Do końca zmiany zostały 2 godziny. Dostaję kask i przewodnika. Słyszę: "Powinniśmy zdążyć przejść w tym czasie przez wszystkie strefy magazynu". Nie dowierzam, że zajmie to 120 minut marszu. Z zewnątrz centrum logistyczne JYSK w Radomsku wydaje się zwyczajnej wielkości. Ale całkowity obszar zajmowany przez magazyn wynosi 30 hektarów, co odpowiada powierzchni 60 boisk piłkarskich.
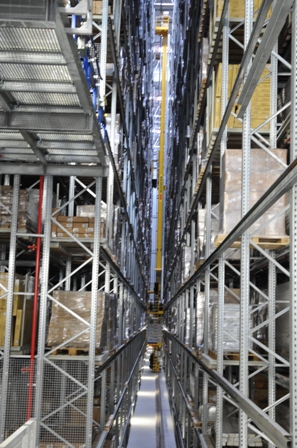
Widok nieznajomy
Centrum Logistyczne JYSK w Radomsku to największy automatyczny magazyn w Polsce. Wchodzimy. Olbrzymia hala przyjęć towaru. Trochę palet i prawie zupełnie nie widać pracowników. Co jakiś czas ciszę przerywa świst i lekkie drżenie, jak gdyby przez magazyn przejeżdżał pociąg. Żółto od barierek bezpieczeństwa, które wydzielają niebieskie urządzenia automatycznego transportu wewnętrznego SSI Schäfera. Próbuję odgadnąć, gdzie zaczyna się proces. Co na pierwszy rzut oka wcale nie jest jednoznaczne. – W przypadku tak dużej inwestycji magazynowej jak JYSK, gdzie znajduje się 169 tys. lokalizacji, a dodatkowo mamy różne wymiary i typy palet: EUR, Large, Large Box, musieliśmy zbudować w strefie przyjęć 3 stacje transferu jednostek ładunkowych do silosu – tłumaczy Bartosz Jankowski, konsultant w firmie SSI Schäfer. Transport palet do magazynu wysokiego składowania odbywa się w pełni automatycznie. Najpierw jednak towar musi dotrzeć do przypisanej mu strefy pobrań; te znajdują się na poszczególnych kondygnacjach budynku. Windy transportowe zapewniają ruch w górę i dół hali przyjęcia i wydania towaru. Poszczególne urządzenia działają niezależnie od siebie, w ten sposób osiągnięto płynność i wydajność procesu. Człowiek jest prawie niepotrzebny. A najkrócej mówiąc, jego zadania są inne, niż w tradycyjnym magazynie. To w Polsce niecodzienny widok, ponieważ magazyny automatyczne z powodów ekonomicznych nadal stanowią margines inwestycji. Dzisiaj na jego budowę potrzeba od kilku do kilkudziesięciu milionów euro. Jednak mimo tej wysokiej ceny znajdują się inwestorzy, dla których ważniejsza od pieniędzy jest wydajność osiągana dzięki automatyzacji.
Konieczna selekcja
W magazynach automatycznych istotną rolę odgrywa odpowiednia jakość palet drewnianych oraz zwartość ułożonych na nich towarów. Mają one bezpośredni wpływ na bezpieczeństwo i ciągłość procesów. Zablokowanie się uszkodzonej palety w silosie, unieruchamia część instalacji. Podobne skutki dla jego pracy może mieć, nadmierny nawis ładunku poza obrys palety. To główne powody, dla których standardowo przy instalacjach automatycznych stosowane są stanowiska kontroli jakości używanych palet, a także urządzenia sprawdzające wymiary i wagę jednostki ładunkowej, mającej trafić do magazynu.
