Produkowanie według zasad Lean wymaga bezwzględnie informatyzacji procesu w celu zapewnienia pełnej informacji o zapasach, półproduktach, produkcji w toku itd. Służą do tego dedykowane systemy klasy ERP i wspierające operacje produkcyjne systemy MES. Warto jednak przyjrzeć się bliżej gospodarce zapasami i magazynowi wyrobów gotowych, aby uniknąć wąskich gardeł na wejściu i wyjściu towarów z fabryki. Tutaj pomocny okazuje się również system zarządzania magazynem klasy WMS.
Niedobór surowców do produkcji, niedostarczenie komponentów na czas, nadprodukcja, nadmiar zapasów czy wyrobów gotowych w strefie składowania na wyjściu z zakładu produkcyjnego to typowe problemy do rozwiązania na drodze do osiągnięcia statusu Lean. Informatyzacja procesu pozwala uzyskać szereg danych do analizy i identyfikacji potencjalnych źródeł problemu. Powszechnie stosowanym rozwiązaniem wspomagającym zarządzanie na poziomie strategicznym są systemy planowania zasobów przedsiębiorstwa, czyli systemy klasy ERP (Enterprise Resource Planning). Na poziomie operacyjnym pomocnym narzędziem menadżerów produkcji są aplikacje klasy MES (Manufacturing Execution System). Niewątpliwie stanowią nieodłączny element informatycznej infrastruktury dużych firm produkcyjnych. Do tego zastawu warto również dołączyć systemy WMS (Warehouse Management System), jako dedykowane rozwiązania do zarządzania magazynem, które wydatnie optymalizują gospodarkę zapasami i przyczyniają się do usprawnienia przepływu zarówno na linii produkcyjnej, jak i w końcowym etapie, na wyjściu z magazynu wyrobów gotowych.
Jednym z podstawowych zadań logistyki magazynowej w firmach produkcyjnych jest dostarczenie w odpowiednim czasie i ilości surowców, komponentów i półproduktów o wskazanych cechach i parametrach, tak aby nie zakłócić przebiegu procesu produkcyjnego, a następnie odebrać wyrób gotowy i zmagazynować go we właściwej lokalizacji lub przygotować pod kompletację do wysyłki. – Systemy WMS zapewniają nie tylko sterowanie pracą magazynów wyrobów gotowych, ale także wspierają procesy przepływu materiałów w produkcji. Wyposażenie systemu WMS w funkcjonalności sterowania zaopatrywaniem maszyn bądź gniazd produkcyjnych w surowce lub półprodukty, czy też odbiorem wyrobów gotowych, jest krokiem w kierunku integracji zarządzania magazynem z operacjami produkcyjnymi zgodnie z zasadami Lean Management – mówi Aneta Janeczko, Kierownik Projektu w firmie DataConsult.
Magazyn surowców i komponentów
Przede wszystkim zastosowanie systemu WMS w obszarze produkcji pozwala na osiągnięcie efektu Just-in-time w zakresie dostaw komponentów na linię czy gniazdo produkcyjne. – Z naszego doświadczenia wynika, że właściwa integracja systemu WMS z systemem generowania zleceń produkcyjnych umożliwia całkowite ograniczenie błędnych wydań komponentów, pozwala na pełną kontrolę faktycznego ich zużycia, a co za tym idzie – pozwala na właściwe rozliczenie produkcji – mówi Jędrzej Iglewski, Członek Zarządu HIT-Kody Kreskowe. Bardzo ważną cechą sytemu WMS na produkcji jest również możliwość śledzenia partii produkcyjnej wraz z dokładnym opisem wydarzeń, które miały miejsce podczas produkcji. – Zastosowanie systemu WMS na produkcji pozwala na jej odchudzenie. Redukujemy zapasy, wykorzystujemy tylko faktycznie potrzebne komponenty, kontrolujemy lokalizację ich składowania – dodaje Jędrzej Iglewski.
