Pytanie "Lean Assessment – moda czy potrzeba biznesowa?" co najmniej od kilku lat nurtuje przedstawicieli kadry zarządzającej organizacji produkcyjnych. Rodzime firmy produkcyjne od lat, o ile nie od dziesięcioleci, adoptują oraz wdrażają strategiczne praktyki, narzędzia i metody „szczupłego zarządzania”, wszystko po to, by podwyższać jakość, poprawiać produktywność, redukować koszty wytwarzania, a w efekcie, w długim okresie. uzyskać przewagę konkurencyjną na rynku.
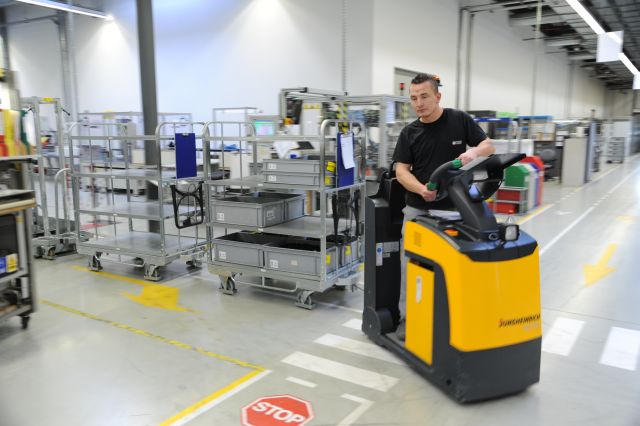
Zastosowanie metod i narzędzi lean w praktyce niejednokrotnie przynosi oczekiwane efekty, jednak, jak wskazują realia biznesowe, pojawiają się kolejne przykłady organizacji, które oprócz stosowania narzędzi i metod lean, decydują się na regularne mierzenie dojrzałości stosowanego systemu wytwarzania. Przykładem może być tu FIAT, VOLVO, Bombardier, czy też Wielkopolski oddział Phoenix Contact.
Lean Assessment, z założenia, ma służyć regularnemu diagnozowaniu poziomu dojrzałości oraz efektywności stosowanych metod wytwarzania na zgodność z zasadami lean manufacturing. Warto pamiętać, że miara (wynik) assessmentu nie jest jednak celem samym w sobie, jest nim na pewno identyfikacja obszarów do doskonalenia organizacji, dzięki porównaniu stanu obecnego („as is”) ze stanem docelowym („should be”), wynikającym ze standardów oraz oczekiwań stawianych audytowanej organizacji przez spółkę-matkę.
Stosowana w praktyce częstotliwość assessmentów to przeważnie 6 bądź 12 m-cy. Praktyka pokazuje również, że zakres assessmentu bywa bardzo zróżnicowany, począwszy od oceny jakości, dojrzałości oraz efektywności stosowanego systemu wytwarzania, poprzez diagnozę efektywności wykorzystania zasobów ludzkich, badanie stopnia dodawania wartości w organizacji czy też audyt kultury organizacyjnej.
W dalszej części niniejszego artykułu przedstawione zostanie studium przypadku dotyczące procesu planowania, przygotowywania oraz realizacji Lean Assessment Systemu Ciągłego Doskonalenia Phoenix Contact Wielkopolska.
Grupa Phoenix Contact, założona w latach 20 tych ubiegłego wieku w Essen, obecnie z siedzibą w Blomberg, Niemcy, posiada ok.50 zagranicznych oddziałów, z których jednym jest organizacja Phoenix Contact Wielkopolska, z siedzibą w Nowym Tomyślu. Grupa specjalizuje się w wytwarzaniu produktów, systemów i rozwiązań z zakresu elektrotechniki i automatyki przemysłowej, stale utrzymując pozycję lidera w branży. Kluczowe grupy produktów Phoenix Contact Wielkopolska to uniwersalne złącza przemysłowe (CLIPLINE), złącza do płytek drukowanych (COMBICON) oraz złącza do okablowania obiektowego (PLUSCON).
Oddział w Nowym Tomyślu funkcjonuje na rynku ponad 20 lat, obecnie zatrudniając nieco ponad 2000 pracowników. Z początkiem roku 2014, na podstawie autonomicznej, niezależnej od centrali w Blomberg decyzji Kadry Kierowniczej Phoenix Contact Wielkopolska, rozpoczęte zostały prace nad opracowaniem założeń oraz elementów składowych tzw. Systemu Ciągłego Doskonalenia Phoenix Contact Wielkopolska. Ideą przewodnią tworzonego Systemu Ciągłego Doskonalenia było ujednolicenie, ustrukturyzowanie oraz ukierunkowanie wszelkich działań usprawniających realizowanych w spółce „pod parasolem” jednego spójnego systemu.
W ramach konstruowanego Systemu Ciągłego Doskonalenia zidentyfikowano kilkanaście elementów składowych, które miały stanowić o jego zawartości merytorycznej. Większość z nich odwoływała się wprost do narzędzi lean manufacturing jak: „5S”, „autonomiczne utrzymanie ruchu”, „mapowanie strumienia wartości” czy „system sugestii Kaizen”. Obok nich zidentyfikowano również takie elementy jak: „BHP”, „ochrona środowiska” czy też „przywództwo i zarządzanie”.
