwa się razem ze wszystkim. W takich sytuacjach możemy powiedzieć, że naprawdę wszystko płynie.
Piotr Bachorz