Menadżerowie odpowiedzialni za planowanie produkcji muszą sprostać licznym wyzwaniom. W ich pracy nakładają się na siebie złożoność całego procesu planowania oraz silna presja finansowa, organizacyjna i rynkowa. Planowanie zleceń produkcyjnych w środowisku licznych ograniczeń może być narzędziem skutecznie działających przedsiębiorstw.
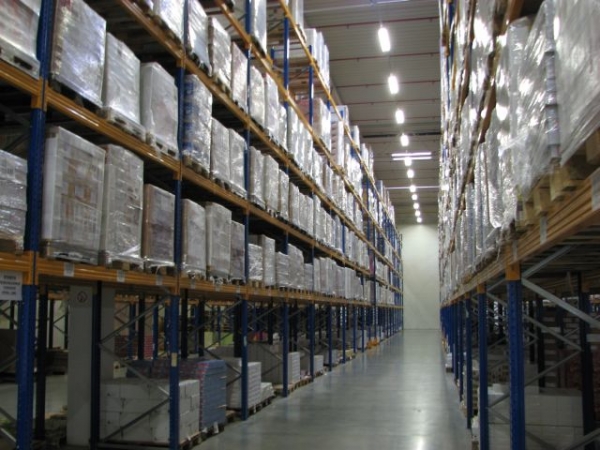
Coraz częściej przedsiębiorstwa zmieniają okresy planowania z tygodniowego na harmonogramowanie dzienne, godzinowe, a czasami jeszcze dokładniejsze. Wydaje się to na pierwszy rzut oka dość akademickie podejście, ale jeśli linia produkcyjna głównego klienta jest zlokalizowana kilkaset metrów od naszej fabryki, to nie jest łatwo mu wytłumaczyć, że nie może zmienić naszego planu produkcji na kolejnej zmianie. Nawet jeżeli konieczność tej nagłej zmiany wynika z niedoskonałości jego procesu planowania, to przecież ma rację. Wymagania dotyczące elastyczności procesu harmonogramowania oczywiście nie powodują zmniejszenia nacisku na obniżenie kosztów. Kluczowa okazuje się również szybka reakcja na wszelkie zmiany: wspomnianego już popytu, dostępności surowców i parku maszynowego. Kolejnym elementem jest właściwe dobranie personelu do faktycznych potrzeb oraz integracja planowania produkcji z zadaniami działu utrzymania ruchu (przeglądy, wyłączenia itd.).
Przekleństwo arkusza kalkulacyjnego
O ile rynek systemów ERP możemy uznać w Polsce za dojrzały (wiedza użytkowników i doradców, dostępność konsultantów, praktyki kontraktacji i implementacji systemów) oraz nasycony, o tyle rynek systemów APS (Advanced Production Scheduling) nadal mocno się rozwija. Firmy stosują uniwersalne narzędzia wspomagające układanie harmonogramów (arkusze kalkulacyjne) oraz najprostsze metody układania harmonogramu, np. harmonogramowanie w przód/harmonogramowanie wstecz wzbogacone o specjalistyczną wiedzę i doświadczenia planistów. Procesy te często nie uwzględniają w ogóle kontroli materiałowej lub stosują uproszczone rozwiązania w tym zakresie. Złożoność procesu harmonogramowania już w średnio skomplikowanych procesach produkcyjnych zmusza planistów do ograniczenia harmonogramowania tylko do wybranych poziomów w strukturze złożenia produktu (Bill Of Material). Uniwersalne narzędzia, jakim są arkusze, nie pozwalają na śledzenie zależności pomiędzy poziomami złożenia produktu. Dodatkowo, mała znajomość udanych wdrożeń systemów APS w Polsce (a jest ich sporo) jest pożywką dla publikacji na ich temat opartych na źródłach niemających nic wspólnego z praktyczną wiedzą.