Idea odchudzonej produkcji opiera się na identyfikacji i redukcji marnotrawstwa (Muda) oraz skoncentrowaniu się na tych elementach, dzięki którym zyskuje się wartość dodaną. Niewątpliwym wyzwaniem w procesie „odchudzania” jest śledzenie zachodzących w przedsiębiorstwie zmian oraz znalezienie tych elementów, które mogą stanowić potencjalne wąskie gardła i źródło zagrożenia dla sprawności procesu. – Aby wiedzieć, co trzeba „odchudzić”, trzeba najpierw to zmierzyć. Dane i informacje rejestrowane w systemie WMS pomagają m.in. zidentyfikować i określić zbędne ruchy magazynowe i produkcyjne, okresy bezczynności ludzi, maszyn czy materiałów, nadprodukcję, zapasy bądź nadmierną rotację – przekonuje Aneta Janeczko z DataConsult. Po etapie zidentyfikowania obszarów zagrożeń system pozwala modelować scenariusze alternatywne i przetestować je z możliwością doboru odpowiednich i najbardziej korzystnych narzędzi do wsparcia oraz rozwiązań.
Konsekwentne podejście do eliminacji wszelkich przejawów marnotrawstwa radykalnie zmienia zarządzanie przedsiębiorstwem. Zapasy są na minimalnym poziomie, lub też nie ma ich w ogóle. Materiały dostarczane są w zależności od zapotrzebowania. Przez Muda należy rozumieć nie tylko nadprodukcję i nadmierne zapasy, ale także nieoptymalne przemieszczanie towaru czy marnotrawstwo czasu pracowników magazynowych. – System WMS steruje przepływem towarowym, pozwala na harmonogramowanie prac, kontroluje stany magazynowe, dając w odpowiednim czasie alerty, przydziela zasoby i optymalizuje wykorzystanie powierzchni magazynowej. Integracja z systemem produkcyjnym redukuje czas niezbędny do wprowadzania tych samych informacji w wielu systemach. Wszystko odbywa się płynnie i automatycznie, jednocześnie eliminując czynnik błędu ludzkiego – mówi Anna Kalista, Menedżer Sprzedaży w firmie Comp-Win.
Wracając do problemu optymalizacji zapasów, w wielu zakładach produkcyjnych wymaga się od systemu WMS nie tylko zarządzania stricte magazynem surowców i półproduktów, ale również buforami produkcyjnymi znajdującymi się w halach produkcyjnych. – Są one często postrzegane jako „rozszerzenie” magazynu surowców. Do takich buforów zaliczyć można bufory międzyoperacyjne, ale również bufory gniazd czy linii produkcyjnych. W takim przypadku konieczne jest także zarządzanie przepływami pomiędzy tymi buforami – przekonuje Andrzej Bobiński, Prezes Zarządu Logifact-Systems. Dla magazynów surowców/półproduktów niezwykle istotne jest, aby system WMS zarządzał cechami istotnymi dla śledzenia produkcji takimi, jak: seria, data przydatności (z uwzględnieniem jej liczenia od momentu otwarcia opakowania), dane o dostawcy i/lub producencie, posiadane certyfikaty lub zaświadczenia itp. – Zbierane dane muszą być następnie prezentowane w postaci odpowiednich raportów zdefiniowanych w systemie WMS zapewniających prześledzenie dla wskazanej porcji wyrobu gotowego z jakich surowców i półproduktów został on wytworzony – mówi Andrzej Bobiński.
Ważną kwestią dla niektórych procesów produkcyjnych, rozwiązywaną dzięki dostępnym funkcjonalnościom systemów WMS, jest możliwość składowania towarów w różnych jednostkach miary. – Na przykład jednostką miary dla przewodów elektrycznych będzie metr bieżący, dla blachy metr kwadratowy, natomiast jednostką miary dla śrub będzie po prostu sztuka. Elastyczność systemu WMS w tym zakresie pozwala na prawidłowe przygotowanie wydania towaru na produkcję – zapewnia Jerzy Danisz, WMS Center Competence Manager w PSI.