Stanowisko pomiarowe palet porównuje cechy fizyczne z wzorcem i selekcjonuje na trzy kategorie: A, B, C. Dwie pierwsze nadają się do użytku, ostatnie to drewniany złom. Chcę sprawdzić, jak działa taki system selekcji. Na bieżni rolkowej stawiamy stos palet. Urządzenie rozpoczyna pracę, pobierając paletę po palecie na stanowisko pomiarowe. W kilka sekund bada jakość palety. Porównuje jej cechy fizyczne z wzorcem. Selekcjonuje na trzy kategorie: A, B, C. Dwie pierwsze nadają się do użytku, ostatnia to drewniany złom. Precyzja, z jaką pracuje maszyna, jest olbrzymia. Bezwzględnie potrafi wyeliminować z obiegu nawet nowe palety, których deski odbiegają od normy wymiarowej z powodu nadmiernego zawilgocenia. Ta zimna bezwzględność gwarantuje, że w magazynie wysokim ruch odbywa się płynnie, bez awarii, których źródłem mogłaby być uszkodzona paleta.
W innym miejscu trwają sprawdzenia poprawności jednostek ładunkowych. Przez bramkę kontrolną musi przejść każda trafiająca do magazynu paleta. Nie ma możliwości oszukania systemu, ponieważ to równocześnie punkt startowy transportu wewnętrznego. Ładunki zjeżdżają po chwilowej analizie do stacji wind. Jeden z ładunków przenośnik kieruje w drugą stronę. "Stanowiska kontrolne posiadają bufory, gdzie transportowane są te jednostki, w których system stwierdził odstępstwo wymiarowe. Nie blokując systemu, można w tym miejscu poprawić ułożenie ładunku. W ostateczności trzeba go ponownie uformować na innej palecie." – opowiada Bartosz Jankowski.
Strategiczna decyzja
Bramki kontrolne jednostek paletowych - czujniki analizują prawidłowość ułożenia palet. JYSK zdecydował się na lokalizację w Polsce magazynu, który pełni funkcję centrum logistycznego dla sieci sklepów tej marki w Europie Środkowo-Wschodniej. "Pod wieloma względami JYSK Polska działa jako zaplecze do zaopatrzenia w tym regionie, a centrum dystrybucyjne w Radomsku będzie podstawą systemu dostaw dla całego regionu." – powiedział Jan Bogh, Dyrektor Zarządzający JYSK Nordic podczas wkopania kamienia węgielnego pod centrum w 2010 roku.
Sieć sklepów JYSK znana jest w całej Europie, gdzie klienci kupować mogą w 1 550 sklepach artykuły wyposażenia mieszkań. Obroty firmy sięgają 2 miliardów euro, a zatrudnionych jest w nich 14 000 pracowników. W Polsce firma obecna jest od 2000 roku, kiedy otworzyła siedzibę w Gdańsku; po niespełna dziesięciu latach obecności na polskim rynku posiada pokaźną sieć ponad 120 sklepów. Potrzeby rozwijającej się sieci stale rosną. "Centrum dystrybucyjne zaopatrywać będzie nie tylko rynek polski, ale także sklepy na Węgrzech, w Czechach, Słowacji, Słowenii, Chorwacji, a niedługo również w Bośni. Z działu detalicznego otrzymałem informację, że sklepy korzystające z usług centrum są zadowolone ze współpracy, zarówno pod względem administracyjnym, jak i operacyjnym." – powiedział Henryk Bogelund, Dyrektor Logistyki JYSK Nordic. Lars Larsen, właściciel JYSK, określił projekt budowy magazynu w Radomsku mianem „niezbędnej inwestycji w przyszłość”.