Jeżeli chodzi o środowiska systemowe, to są one pochodną stosowanych mniej lub bardziej specjalizowanych narzędzi i sprowadzają się do jednego z poniższych modeli:
- w najprostszych środowiskach arkusz kalkulacyjny zasilany jest jedynie informacjami podstawowymi z systemu ERP albo nawet jest całkowicie odrębny od systemu głównego;
- w bardziej zaawansowanych środowiskach zamodelowane arkusze planistyczne bazują na danych z przebiegów MRP wykonanych w systemach ERP. Wynik kalkulacji MRP po imporcie do arkuszy i ręcznych czynnościach planistów wykorzystujących i wiedzę, i doświadczenie.
- firmy wykorzystujące funkcjonalności systemu ERP (plan główny, MRP, CRP) plus APS.
Rzadko spotykamy się z sytuacją zastosowania specjalistycznych narzędzi harmonogramujących. Wynika to z kilku czynników. Jeden z nich jest rezultatem niedostatecznej świadomości menadżerów o potencjalnych korzyściach z wdrożenia systemu klasy APS. Co ciekawe, trudność w zmierzeniu efektywności bieżącego modelu harmonogramowania, a przez to brak świadomości strat generowanych w wyniku niedoskonałego sposobu harmonogramowania, nie jest czynnikiem sprzyjającym gwałtownemu rozpowszechnieniu systemów APS. Na pytanie, który z ułożonych harmonogramów jest najlepszy, nie można odpowiedzieć, bo zwykle czasu wystarcza na ułożenie jednego. Zatem jest na pewno najlepszy. Do definicji „najlepszy” dochodzi się w następnym kroku. W procesie wdrażania APS nazywamy ten moment warsztatem na temat kryteriów oceny harmonogramu.
Ostatnio obserwujemy duże inwestycje ze strony dostawców w moduły planowania i harmonogramowania produkcji, często dostarczane łącznie z modułami prognozowania sprzedaży i zarządzania łańcuchem dostaw. Najwyraźniej zapadły decyzje, aby skomplikowane moduły przestały być czarnymi skrzynkami, generującymi informacje trudne do zweryfikowania pod względem ich pochodzenia i pozwoliły analizować swoje algorytmy.
Jeżeli zarząd firmy dojdzie do wniosku, że procesy planowania i harmonogramowania należy wesprzeć technologią informatyczną, to pierwszym i naturalnym adresatem takiego tematu jest dostawca wykorzystywanego systemu ERP. I tu okazuje się, że w ogromnej większości dostawcy nie mają w swojej ofercie tego typu rozwiązań, a z wiedzą wdrożeniową nie jest najlepiej. Najwięksi, globalni, dostawcy systemów wspomagających zarządzanie oferują takie rozwiązania, ale bariery zakupu są na tyle wysokie, że popularność ich modułów jest niewielka. Ostatnio obserwujemy duże inwestycje ze strony dostawców w moduły planowania i harmonogramowania produkcji, często dostarczane łącznie z modułami prognozowania sprzedaży i zarządzania łańcuchem dostaw. Najwyraźniej zapadły decyzje aby skomplikowane moduły przestały być czarnymi skrzynkami, generującymi informacje trudne do zweryfikowania pod względem ich pochodzenia i pozwoliły analizować swoje algorytmy. Takie prozaiczne przyczyny, jak problem z możliwością sprawdzenia krok po kroku, jakich obliczeń dokonuje oprogramowanie, stały się w kilku przypadkach główną przyczyną porażek wdrożeń. Jeśli dołożymy do tego niewielkie, jeszcze kilka lat temu, doświadczenie konsultantów to faktycznie okaże się jasne, że wyzwania wdrożeń mogły okazać się zbyt ambitne. Z naszego doświadczenia wynika, że kompetencyjna bariera wejścia w obszar APS nawet dla doświadczonych konsultantów obszarów produkcji w ERP jest bardzo wysoka. Kilka lat pracy, najlepiej w doświadczonym zespole i kilku cierpliwych klientów – oto co powinno się zdarzyć na początku drogi zawodowej konsultanta APS.