Miejsce styku
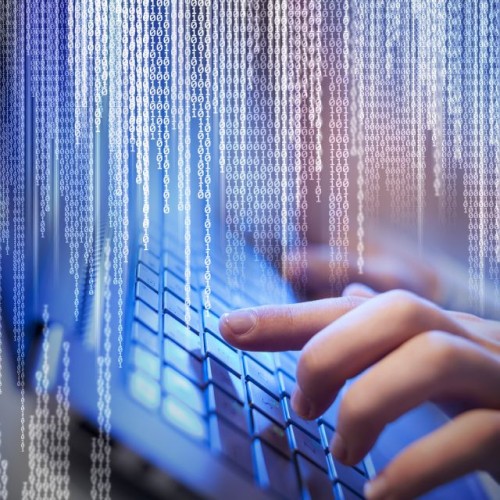
Ze względu na charakter całości procesu produkcyjnego nie ulega wątpliwości, że obszar, w którym kończą się „kompetencje” systemu WMS, a rozpoczyna się działanie systemu MES, jest momentem newralgicznym. Skuteczne zintegrowanie ze sobą miejsca styku tych aplikacji jest warunkiem zapewnienia sprawności procesu, aby mogła być zachowana zasada Lean Production. Głównym elementem wspomagającym zasady Lean jest logistyka zasilania linii, bądź gniazd produkcyjnych. – Dzięki współpracy systemu magazynowego WMS z systemem klas MES, możemy zadbać o zaopatrzenie linii produkcyjnej w surowce, materiały, półprodukty i zakupione części, przepływy tych dóbr pomiędzy kolejnymi etapami przetwarzania oraz przekazywanie wykonanych wyrobów gotowych do magazynów. Możliwe jest określenie miejsca składowania towarów dla maszyny oraz jej punktów wejścia i wyjścia – mówi Maciej Wojtkowiak, Starszy konsultant handlowy systemu MES/APS w firmie Quantum Software. Zdaniem naszego rozmówcy dzięki takiemu rozwiązaniu cały czas posiadamy informacje o stanach magazynowych na produkcji i możemy optymalizować wielkość zapasu oraz zminimalizować zbędne ruchy wózków widłowych. Ważne jest też to, że obszary, linie lub gniazda produkcyjne otrzymują niezbędny surowiec do produkcji w sposób płynny w momencie ich rzeczywistego zapotrzebowania.
Podstawowym elementem systemu WMS pomagającym wspierać magazyny przyprodukcyjne jest jego integracja z systemami planowania produkcji. Pozwala to na minimalizację stanów magazynowych oraz automatyczne generowanie zleceń wydania towaru na produkcję. – Nowoczesne systemy WMS wyposażone są w mechanizmy automatycznego odtwarzania lokacji na produkcji zgodnie z zasadą Kanban. Każde stanowisko w hali produkcyjnej posiada miejsce składowania komponentów lub półproduktów. System WMS na podstawie zdefiniowanych wartości minimalnych generuje zlecenia na magazynie w celu odtworzenia stanów na produkcji. Tego typu rozwiązania niwelują ryzyko powstawania przestojów na produkcji – wyjaśnia Jerzy Danisz.
Magazyn wyrobów gotowych
Po drugiej stronie procesu magazyn wyrobów gotowych należy zorganizować w taki sposób, aby zapewnić efektywne gospodarowanie przestrzenią, właściwy czas realizacji zamówień zewnętrznych i eliminację pomyłek. Zarządzanie magazynem wyrobów gotowych odbywa się w sposób zależny od wymagań i oczekiwań konkretnych branż. – Dla niektórych ważna jest kontrola daty przydatności czy data przechowywania, dla innych kluczowe znaczenie ma kontrola partii, jeszcze inni zarządzają magazynem przy zachowaniu reguły FIFO lub LIFO – wyjaśnia Jędrzej Iglewski (HIT-Kody Kreskowe). – Profesjonalne systemy magazynowe umożliwiają połączenie bardzo wielu strategii zarządzania magazynem wyrobów gotowych, np. pod kątem odbiorców czy grup produktowych. Właściwa konfiguracja systemu zależy od wyników analizy przedwdrożeniowej – dodaje.