W efekcie kilkunastomiesięcznych prac koncepcyjnych Komitet Sterujący podjął decyzje o przebudowie struktury Systemu Ciągłego Doskonalenia tak, aby wszystkie wymagane elementy zwane odtąd FILARAMI zostały przyporządkowane do kilku większych BLOKÓW merytorycznych takich jak:
- Krótki czas przepływu
- Szczupłe procesy
- Wbudowana jakość
- Zaangażowani pracownicy
- Inspirujące przywództwo
W tym samym czasie, na etapie kształtowania docelowej zawartości oraz struktury Systemu Ciągłego Doskonalenia, Kadra Kierownicza mająca na względzie konieczność budowania kultury ciągłego doskonalenia w organizacji, podjęła decyzję o zidentyfikowaniu kluczowych zasad warunkujących oraz stymulujących ciągłe doskonalenie organizacji w długim okresie. W ten sposób, częścią Systemu Ciągłego Doskonalenia stały się również 4 zasady:
- Standardowe procesy
- Praca zespołowa
- Rzucanie wyzwań
- Idź i zobacz
Proces ten przebiegał etapowo, w następujący sposób:
Etap 1: warsztaty strategiczne: definiowanie założeń ogólnych dla Assessmentu: cele Lean Assessmentu, częstotliwość assessmentów: co 12 m-cy, częstotliwość rewizji kryteriów, etc.
Etap 2: wypracowanie merytorycznych kryteriów oceny dla wszystkich 18 Filarów Systemu Ciągłego Doskonalenia (dla poszczególnych poziomów dojrzałości na 5cio stopniowej skali 0 – 4)
Etap 3: kalibracja kryteriów oceny pomiędzy Filarami oraz ich walidacja
Etap 4: rekrutacja wewnętrzna kandydatów na assessorów wewnętrznych Phoenix Contact Wielkopolska
Etap 5: przygotowanie merytoryczne kandydatów na assessorów do pełnienia swojej roli (warsztaty)
Etap 6: realizacja 1-szego, bazowego Lean Assessment’u – assessorzy wiodący Kaizen Instutute Poland z towarzyszeniem assessorów wewnętrznych w roli obserwatorów procesu
Uzyskane efekty:
- wynik Assessmentu wskazujący całościowy poziom dojrzałości Systemu Ciągłego Doskonalenia
- wyniki cząstkowe dla poszczególnych Filarów Systemu Ciągłego Doskonalenia, wskazujące mocne strony oraz obszary wymagające doskonalenia
- kandydaci na assessorów wewnętrznych doświadczyli w praktyce swojej przyszłej roli
Tak podsumowują trwający ok.6 miesięcy proces przygotowań oraz realizację 1szego Lean Assessment’u Systemu Ciągłego Doskonalenia Phoenix Contact kluczowe osoby w tym procesie:
Lider całego przedsięwzięcia, Dyrektor Produkcji BU DC, Grzegorz Filary:
- Największą korzyścią z przeprowadzenia Lean Assessmentu jest przejrzyste, spójne i kompletne określenie kierunków rozwoju całej organizacji i całego Systemu. Opracowanie wymagań „szytych na miarę” określiło szczegółowo obraz firmy, jaką chcemy być w perspektywie kilku najbliższych lat. Ukierunkowane działania, które będziemy podejmować na podstawie Assessmentu wesprą długookresowe cele biznesowe organizacji. Jestem przekonany, że pozwoli to na zwiększenie konkurencyjności Phoenix Contact Wielkopolska na rynku.
oraz Koordynator Systemu Ciągłego Doskonalenia Phoenix Contact Wielkopolska, Michał Nowak:
- Zrealizowany w naszej firmie proces Assessment Systemu Ciągłego Doskonalenia wpłynął pozytywnie na zaangażowanie większego zespołu pracowników (ponad 100 osób, z różnych poziomów organizacji). Aktywny udział zespołów w całym procesie podniósł świadomość tego czym jest System Ciągłego Doskonalenia w naszej firmie oraz jakie wyzwania stoją przed naszą organizacją na drodze ku doskonałości. Stanowi to bardzo solidny fundament pod realizację działań w kolejnych latach.
Małgorzata Bednarek
PROFES Sp. z o.o. Sp. K./KAIZEN Institute Poland Operations
Konsultant KAIZEN
Specjalizuje się w treningach i doradztwie z zakresu metod i narzędzi ciągłego doskonalenia oraz optymalizacji procesów produkcyjnych i usługowych. Trener kompetencji miękkich jak: motywowanie, rozwiązywanie konfliktów, asertywność, zarządzanie zmianą.
Certyfikowany Black Belt Six Sigma, certyfikowany Expert Kaizen oraz Dyrektor Działu Ciągłego Doskonalenia w międzynarodowej firmie produkcyjnej w branży przemysłu ciężkiego (spawalnictwo). Praktyk z 13-letnim doświadczeniem w realizacji działań z zakresu Ciągłego Doskonalenia/Kaizen w międzynarodowej spółce produkcyjnej obejmującym: przygotowanie, realizację i nadzór nad działaniami optymalizacyjnymi procesy produkcyjne oraz usługowe (mapowanie procesów, eliminację marnotrawstwa) zarówno w skali mikro (kaizen flash) jak i makro (warsztaty kaizen).
Posiada 8-letnie praktyczne doświadczenie w projektowaniu oraz wdrażaniu systemów sugestii, kompleksowej realizacji programu 5S na obszarach produkcji oraz administracji, w realizacji działań z zakresu TPM/Autonomous Maintenance.