Pozostali, mniejsi dostawcy ERP zarówno globalni, jak i lokalni (z nielicznymi jednak istniejącymi wyjątkami) oferują zwykle rozwiązania wspomagające harmonogramowanie w podstawowym zakresie. Są to proste produkty niemające cech systemów APS, jedynie pomagające planistom poprzez proste metody harmonogramowania, wizualizację obciążenia zasobów itd. Ich zastosowanie co prawda pomaga w utrzymaniu spójności danych (w przeciwieństwie do rozwiązań opartych na arkuszach kalkulacyjnych dane są cały czas w głównym repozytorium ERP), jednak nie wprowadza jakościowej zmiany w systemie harmonogramowania. Część z nich dostarczana jest w ramach opieki serwisowej bez opłat licencyjnych, co zachęca do podjęcia próby wdrożenia. Często jednak moduł niegenerujący przychodu z licencji nie ma dostatecznego wsparcia konsultacyjnego u dostawcy.
Zapanować nad wskazówkami zegara
Zauważalnym trendem w obszarze kryteriów planowania produkcji jest nacisk na czas dostaw. Jest to zrozumiałe i odzwierciedla zmiany w priorytetach firm wytwórczych. Zawsze bardzo ważny – szczególnie dla rynku polskiego, określanego jako „wrażliwy cenowo” – był aspekt kosztowy. Firmom zależało na utrzymaniu niskiego kosztu wytworzenia. Tu oczywiście nic się nie zmieniło – presja cenowa jest cały czas mocna, jeśli nie mocniejsza niż kiedyś. Wraz z ogólnym rozwojem, tradycyjnie wysokimi wymaganiami odbiorców zagranicznych, jak i ciągle rosnącymi standardami oczekiwań na rynku wewnętrznym, jakość stała się kolejnym kluczowym warunkiem sukcesu dla wytwórców. Czas dostaw to czynnik krytycznie wpływający na konkurencyjność wytwórców. Wskazane czynniki są ze sobą w naturalny sposób mocno powiązane. Paradoksalnie, wytwórca niedotrzymujący oferowanych standardów jakości i terminów dostarczenia, praktycznie nie może osiągać niskich kosztów wytworzenia. Dzieje się tak dlatego, że występują dodatkowe koszty kontroli jakości, koszty poprawek, specjalnych szybkich wysyłek dla zmniejszenia spóźnień itd. Wysoki poziom terminowości dostaw jest zatem koniecznym warunkiem dla wysokiej konkurencyjności.
Jednak są branże szybciej rotujące, gdzie krótki czas dostawy jest ważny. Przedsiębiorcy wydają się nie doceniać, jak wielkie korzyści może im przynieść skrócenie czasu dostaw dla klienta (rozumianego jako czas od zamówienia do dostarczenia towaru). Oprócz oczywistego argumentu handlowego „oferuję krótszy czas dostawy od mojej konkurencji”, skrócenie czasu dostaw to zmniejszenie kosztów produkcji. Cały proces produkcji to przecież: gromadzenie surowców, przygotowanie produkcji, wytwarzanie i przesuwanie go oraz magazynowanie i dostarczenie. Wszystkie fazy to kosztotwórcze procesy, których skrócenie skutkuje obniżeniem naszych kosztów. Producenci podejmują różne działania przeorganizowujące produkcję, służące skróceniu czasu faz okołowytwórczych: techniki SMED, kompaktowe rozmiary hal, optymalne ustawienie maszyn i odpowiednie wielkości partii itd. Wszystkie te działania poprawiają przepływ materiałowy przez firmę, w efekcie ograniczając czasy. Jednak wielkość kolejek, jakie tworzą się na hali produkcyjnej, to efekt nie tylko organizacji produkcji, ale też kolejności wykonywania zadań. Ilość możliwych sekwencji i środowisko ograniczonych zasobów powoduje, że w zależności od jakości harmonogramowania zadań możemy uzyskać bardzo różne rezultaty w przepływie materiałów. Coraz większa zmienność produkcji oraz wysoka utylizacja parku maszynowego powoduje, że optymalne harmonogramowanie staje się coraz trudniejsze. Prowadząc w roku 2002 projekt wdrożenia APS Preactor w przedsiębiorstwie branży elektronicznej, z podziwem obserwowałem dokładnie sprecyzowane cele wdrożenia APS. Było one konsekwentną kontynuacją osiągniętych celów wdrożenia systemu ERP, które przyniosło między innymi spadek zaangażowania kapitałów właścicieli w firmę. Przed wdrożeniem APS postawiono już zupełnie inne cele operacyjne. Jednym z nich było uwiarygodnienie terminów dostaw. Nie skrócenie, ale uwiarygodnienie. Dla niektórych asortymentów uległy one nawet wydłużeniu, ale klienci byli informowani o terminie przed potwierdzeniem zamówienia, a wskaźnik terminowości dostaw poszybował w górę, wraz z premiami osób za to odpowiedzialnych.