Proces wyjścia z magazynu w wielu przypadkach stanowi „wąskie gardło”, które bez odpowiedniej organizacji i wsparcia funkcjonalnym narzędziem może spowodować straty jakościowe (oznaczające np. dłuższy czas realizacji zamówień czy błędy w kompletacji) i wydajnościowe (np. ilość obsłużonych wydań w ciągu godziny czy ilość zrealizowanych pozycji zleceń w jednostce czasu dla poszczególnych magazynierów), co przekłada się na koszty i wymierne straty finansowe. W związku z tym kluczową korzyścią z zastosowania WMS-a jest wsparcie procesu kompletacji zamówień. – System klasy WMS w sposób automatyczny lub półautomatyczny (priorytety zadań) planuje i rozdziela pracę operatorów w magazynie. WMS zna rzeczywisty stan każdej lokalizacji magazynowej, co pozwala na umiejętne kierowanie magazyniera, np. według ścieżki kompletacji podczas wydania – wyjaśnia Aneta Janeczko z DataConsult. – Wpływa to na zmniejszenie czasów realizacji zadań, co przekłada się bezpośrednio na zwiększenie wydajności pracy, umożliwiając realizację tego samego strumienia materiału mniejszą ilością ludzi i środków, niż w przypadku braku systemu WMS w magazynie. Dzięki poprawie wydajności pracy możliwe jest zwiększenie przepływu materiału w magazynie bez konieczności ponoszenia dodatkowych kosztów – dodaje.
Niedobór surowców do produkcji, niedostarczenie komponentów na czas, nadprodukcja, nadmiar zapasów czy wyrobów gotowych w strefie składowania na wyjściu z zakładu produkcyjnego to typowe problemy do rozwiązania na drodze do osiągnięcia statusu Lean.
Często zdarza się, że obszarem niedostatecznie docenianym pod względem ukształtowania funkcjonalno-przestrzennego w magazynie jest bufor wyjściowy. Traktowany jako jednorodna funkcjonalnie strefa może – w wyniku dużej liczby różnorodnych zleceń kompletowanych w różnych strefach magazynowych – generować problemy lub co najmniej stanowić tę część magazynu, w której pozostaje niewykorzystany potencjał do optymalizacji. W tym zakresie system WMS oferuje możliwość złożonego zarządzania buforami wyjściowymi, którą wyjaśnia Andrzej Bobiński z Logifactu. – Na przykład funkcja systemu zarządzania pojedynczym miejscem paletowym w buforze wyjścia pozwala na to, że do skompletowanej i odłożonej w określonym adresie jednostki wysyłkowej WMS można dołożyć kolejną porcję produktu, np. gdy kompletacja jednego zlecenia dokonywana jest równolegle przez dwóch lub więcej pracowników – tłumaczy nasz ekspert. – Zarządzanie pojedynczym miejscem w buforach wyjściowych jest również bardzo przydatne w przypadku, gdy istotna jest kolejność załadunku. Palety mogą stać w różnych miejscach bufora (tak jak napływały), a system podaje pracownikowi adresy pobrania uporządkowane w kolejności załadunku – dodaje. Zdaniem naszego rozmówcy bardzo istotną funkcjonalnością związaną z przepływem na wyjściu jest możliwość konsolidowania zgromadzonych w buforach wyjściowych jednostek wysyłkowych w jednostki transportowe, czyli takie, które są zaplanowane dla załadunku do konkretnego środka transportu. – Jest to kluczowe w bardziej złożonych systemach, gdy kompletacja realizowana jest w różnych strefach, np. część towaru do wysyłki jest przywożona z strefy półkowej na antresoli, gdzie do kartonów kompletowane są drobne produkty, część skompletowana jest na paletach mieszanych, a część to towary gabarytowe. Funkcjonalność ta pozwala na znaczne zwiększenie wydajności procesu przy mniejszym nakładzie pracy w stosunku do sterowania manualnego – przekonuje Andrzej Bobiński.