Dwa silosy
Magazyn wysokiego składowania w centrum logistycznym JYSK stanowią dw niezlaezne silosy o wysokości prawie 40 m. Instalację obsługują 24 dwumasztowe układnice SSC 2x 1000.38-2-DD o nośności 2 x 1000 kg. Każda z nich została wyposażona w teleskopowe widły na podwójną głębokość Zasadniczy magazyn wysoki w centrum logistycznym JYSK stanowią dwa niezależne silosy o wysokości prawie 40 m i długości średnio po 150 m. W każdym z 2 silosów znajduje się po 12 korytarzy, w sumie 24, po jednym na układnice. To z tego miejsca dochodził świst – efekt jazdy po szynach 24 dwumasztowych automatycznych układnic SSC 2x 1000.38-2-DD o nośności 2 x 1000 kg. Każda z nich została wyposażona w teleskopowe widły na podwójną głębokość, w ten sposób obsługuje po dwa gniazda paletowe z każdego boku. – Dwa korytarze robocze przeznaczono dla boxów large (dł. 280 cm) z obsługą z poziomu parteru. W pozostałych składowane są palety o 5 różnych wysokościach (120, 170, 220, 240, 280 cm). Średnia wydajność, biorąc pod uwagę różnej długości korytarze, wynosi około 20 podwójnych cykli na układnice w trakcie godziny pracy – opowiada Bartosz Jankowski. Układnice wstawiono do silosów przez dach, kiedy samonośna konstrukcja hali była ukończona. Patrząc na nie z poziomu zero, są monstrualnie wysokie, sięgają do spodu konstrukcji dachu, gdzie wysokość wynosi 37,8 m. Przy starcie wzbudzają powiew powietrza i z nieprawdopodobną lekkością i gracją ich kilkunastotonowa konstrukcja pokonuje długie odcinki korytarza, błyskawicznie ginąc w ciemności na jego końcu. Słychać tylko szmer, który świadczy, że gdzieś w oddali trwa operacja wkładania lub wyjmowania ładunku.
Obszar newralgiczny
Pojemny magazyn wysoki potrzebuje wydajnego systemu transportu wewnętrznego. W innym razie pojawi się wąskie gardło. Co z tego, że potrafimy dużo zmagazynować, jeśli nie potrafilibyśmy szybko skorzystać z tych zasobów? Sprawy nie załatwi wprowadzenie w taki układ floty wózków widłowych. Nie ma takich, które zapewnią wydajność na poziomie 300 palet na godzinę. Automatyzacja procesów dotyczy bezwzględnie wszelkich obszarów. Tu nie ma miejsca na rozwiązania pośrednie. Jak zatem wydać tak dużą liczbę palet? SSI Schäfer rozwiązał kwestię transferu z obszaru przyjęć do magazynu wysokiego, projektując system Monorail. Działa on dwukierunkowo, zapewniając transfer ładunków z silosu do strefy wydań. To rodzaj bezzałogowej szynowej kolejki, którą zaprojektowano na każdym z dwóch poziomów magazynu. Na dwóch poziomach pracuje kilkadziesiąt wózków, które posiadają na swych platformach przenośniki łańcuchowe. Platformy krążą w pętli między poszczególnymi stacjami magazynu, przenosząc jednostki paletowe. System Monorail ma wydajność po 275 palet w podwójnym cyklu na poziomie transportowym, a więc 550 palet w podwójnym cyklu, czyli 1.100 palet w sumie transportowanych na godzinę.
Transfer z obszaru przyjęć do magazynu wysokiego składowania zapewnia system Monorail. Na dwóch poziomach pracuje kilkadziesiąt bezzałogowych wózków, które posiadają na swych platformach przenośniki łańcuchowe. Sercem każdego magazynu automatycznego jest system informatyczny, to jego funkcjonalności pozwalają zarządzać lokalizacjami w magazynie wysokim oraz wszystkimi pozostałymi strefami wewnętrznymi w centrum logistycznym. W JYSK zainstalowano aplikację autorską SSI Schäfer pod nazwą ant, który współpracuje z systemem SAP. Oprogramowanie obsługuje zarówno operacje magazynowe, jak również steruje urządzeniami automatycznymi.
JYSK zyskał centrum o powierzchni 100 000 mkw., którego potencjał zapewni właściwą obsługę rynku Europy Środkowej i Wschodniej, SSI Schäfer natomiast doskonałą referencję, ponieważ magazyn w Radomsku w tej chwili należy uznać za największy automatyczny magazyn w Polsce. Aby obejść wszystkie jego strefy, potrzebowałem ponad 3 godzin.
Krzysztof Pograniczny
Więcej o SSI Schäfer - http://www.ssi-schaefer.pl/