Firmy stosują uniwersalne narzędzia wspomagające układanie harmonogramów. Procesy te często nie uwzględniają w ogóle kontroli materiałowej lub stosują uproszczone rozwiązania w tym zakresie.
Terminowość, rozumiana jako sama data czy też godzina dostawy, może nie być problemem dla FMCG i produkcji jednostkowej. Szczególnym wyzwaniem jest dla nich synchronizacja zleceń/operacji wewnątrz własnego łańcucha produkcyjnego oraz synchronizacja z niższym poziomem łańcucha – dostawcy. Kolejny problem wynika wprost z ilości informacji do ogarnięcia (zwłaszcza kontrola materiałowa). Pojawiają się dodatkowe ograniczenia w postaci dostępnych w danej chwili narzędzi, form (np. wtryskarki) czy personelu (pod względem ilości lub posiadanych kwalifikacji). Ostatecznie, wyzwaniem jest również konieczność częstej zmiany harmonogramów wynikająca z jakichkolwiek zakłóceń.
Wyzwania planistów w sytuacji zmian
Firma Valmont, międzynarodowy lider w produkcji konstrukcji stalowych, usług dla przemysłu i systemów irygacyjnych dla rolnictwa, wdrożyła system Preactor klasy APS w celu uporządkowania procesów związanych z planowaniem produkcji. Kierownictwu firmy zależało również na możliwości sprawnej i przejrzystej obserwacji efektów zmian zachodzących w planie produkcji.
Spółka działa w warunkach bardzo silnej konkurencji, dlatego szczególnym wyzwaniem było skrócenie czasu odpowiedzi do klienta i precyzyjne zdefiniowanie daty dostarczenia zamówienia. Firma oferuje pełne portfolio produktów realizowanych w modelu „designed-to-order”, zakładającym pełne dostosowanie zamówienia do potrzeb i specyfikacji klienta, co wiąże się również z koniecznością potwierdzenia terminu finalnej realizacji. Valmont wyróżnia na rynku bardzo elastyczne reagowanie na potrzeby i konkretne zamówienia klientów. Śledzenie konsekwencji zmian w planie, dzięki symulacjom wyglądu zamówień, stanowi dla nas kluczową wartość systemu Preactor APS. Sebastian Borowik, Dyrektor Zakładu Valmont, podkreśla, że już po 2 miesiącach od wprowadzenia rozwiązania firma uzyskała przejrzysty obraz zmian.
W przypadku takich firm, jak Valmont, które realizują dostawy konstrukcji stalowych na place budowy, bardzo istotna jest doskonała koordynacja dostaw. Ze względu na brak miejsca składowania większych elementów, konieczne jest zachowanie uzgodnionych terminów. W innym przypadku może to zaburzyć, a nawet wstrzymać prace budowlane. Stanowi to duże wyzwanie dla menadżerów odpowiedzialnych za terminy dostaw u producenta elementów stalowych na zamówienie.