Podobnie jak w przypadku magazynu półproduktów, także w przypadku magazynu wyrobów gotowych niezwykle istotna jest pełna integracja systemu WMS z systemami planowania produkcji. System zarządzania produkcją może w takim przypadku generować awizację do systemu WMS w momencie zejścia towaru z linii produkcyjnej, co z kolei przyspiesza proces przyjęcia towaru na magazyn. – W przypadku całego sektora produktów żywnościowych towary schodzące z produkcji z reguły muszą podlegać kwarantannie do czasu zakończenia badań laboratoryjnych i zwolnienia partii. System WMS powinien brać pod uwagę okres karencji oraz śledzić numer partii produkcyjnej dla wyrobów gotowych. Pozwala to na pełną kontrolę wydań oraz ułatwia ewentualne wycofanie partii towaru z rynku – obrazuje Jerzy Danisz z PSI.
Szczupłe WMS-y
Oferowany przez BCS Polska system magazynowy Accellos One Warehouse nadzoruje przepływ produktu lub jednostki logistycznej od chwili przyjęcia, przez cały czas jej przebywania w magazynie, aż do momentu wydania. Umożliwia ciągły dostęp do informacji o produkcie, przez co stanowi zaawansowane narzędzie wspomagające planowanie i ograniczenie zbędnych zapasów. Dzięki współpracy z urządzeniami mobilnymi znacząco skraca czas realizacji procesów, usprawniając i optymalizując w ten sposób pracę całego magazynu. System Accellos WMS pozwala na ustandaryzowanie pracy na magazynie, przez co staje się ona bardziej wydajna, a błędy zostają ograniczone do minimum.
Wsparcie logistyki wewnętrznej zakładów produkcyjnych systemem ExpertWMS® firmy DataConsult wiąże się z zapewnieniem optymalnej koncepcji zarządzania przepływem materiałów w firmie przy wykorzystaniu zasady Lean Production. ExperWMS® wspiera i eliminuje marnotrawstwo w postaci m.in.:
- nadprodukcji, gdyż zintegrowanie ExpertWMS® z systemem produkcyjnym lub nadrzędnym (ERP) daje możliwość produkcji bezpośrednio pod zamówienie klienta oraz kalkulacji wielkości produkcji wraz z natychmiastowym planowaniem kompletacji i wysyłek;
- nadmiernych zapasów, ponieważ system wspomaga podejmowanie decyzji w obszarze optymalizacji zapasów, opiera się na automatyzacji procesu ich uzupełniania. Pozwala na bieżące monitorowanie struktury zapasów, wskaźników pokrycia popytu zapasem magazynowym oraz na generowanie prognoz statystycznych i ich weryfikację;
- oczekiwania, system umożliwia zarządzanie pracą operatorów w czasie rzeczywistym, eliminując długie okresy bezczynności ludzi, informacji lub materiałów, niewłaściwe przepływy i długie cykle produkcyjne.
Z kolei oferowane przez HIT-Kody Kreskowe systemy umożliwiają kontrolę logistyki produkcyjnej w firmach każdej wielkości i o każdym stopniu skomplikowania procesowego. – Nasze systemy działają zarówno w branży Automotive, sterując kompletacją sekwencyjną, jak i w mniejszych firmach branży poligraficznej, sterując i kontrolując logistykę produkcji niskonakładowej. System WMS jest zawsze łącznikiem pomiędzy systemem generowania zleceń produkcyjnych, a tym, co faktycznie dzieje się w obrębie dostaw komponentów, rozliczania ich zużycia czy przyjęć na magazyn – mówi Jędrzej Iglewski. Wdrożenie systemu WMS przyczynia się do znacznego odchudzenia produkcji poprzez zwiększenie kontroli nad zużyciem komponentów, optymalizację czasu ich dostaw na gniazda produkcyjne, zwiększenie kontroli nad przebiegiem produkcji oraz właściwą organizację magazynu wyrobów gotowych.