W celu usprawnienia procesu układania harmonogramu i poprawy realizacji terminów zamówień w Valmont, firma DSR wdrożyła autorskie rozwiązanie planistyczne zakładające wykorzystanie tzw. technologii/marszrut fantomowych. Polega ono na wprowadzeniu do harmonogramu produkcji wirtualnego zamówienia, rozwinięciu go z wykorzystaniem technologii fantomowej i umieszczeniu w harmonogramie. Efektem tego jest bardziej precyzyjna informacja o planowanym terminie wykonania zlecenia. Dzięki temu dział sprzedaży jest w stanie przekazać klientowi dokładne informacje, kiedy otrzyma gotowy produkt.
Kolejnym założeniem projektu była redukcja czasu wytworzenia wyrobu (lead time) od wpłynięcia zamówienia, aż po wysyłkę do klienta. Kierownictwo przedsiębiorstwa zwracało również uwagę na zwiększenie efektywności produkcji poprzez optymalizację liczby przezbrojeń. Sebastian Borowik zwraca uwagę, że dzięki lepszej wizualizacji danych, łatwiej i dokładniej można analizować portfel zamówień. W ten sposób firma z wyprzedzeniem reaguje na popyt i może lepiej dostosować moce produkcyjne do zgłaszanych zamówień.
Przed wdrożeniem rozwiązania Preactor, firma nie dysponowała jednym systemem odpowiedzialnym za przekazywanie informacji do całej firmy, w tym działu technologicznego, zaopatrzenia, produkcyjnego i sprzedażowego. Poszczególne działy mają teraz dostęp do raportów generowanych przez program, co znacząco ułatwia i optymalizuje cały proces produkcyjny. Planowanie uwzględnia zatem nie tylko część produkcyjną, ale również administracyjną. System usprawnił obsługę dokumentacji wydziałowej i technicznej, minimalizując ilość dokumentów w obiegu. Workflow został całkowicie przeprojektowany, co pozytywnie wpłynęło na efektywność całego procesu.
Jak pokazały doświadczenia z projektu, system APS nie stanowi tylko narzędzia do planowania produkcji, ale daje możliwość spojrzenia na całą organizację. W ten sposób pomaga w wyborze konkretnych kierunków działań biznesowych. – Traktujemy system APS jako narzędzie zarządcze, pozwalające podejmować trafne decyzje. Dostrzegamy szanse jego dalszego rozwoju nie tylko w obszarze poprawy precyzji planowania produkcji, ale również innych zasobów organizacji – mówi dyrektor zakładu.
Piotr Rojek
Dyrektor Zarządzający
DSR
APS: jak się do tego przygotować?
Firma planująca wdrożenie systemu APS powinna uwzględnić między innymi następujące zagadnienia:
- cele wdrożenia APS, a wcześniej cele stojące przed zmianami w procesie planowania produkcji (PO CO?);
- stopień uproszczeń zastosowanych reguł w stosunku do ich optymalnej postaci. Generalnie wprowadzanie uproszczeń obniża jakość wyników APS, z drugiej strony osiągniecie całkowitej 100 proc. automatyzacji harmonogramowania może okazać się kosztowne i długotrwałe (JAK?);
- integracja z posiadanymi systemami (MES, ERP) – informacja aktualna, prawdziwa i obejmująca nie tylko jeden moment w czasie, ale również przyszłość (dostawy, sprzedaż) (Z CZYM?);
- automatyzacja powtarzalnych czynności wykonywanych przez planistę (kontrola materiałowa), aktualizacja o wykonanie harmonogramu (JAK AUTOMATYCZNIE?)
- wykorzystanie zaawansowanych reguł harmonogramowania (min. przezbrojeń) lub w skomplikowanych środowiskach stworzenie własnych, które przygotują wstępną wersję harmonogramu, którą planiści skorygują na bazie doświadczenia i informacji nieznajdujących się w żadnym systemie (JAK SKOMPLIKOWANIE?).