System logifact®WMS wspomaga bezpośrednie zarządzanie procesami magazynowymi i produkcyjnymi w czasie rzeczywistym, zapewniając integrację obszarów produkcyjnych i magazynowych w procesach przepływu materiałów, zapewniając jednolite środowisko zarządzania i eliminując dzięki temu bariery na styku magazyn–produkcja. Tym samym zapewnia zintegrowane zarządzanie ogółem procesów przepływu ładunków z uwzględnieniem surowców, półproduktów, wyrobów gotowych czy opakowań. Przy zastosowaniu systemu oznakowania kodami kreskowymi oraz terminali radiowych, w oparciu o pełny nadzór i rejestrację zadań transportowych, system zapewnia transparentność przeprowadzanych operacji i dostarcza on-line wiarygodnych informacji o:
- stanie zapasów w magazynach surowców/półproduktów, wyrobów gotowych oraz buforach produkcyjnych (zapasy w toku);
- przepływach ładunków w magazynach i na produkcji;
- zużyciu dostarczonych materiałów produkcyjnych, powstającej produkcji, niewykorzystanych surowcach przeznaczonych do zwrotu do magazynu, odpadach użytkowych itp.;
- efektywności pracy operatorów.
Jak deklaruje Jerzy Danisz z firmy PSI Produkty i Systemy Informatyczne, system PSIwms został z sukcesem wdrożony w dziesiątkach firm produkcyjnych na terenie całej Europy. – Fakt, że system PSIwms chętnie wykorzystywany jest przez firmy produkcyjne, wynika przede wszystkim z jego skalowalności oraz elastyczności – przekonuje nasz rozmówca. Dodatkowo system PSIwms posiada szereg rozwiązań dedykowanych branży produkcyjnej: implementacja listy materiałów BOM, możliwość składowania surowców w różnych jednostkach miary czy automatyczne odtwarzanie lokacji na produkcji zgodnie z zasadą Kanban. Jednak głównymi zaletami oferowanego przez PSI rozwiązania jest pełna integracja systemu z automatyką magazynową z jednej strony oraz z systemami zarządzania produkcją – z drugiej.
Michał Klecha
***
Funkcjonalna marszruta
– Systemy WMS mają możliwość przydzielania zadań magazynierom. Pozwala to na efektywne planowanie i zarządzanie ich pracą oraz minimalizację czasu oczekiwania na wydanie towaru.
Bardzo popularna w wielu systemach WMS jest funkcjonalność marszruty, czyli ścieżki zbierania towarów przez magazyniera. Zaawansowany algorytm systemu WMS wylicza najszybszą możliwą trasę według zdefiniowanych parametrów, np. układu regałów w magazynie, rozmieszczenia lokalizacji kompletacyjnych, wielkości towarów itp. Dzięki wbudowanym funkcjom analitycznym możliwe jest porównywanie efektywności pracy magazynierów. Spotkaliśmy się z przypadkami, gdzie najlepszy magazynier był siedmiokrotnie bardziej wydajny od najmniej efektywnego. Dzięki systemowi WMS firma przeanalizowała, z czego wynika ta różnica i przeszkoliła całą obsługę magazynu z metod pracy najlepszego pracownika.
Jakub Bieszke
Starszy konsultant
INSOFT CONSULTING Sp. z o.o.
Starszy konsultant
INSOFT CONSULTING Sp. z o.o.
Kontrola Jakości
– Niepoprawnie zorganizowany obszar wejścia może stanowić wąskie gardło w procesach magazynowych. Zadaniem systemów klasy WMS jest precyzyjna kontrola jakości i ilości pojawiających się na wejściu pojedynczych jednostek logistycznych z równoczesnym ich ewidencjonowaniem oraz znakowaniem etykietami logistycznymi (o ile jest to konieczne). Każda tak skontrolowana jednostka stanowi odrębny obiekt, któremu algorytmy przydziału lokacji automatycznie poszukują stosownego miejsca składowania, spełniającego najlepsze możliwe kryteria. Cały proces, w celu jego usprawnienia, powinien być wspierany przez szeroko rozumiane urządzenia automatycznej identyfikacji.
Tomasz Mandziej
Dyrektor handlowy
Quantum Software
Dyrektor handlowy
Quantum Software